Pressure sintering is a specialized process used to create dense, high-strength materials by combining heat and pressure. It involves preparing a powder compact, heating it to a temperature below its melting point, and applying external pressure to enhance densification and reduce porosity. This process is particularly effective for materials like ceramics and metals, where achieving low porosity and high mechanical strength is critical. The steps typically include powder preparation, mixing, forming, sintering under pressure, and post-treatment. Pressure sintering can be performed in various environments, such as vacuum or inert atmospheres, to prevent oxidation and ensure material integrity.
Key Points Explained:
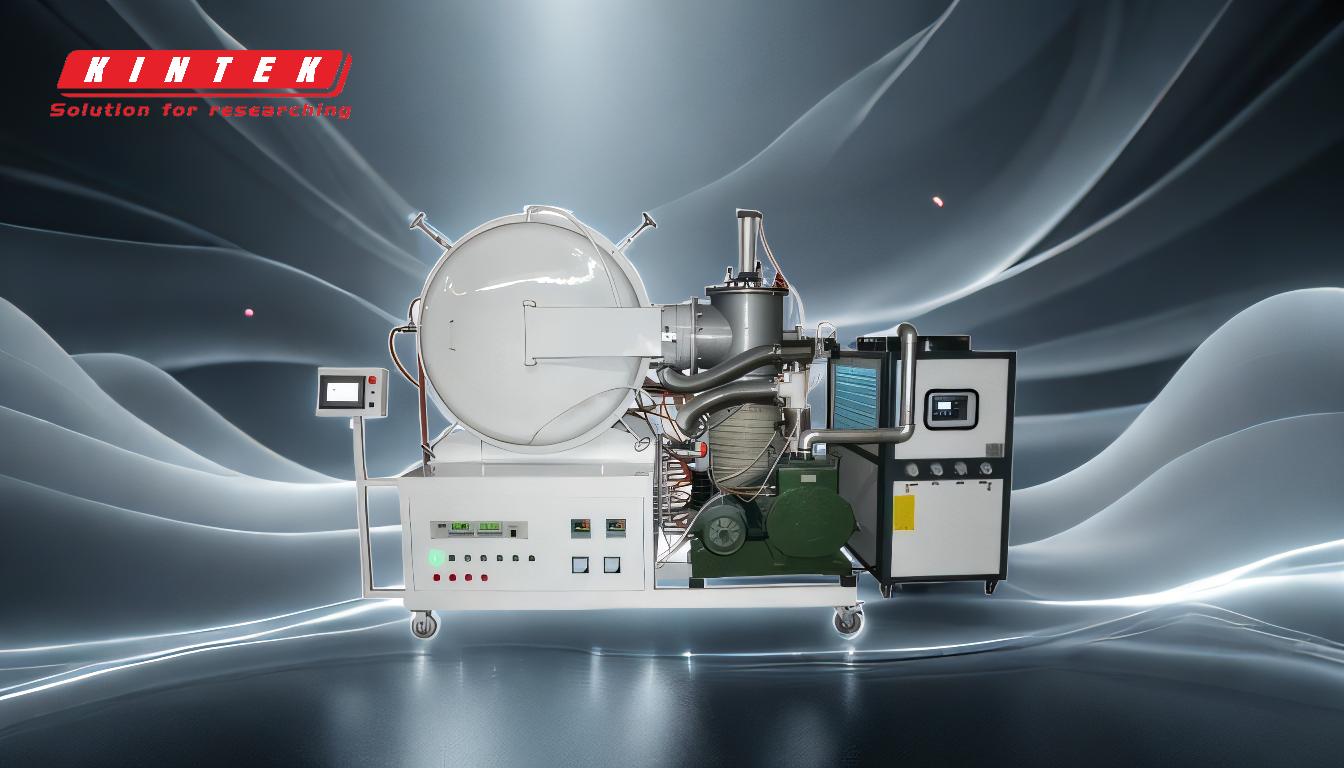
-
Preparation of Powder Compact:
- The process begins with the preparation of a powder compact, which involves mixing powdered materials with bonding agents or coupling agents to ensure uniformity.
