Vacuum Arc Remelting (VAR) is a specialized metallurgical process used to refine and purify metals, particularly high-performance alloys. It involves melting a metal electrode under a vacuum using a direct current (DC) arc, which generates extremely high temperatures. The molten metal forms droplets that fall into a water-cooled copper mold, where it solidifies into a high-purity, homogeneous ingot. This process is critical for producing materials with superior mechanical properties, reduced impurities, and improved microstructure, making it essential for aerospace, medical, and energy applications.
Key Points Explained:
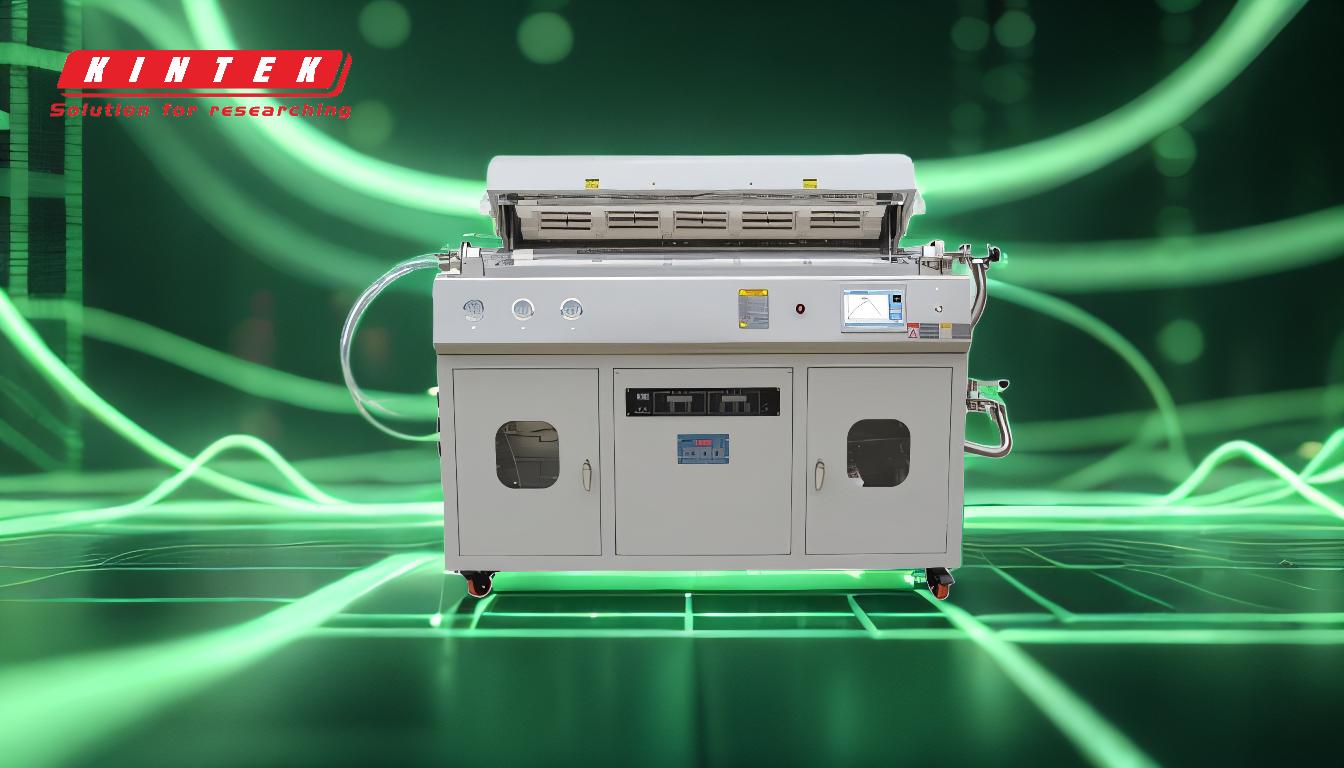
-
Overview of the VAR Process:
- Vacuum Arc Remelting (VAR) is a secondary refining process used to produce high-quality alloys.
- It operates under a vacuum to prevent contamination and oxidation, ensuring the purity of the final product.
- The process is particularly effective for refining refractory metals and their alloys, such as titanium, nickel, and superalloys.
-
Key Components of a Vacuum Arc Furnace:
- Electrode: The starting material, typically an impure alloy, is shaped into an electrode.
- DC Arc: A direct current arc is used to generate the high temperatures required for melting the electrode.
- Water-Cooled Copper Mold: The molten metal solidifies in this mold, which is cooled by water to control the solidification rate and microstructure.
- Vacuum Chamber: The entire process occurs in a vacuum environment to eliminate impurities and gases.
-
Step-by-Step Process:
- Loading the Electrode: The electrode is loaded into the furnace chamber and positioned above the copper mold.
- Creating a Vacuum: The chamber is evacuated to remove oxygen and other gases, ensuring a contamination-free environment.
- Melting the Electrode: A DC arc is struck between the electrode and the molten pool, melting the tip of the electrode.
- Droplet Formation and Refining: As the electrode melts, droplets fall through the vacuum and pass through the high-temperature arc zone (up to 5000K), where physical and chemical reactions refine the metal.
- Solidification: The molten metal solidifies in the water-cooled copper mold, forming a high-purity ingot with a controlled microstructure.
-
Advantages of VAR:
- Improved Purity: The vacuum environment and high-temperature refining remove impurities and gases, resulting in a cleaner alloy.
- Enhanced Microstructure: The controlled solidification process produces a uniform and fine-grained structure, improving mechanical properties.
- Superior Performance: VAR-processed alloys exhibit better fatigue resistance, strength, and corrosion resistance, making them ideal for critical applications.
-
Applications of VAR-Processed Alloys:
- Aerospace: VAR is used to produce turbine blades, engine components, and other critical parts that require high strength and reliability.
- Medical: Implants and surgical instruments made from VAR-refined alloys benefit from their biocompatibility and durability.
- Energy: Alloys used in nuclear reactors and power generation equipment are often processed using VAR to ensure safety and performance.
-
Challenges and Considerations:
- Cost: The VAR process is expensive due to the need for specialized equipment and a controlled environment.
- Process Control: Precise control of parameters such as arc current, vacuum level, and cooling rate is essential to achieve the desired material properties.
- Material Limitations: While VAR is highly effective for certain alloys, it may not be suitable for all materials.
-
Comparison with Other Refining Processes:
- VAR is often compared to processes like Electroslag Remelting (ESR) and Induction Melting. While ESR also refines metals, it uses a slag layer rather than a vacuum, which can introduce impurities. Induction melting, on the other hand, does not provide the same level of purification as VAR.
-
Future Trends in VAR Technology:
- Advances in automation and process monitoring are improving the efficiency and consistency of VAR.
- Research is ongoing to expand the range of materials that can be processed using VAR, including new high-entropy alloys and composites.
By understanding the intricacies of the VAR process, manufacturers and purchasers can make informed decisions about the production and selection of high-performance alloys for demanding applications.
Summary Table:
Aspect | Details |
---|---|
Process Overview | Refines metals under vacuum using a DC arc to produce high-purity alloys. |
Key Components | Electrode, DC arc, water-cooled copper mold, vacuum chamber. |
Step-by-Step Process | Loading electrode → Creating vacuum → Melting → Refining → Solidification. |
Advantages | Improved purity, enhanced microstructure, superior mechanical properties. |
Applications | Aerospace, medical implants, energy equipment. |
Challenges | High cost, precise process control, material limitations. |
Discover how vacuum arc remelting can elevate your alloy production—contact our experts today!