Quenching aluminum is a critical process in metallurgy aimed at rapidly cooling the metal to achieve specific mechanical and structural properties. This process is essential for enhancing the hardness, strength, and durability of aluminum alloys, making them suitable for various industrial applications. By controlling the cooling rate, quenching helps to lock in the desired microstructure, preventing the formation of unwanted phases that could weaken the material. This summary provides a foundational understanding of why quenching is indispensable in aluminum processing.
Key Points Explained:
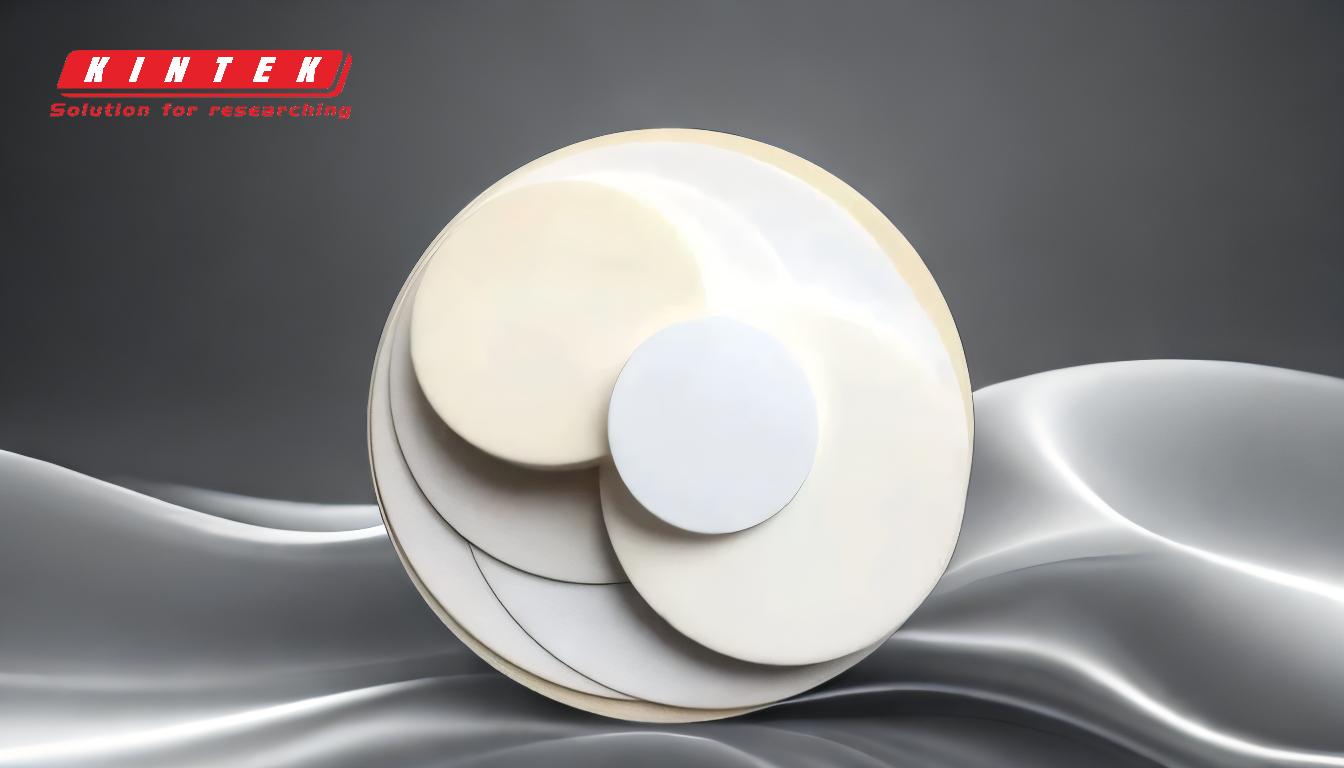
-
Enhancing Mechanical Properties:
- Quenching aluminum significantly improves its mechanical properties, such as hardness and strength. When aluminum is heated to a high temperature, its microstructure becomes more malleable. Rapid cooling through quenching locks this structure in place, preventing the formation of softer phases that would otherwise reduce the material's strength.
-
Preventing Unwanted Phase Formation:
- During the cooling process, aluminum can form different phases depending on the cooling rate. Slow cooling can lead to the formation of softer, less desirable phases. Quenching ensures that the aluminum cools quickly enough to avoid these phases, maintaining a more uniform and desirable microstructure.
-
Improving Durability and Wear Resistance:
- The rapid cooling achieved through quenching not only enhances hardness but also improves the overall durability and wear resistance of aluminum. This makes quenched aluminum ideal for applications where the material is subjected to high stress and friction, such as in automotive and aerospace components.
-
Achieving Desired Microstructure:
- The microstructure of aluminum plays a crucial role in determining its properties. Quenching allows for precise control over this microstructure, ensuring that the final product has the desired characteristics. This is particularly important in industries where material performance is critical.
-
Application in Heat Treatment Processes:
- Quenching is often a key step in the heat treatment of aluminum alloys. After being heated to a specific temperature, the aluminum is rapidly cooled to achieve the desired properties. This process is essential for creating high-performance materials used in various industrial applications.
-
Comparison with Other Materials:
- While quenching is commonly associated with steel, it is equally important for aluminum. Unlike steel, which is often quenched in water or oil, aluminum is typically quenched in water or air, depending on the specific alloy and desired properties.
-
Industrial Relevance:
- The ability to quench aluminum effectively is crucial for industries that rely on high-performance materials. From automotive to aerospace, the enhanced properties achieved through quenching make aluminum a versatile and reliable material for a wide range of applications.
In conclusion, quenching aluminum is a vital process that enhances its mechanical properties, prevents the formation of unwanted phases, and improves its overall durability and wear resistance. By controlling the cooling rate, quenching ensures that aluminum alloys achieve the desired microstructure, making them suitable for various high-stress applications. This process is integral to the heat treatment of aluminum, highlighting its importance in modern metallurgy and industrial applications.
Summary Table:
Key Benefit | Description |
---|---|
Enhanced Mechanical Properties | Improves hardness and strength by locking in a desirable microstructure. |
Prevents Unwanted Phases | Rapid cooling avoids softer, less desirable phases, ensuring uniform structure. |
Boosts Durability | Increases wear resistance, ideal for high-stress applications. |
Controls Microstructure | Achieves precise material properties for critical industrial uses. |
Integral to Heat Treatment | A key step in creating high-performance aluminum alloys. |
Learn how quenching aluminum can optimize your material performance—contact our experts today!