Vacuum deposition coating is a sophisticated process used to apply thin layers of material onto a substrate in a controlled, high-vacuum environment. This method ensures precise, high-quality coatings with applications ranging from corrosion protection to optical and decorative finishes. The process involves creating a vacuum to eliminate interfering gases, preparing the substrate, evaporating or sputtering the coating material, depositing it onto the substrate, and cooling the system. It is widely used in industries such as electronics, automotive, and energy due to its ability to produce uniform, durable, and functional coatings at the atomic or molecular level.
Key Points Explained:
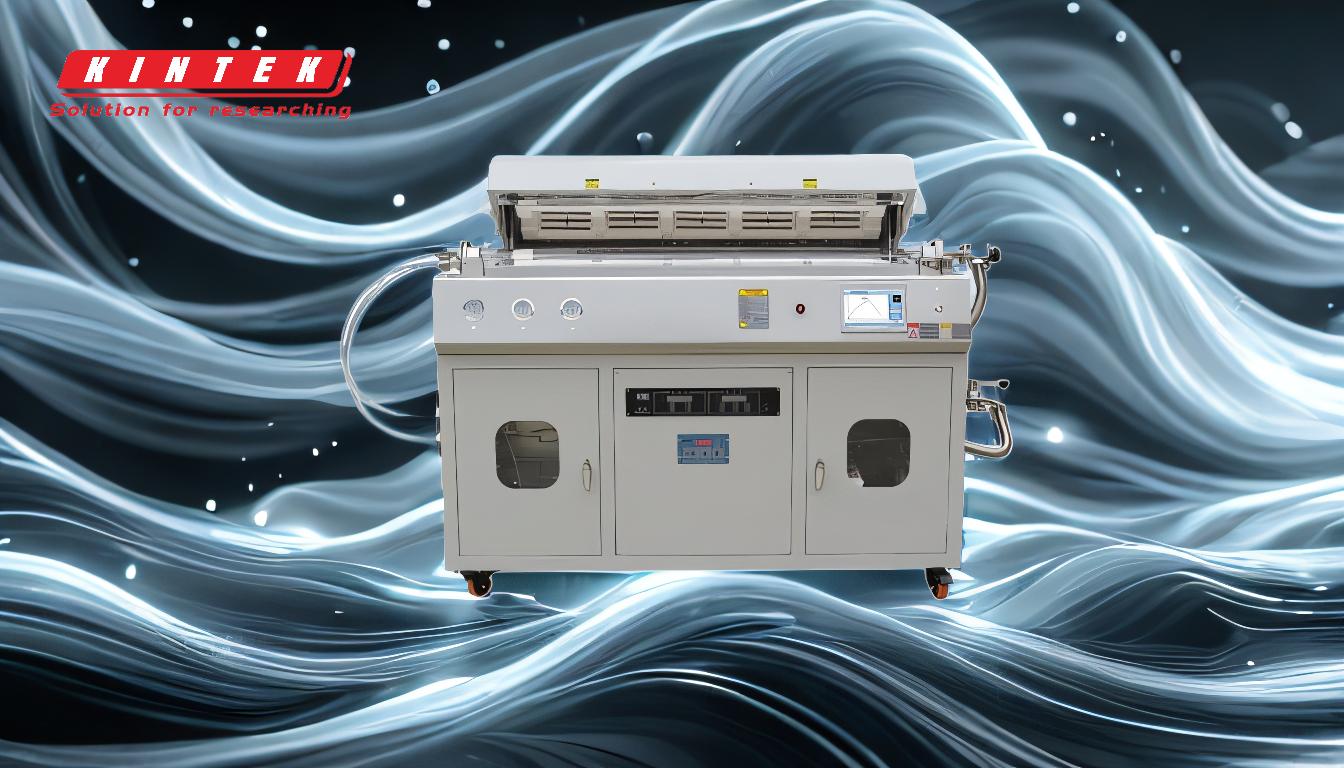
-
Creating a Vacuum Environment
- The first step in vacuum deposition is creating a vacuum inside the deposition chamber. This eliminates air and gases that could interfere with the deposition process or contaminate the coating.
- A high vacuum ensures that the coating material can travel freely to the substrate without collisions with gas molecules, resulting in a uniform and high-quality film.
- The vacuum environment also reduces oxidation and other chemical reactions that could degrade the coating's performance.
-
Substrate Preparation
- Before deposition, the substrate must be thoroughly cleaned and treated to ensure proper adhesion of the coating material.
- Cleaning methods may include ultrasonic cleaning, chemical treatments, or plasma cleaning to remove contaminants like oils, dust, or oxides.
- Surface treatments, such as etching or applying adhesion-promoting layers, may also be used to enhance the bond between the substrate and the coating.
-
Evaporation or Sputtering of Coating Material
- The coating material is introduced into the vacuum chamber in one of two primary ways: evaporation or sputtering.
- Evaporation: The material is heated until it vaporizes, either through resistive heating, electron beams, or laser ablation. The vaporized atoms or molecules then travel through the vacuum and deposit onto the substrate.
- Sputtering: High-energy ions (often argon) are used to bombard a target material, knocking off atoms or molecules that then deposit onto the substrate.
- Both methods allow precise control over the thickness and composition of the deposited layer, even down to the nanometer scale.
- The coating material is introduced into the vacuum chamber in one of two primary ways: evaporation or sputtering.
-
Deposition of the Coating
- The vaporized or sputtered material travels through the vacuum and adheres to the substrate, forming a thin film.
- The deposition process can be controlled to achieve specific film properties, such as thickness, uniformity, and microstructure.
- Shutters, deposition rate monitors, and heaters may be used to fine-tune the process and ensure consistent results.
-
Cooling and Venting the System
- After the deposition is complete, the system is allowed to cool down to prevent thermal stress on the substrate or coating.
- The vacuum chamber is then vented to allow the coated substrate to be removed safely.
- Proper cooling and venting are critical to maintaining the integrity of the coating and ensuring the system is ready for the next cycle.
-
Applications of Vacuum Deposition
- Vacuum deposition is used in a wide range of industries and applications, including:
- Optical Coatings: Anti-reflective, mirror, and interference coatings for lenses, mirrors, and displays.
- Decorative Coatings: Metallic or colored finishes for consumer products.
- Wear-Resistant Coatings: Hard, durable layers for tools and machinery.
- Corrosion Protection: Thin films that protect metals from environmental degradation.
- Semiconductor Devices: Precise layers for electrical conduction and insulation.
- Solar Cells: Thin-film photovoltaic materials for energy generation.
- The versatility of vacuum deposition makes it a cornerstone of modern materials science and engineering.
- Vacuum deposition is used in a wide range of industries and applications, including:
By following these steps, vacuum deposition coating achieves highly controlled and reproducible results, making it an essential technology for producing advanced materials and coatings in various industries.
Summary Table:
Step | Description |
---|---|
1. Creating a Vacuum | Eliminates air and gases to ensure a contaminant-free environment for uniform coating deposition. |
2. Substrate Prep | Cleaning and treating the substrate to enhance adhesion of the coating material. |
3. Evaporation/Sputtering | Coating material is vaporized or sputtered to create a thin film. |
4. Deposition | Coating material adheres to the substrate, forming a precise, uniform layer. |
5. Cooling & Venting | System cools down to prevent thermal stress; chamber is vented for safe substrate removal. |
6. Applications | Used in optical, decorative, wear-resistant, corrosion protection, semiconductor, and solar cells. |
Discover how vacuum deposition coating can transform your materials—contact our experts today!