Vacuum heat treatment is a specialized process used to harden metals by heating them in a vacuum environment. This method ensures that no air or contaminants interfere with the treatment, leading to more predictable and superior results. The process involves placing the metal in a sealed chamber, removing air using a vacuum pump, and then heating the metal to the desired temperature. This technique is particularly beneficial for materials that are sensitive to oxidation or require precise control over their microstructure. Below, we will explore the key steps and considerations involved in vacuum heat treatment.
Key Points Explained:
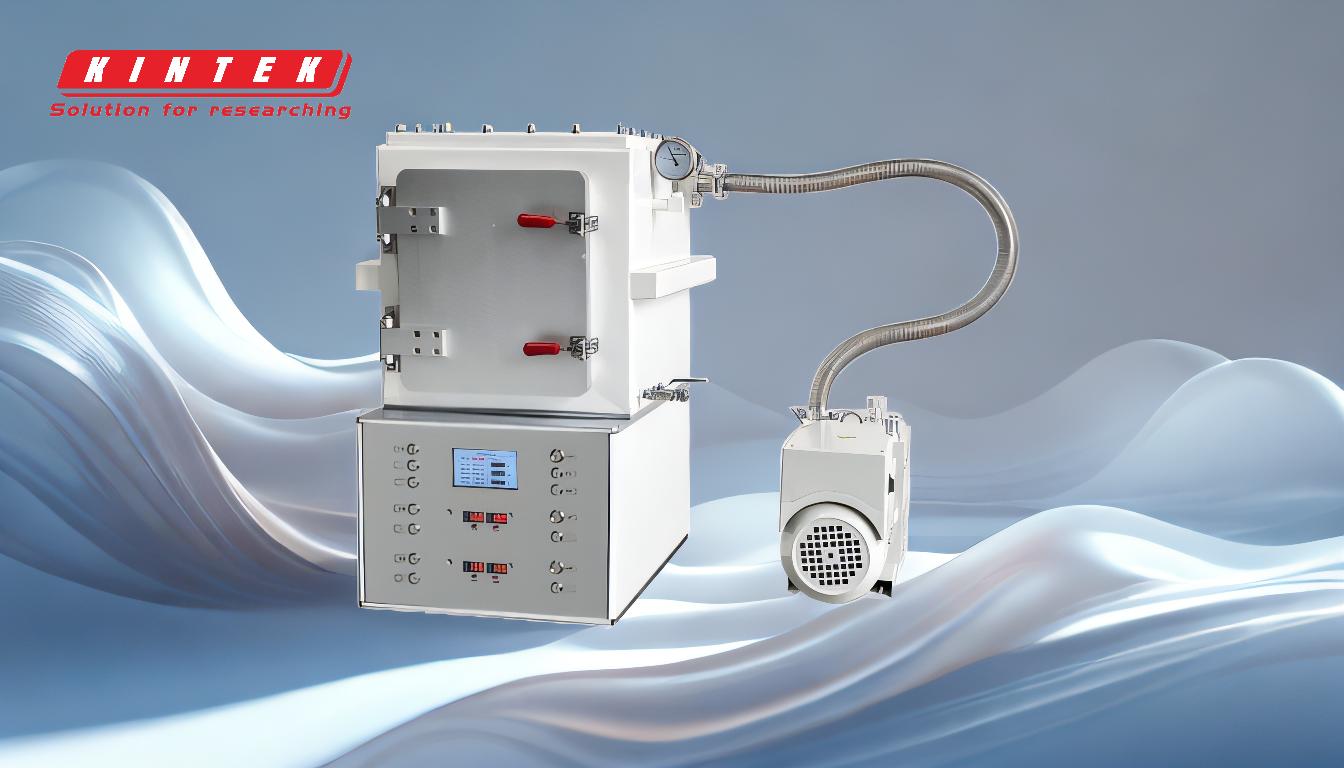
-
Understanding Vacuum Heat Treatment:
- Vacuum heat treatment is a process where metals are heated in a vacuum environment to achieve specific mechanical properties.
- The absence of air prevents oxidation and contamination, ensuring a clean and controlled environment for the treatment.
-
The Role of the Vacuum Chamber:
- The process begins by placing the metal in a sealed chamber.
- A vacuum pump is used to remove air from the chamber, creating a low-pressure environment.
- This step is crucial as it eliminates the presence of oxygen and other gases that could react with the metal during heating.
-
Heating the Metal:
- Once the chamber is evacuated, the metal is heated to a specific temperature, depending on the material and the desired outcome.
- The heating process is carefully controlled to ensure uniform temperature distribution and to prevent thermal stress.
-
Cooling and Quenching:
- After reaching the desired temperature, the metal is cooled or quenched to lock in the new microstructure.
- The cooling rate is critical and varies depending on the material and the properties required.
-
Advantages of Vacuum Heat Treatment:
- Oxidation Prevention: The vacuum environment prevents oxidation, leading to a cleaner surface finish.
- Precision Control: The process allows for precise control over temperature and cooling rates, resulting in consistent and predictable outcomes.
- Enhanced Mechanical Properties: Metals treated in a vacuum often exhibit improved hardness, strength, and wear resistance.
-
Applications of Vacuum Heat Treatment:
- This method is widely used in industries such as aerospace, automotive, and tool manufacturing.
- It is particularly beneficial for materials like titanium, stainless steel, and high-speed steels that are prone to oxidation.
-
Material Considerations:
- The materials used in vacuum heat treatment must withstand high temperatures and maintain their properties in a vacuum.
- Components like heating elements must have high resistivity, small thermal expansion coefficients, and good mechanical strength at elevated temperatures.
-
Comparison with Other Heat Treatment Methods:
- Unlike traditional heat treatment methods that use air or gas atmospheres, vacuum heat treatment offers a cleaner and more controlled environment.
- This results in fewer defects and a higher quality finish compared to conventional methods.
In summary, vacuum heat treatment is a sophisticated process that offers numerous advantages over traditional methods. By understanding the key steps and considerations, manufacturers can achieve superior results and enhance the performance of their metal components. For more detailed information on vacuum heat treatment, you can explore further resources.
Summary Table:
Step | Description |
---|---|
1. Vacuum Chamber Setup | Metal is placed in a sealed chamber; air is removed using a vacuum pump. |
2. Heating | Metal is heated to a specific temperature for uniform microstructure control. |
3. Cooling/Quenching | Metal is cooled at a controlled rate to lock in desired properties. |
4. Benefits | Prevents oxidation, ensures precision, and enhances mechanical properties. |
5. Applications | Used in aerospace, automotive, and tool manufacturing for oxidation-sensitive metals. |
Discover how vacuum heat treating can improve your metal components—contact our experts today!