- The powder is then pressed into the desired shape using tools like cold welds, 3D-printed lasers, or pressing tools in a controlled atmosphere.
- This step is crucial for achieving the initial shape and density of the material before sintering.
-
Heating and Consolidation:
- The compacted powder is heated to a temperature just below its melting point. This temperature is carefully controlled to activate the sintering process without causing complete melting.
- During heating, the bonding agent (often a wax or polymer) evaporates or burns away, leaving the primary particles to begin fusing at their surfaces.
- In some cases, an intermediate bonding agent, such as bronze, melts and couples between the particles, leaving the primary component powder unaltered.
-
Application of External Pressure:
- Unlike traditional sintering, pressure sintering involves the application of external pressure during the heating process. This pressure helps to reduce porosity and accelerate the densification of the material.
- The pressure can be applied in various ways, such as through mechanical presses or hydraulic systems, depending on the specific requirements of the material being sintered.
- The combination of heat and pressure ensures that the particles merge more effectively, resulting in a denser and more uniform final product.
-
Particle Merging and Densification:
- As the temperature rises, the particles begin to merge at their surfaces, a process known as solid-phase sintering. This can be further accelerated by the presence of a liquid phase, known as liquid-phase sintering (LPS).
- In LPS, a liquid phase forms between the particles, enhancing the sintering speed and modifying the fracture modes of the material. This results in improved material properties, such as increased toughness and reduced porosity.
- The application of pressure during this stage ensures that the particles are forced closer together, further reducing voids and enhancing the material's density.
-
Cooling and Solidification:
- After the sintering process is complete, the material is gradually cooled to room temperature. This cooling phase is critical for ensuring that the material solidifies into a unified mass without developing internal stresses or cracks.
- The cooling rate is carefully controlled to prevent thermal shock, which could otherwise lead to material failure.
- Once cooled, the material undergoes post-treatment processes, such as machining or surface finishing, to achieve the final desired properties and dimensions.
-
Environmental Considerations:
- Pressure sintering is often performed in a vacuum or inert atmosphere to prevent oxidation and contamination of the material. This is particularly important for materials like silicon carbide, which require high purity and stability.
- The use of a controlled environment ensures that the material retains its desired properties and does not degrade during the sintering process.
-
Advantages of Pressure Sintering:
- Reduced Porosity: The application of pressure significantly reduces the porosity of the sintered material, resulting in a denser and stronger final product.
- Improved Mechanical Properties: The combination of heat and pressure enhances the mechanical properties of the material, such as hardness, strength, and wear resistance.
- Lower Sintering Temperatures: In some cases, pressure sintering allows for lower sintering temperatures compared to traditional methods, which can be beneficial for materials that are sensitive to high temperatures.
- Faster Sintering Times: The application of pressure can reduce the overall sintering time, making the process more efficient and cost-effective.
In summary, pressure sintering is a highly effective method for producing dense, high-performance materials. By combining heat and pressure, this process enhances the densification and mechanical properties of the material, making it suitable for a wide range of industrial applications. The careful control of each step, from powder preparation to cooling, ensures that the final product meets the required specifications and performance criteria.
Summary Table:
Key Steps in Pressure Sintering | Details |
---|---|
Powder Preparation | Mixing and compacting powdered materials with bonding agents. |
Heating and Consolidation | Heating below melting point to activate sintering. |
Application of External Pressure | Applying pressure to reduce porosity and enhance densification. |
Particle Merging | Solid-phase or liquid-phase sintering for improved material properties. |
Cooling and Solidification | Controlled cooling to prevent cracks and ensure material integrity. |
Environmental Considerations | Performed in vacuum or inert atmospheres to prevent oxidation. |
Advantages | Reduced porosity, improved mechanical properties, lower sintering temperatures, and faster sintering times. |
Discover how pressure sintering can optimize your material production—contact our experts today!