Sintering in powder metallurgy is a critical heat treatment process that transforms metal powders into solid, durable components. It involves heating compacted metal powder to a temperature just below its melting point, allowing particles to bond and densify without fully liquefying. This process enhances the material's strength, reduces porosity, and improves structural integrity. The sintering process typically includes steps such as powder selection, compaction, heating, and post-treatment, with controlled atmospheres and specific temperatures tailored to the metal type. The result is a high-quality, cohesive product suitable for various industrial applications.
Key Points Explained:
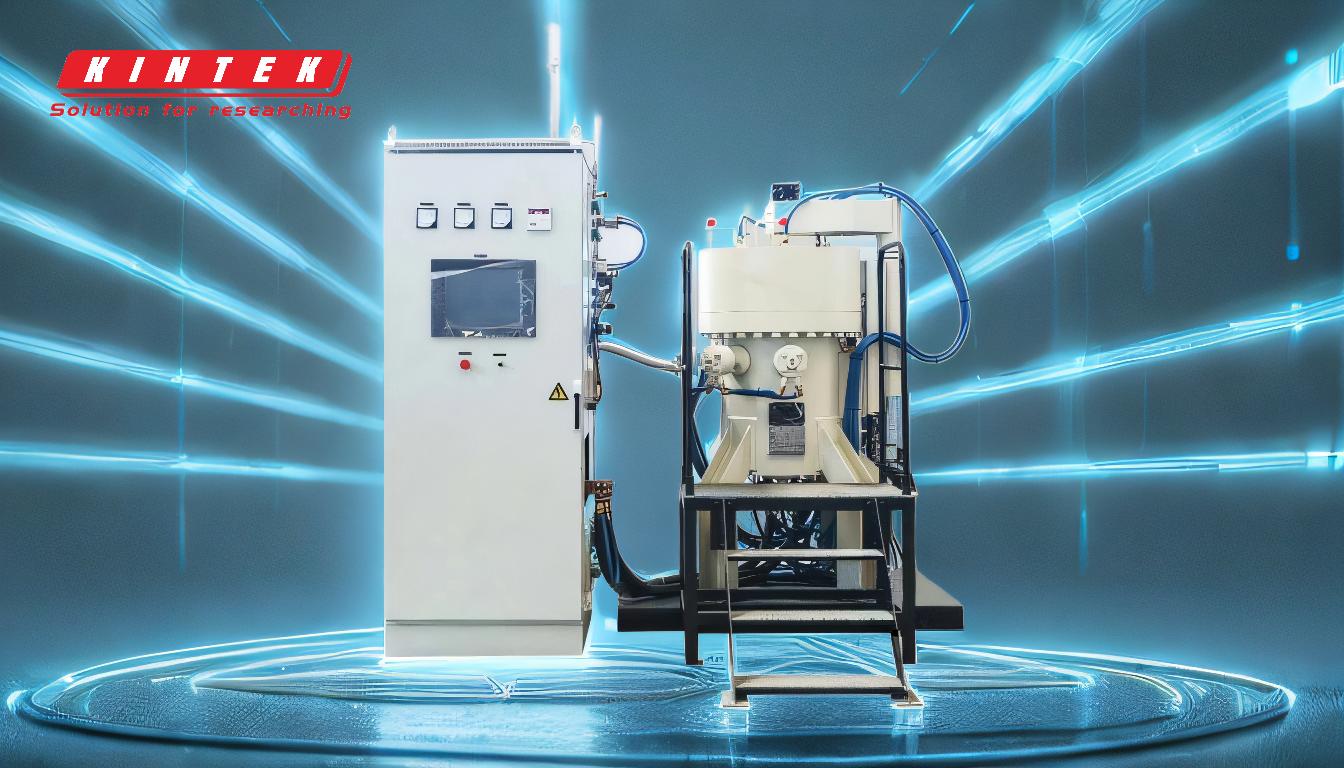
-
Definition and Purpose of Sintering
- Sintering is a heat treatment process used in powder metallurgy to bond metal particles together, forming a solid and coherent structure.
- The primary goal is to increase the material's strength, reduce porosity, and achieve the desired shape and properties.
- It is performed at temperatures slightly below the metal's melting point to prevent complete liquefaction while enabling particle bonding.
-
Steps in the Sintering Process
-
Powder Selection and Preparation:
- The process begins with selecting the appropriate metal powder composition, which determines the final product's properties. Common metals include iron, nickel, molybdenum, and copper.
- Lubricants or coupling agents may be added to improve compaction and bonding.
-
Compaction:
- The metal powder is pressed into a specific shape using a die press, forming a "green" part with initial strength.
- Compaction ensures uniform density and shape before sintering.
-
Sintering:
- The green part is heated in a controlled atmosphere furnace to a temperature just below the metal's melting point.
- During heating, particles bond through diffusion, reducing porosity and increasing density.
- Liquid phase sintering (LPS) may be used to accelerate particle merging in some cases.
-
Post-Treatment:
- After sintering, the part may undergo additional processes like machining, coating, or heat treatment to enhance its properties or achieve specific tolerances.
-
Powder Selection and Preparation:
-
Key Mechanisms in Sintering
-
Particle Bonding:
- At high temperatures, metal particles form bonds through solid-state diffusion, creating a cohesive structure.
-
Porosity Reduction:
- Sintering reduces the number of voids between particles, improving the material's density and mechanical properties.
-
Microstructural Changes:
- The process activates martensitic crystalline microstructures, contributing to the material's strength and hardness.
-
Particle Bonding:
-
Factors Influencing Sintering
-
Temperature and Time:
- The sintering temperature must be carefully controlled to ensure proper bonding without melting the material.
- Longer sintering times may improve bonding but can also lead to grain growth, affecting the material's properties.
-
Atmosphere Control:
- A controlled atmosphere (e.g., hydrogen, nitrogen, or vacuum) prevents oxidation and ensures optimal bonding conditions.
-
Powder Characteristics:
- Particle size, shape, and composition significantly impact the sintering process and final product quality.
-
Temperature and Time:
-
Applications and Benefits
- Sintering is widely used in industries such as automotive, aerospace, and electronics to produce complex, high-strength components.
- Benefits include cost-effectiveness, the ability to create intricate shapes, and the production of materials with tailored properties.
- The process is particularly valuable for manufacturing parts with low porosity, high durability, and excellent mechanical performance.
By understanding the sintering process and its key steps, manufacturers can optimize the production of powder metallurgy components, ensuring high-quality results for a wide range of applications.
Summary Table:
Key Aspect | Details |
---|---|
Definition | Heat treatment process bonding metal particles into a solid structure. |
Steps | Powder selection, compaction, heating, and post-treatment. |
Key Mechanisms | Particle bonding, porosity reduction, and microstructural changes. |
Influencing Factors | Temperature, time, atmosphere control, and powder characteristics. |
Applications | Automotive, aerospace, electronics, and more. |
Benefits | Cost-effectiveness, intricate shapes, low porosity, and high durability. |
Optimize your powder metallurgy process with expert guidance—contact us today!