Hot isostatic pressing (HIP) is a manufacturing process that combines high temperature and high pressure to improve the properties of materials. It is widely used across industries such as aerospace, automotive, medical devices, and energy storage. The process involves applying uniform pressure from all directions using an inert gas like argon, while simultaneously heating the material below its melting point. This eliminates pores, increases density, and enhances material uniformity. HIP is also used for consolidating powders, healing defects in castings, and bonding materials. A related process, warm isostatic pressing, is specifically used in applications like lithium battery production, where precise temperature control is critical.
Key Points Explained:
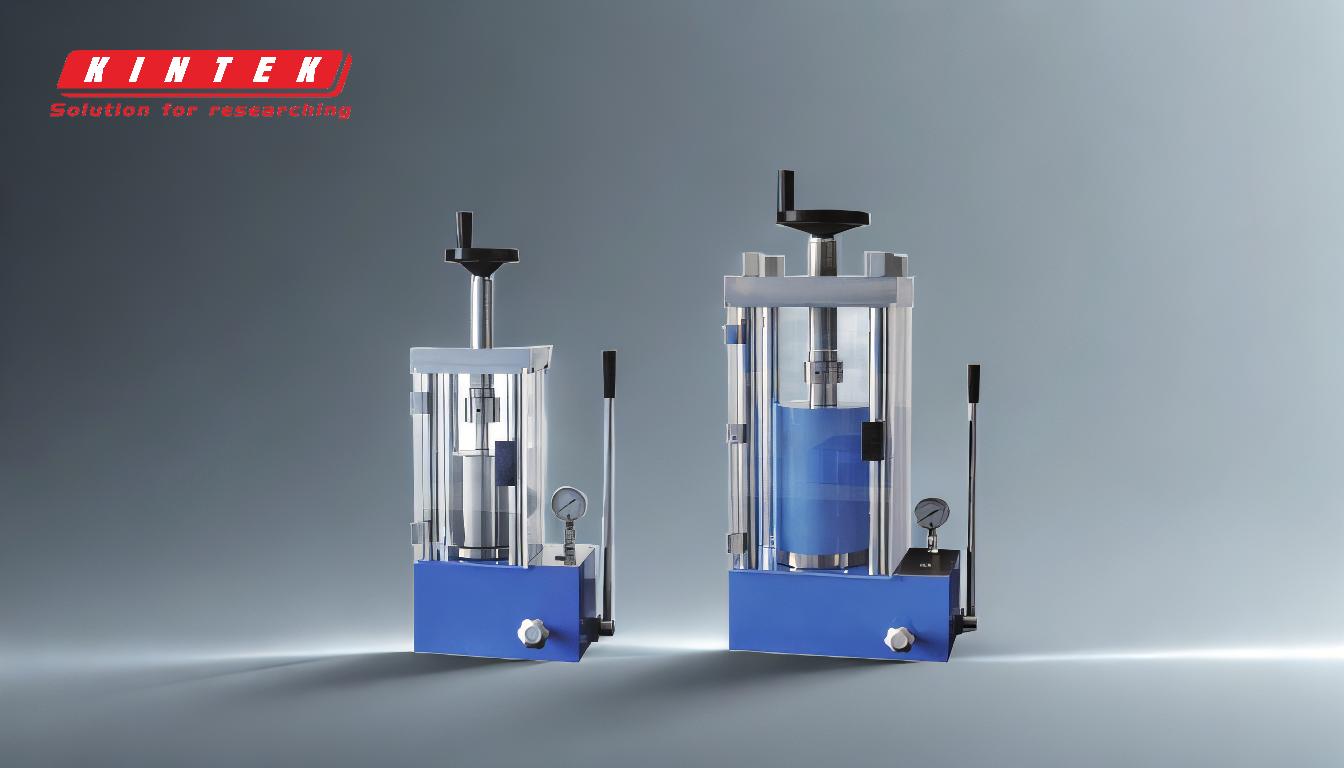
-
Purpose of Hot Isostatic Pressing (HIP):
- HIP is primarily used to eliminate internal defects such as pores and voids in materials, which improves their density and mechanical properties.
- It is also used for consolidating powders into solid components and healing defects in castings, ensuring a uniform and defect-free structure.
- The process enables the bonding or cladding of multiple materials, either in solid or powder form, creating composite materials with enhanced properties.
-
How HIP Works:
- The material is placed in a heating chamber, and inert argon gas is used to apply uniform pressure from all directions.
- Heat is applied to increase the pressure over time, typically below the material's melting point, ensuring the material does not melt but becomes more pliable.
- The combination of heat and pressure helps close gaps and pores, resulting in a denser and more uniform material structure.
-
Applications of HIP:
- Aerospace and Automotive Industries: Used to manufacture advanced ceramics and high-performance components that require high strength and durability.
- Medical Devices: Ensures the production of defect-free implants and prosthetics with superior mechanical properties.
- Energy Storage: Applied in the production of lithium-ion batteries and fuel cells, where material uniformity and density are critical.
- Oil and Gas Industry: Used to create high-performance components that can withstand extreme conditions.
-
Materials Suitable for HIP:
- HIP is applicable to a wide range of materials, including ceramics, metals, composites, plastics, and carbon. This versatility makes it a valuable process across multiple industries.
-
Warm Isostatic Pressing:
- A related process, warm isostatic press, is used in applications requiring precise temperature control, such as lithium battery production.
- In this process, a heated liquid medium is injected into a sealed pressing cylinder, with a heat generator ensuring accurate temperature control.
-
Benefits of HIP:
- Improved Material Properties: Eliminates defects, increases density, and enhances uniformity.
- Versatility: Applicable to a wide range of materials and industries.
- Enhanced Performance: Produces components with superior mechanical properties, suitable for demanding applications.
By understanding the purpose, process, and applications of hot isostatic pressing, manufacturers can leverage this technology to produce high-quality, defect-free components for a variety of industries. The related process of warm isostatic pressing further expands its utility, particularly in precision applications like energy storage.
Summary Table:
Key Aspect | Details |
---|---|
Purpose | Eliminate defects, consolidate powders, heal castings, bond materials. |
Process | High temperature + high pressure using inert gas (argon). |
Applications | Aerospace, automotive, medical devices, energy storage, oil & gas. |
Materials | Ceramics, metals, composites, plastics, carbon. |
Benefits | Improved density, uniformity, mechanical properties, and versatility. |
Interested in leveraging HIP for your industry? Contact us today to learn more!