Spark Plasma Sintering (SPS) is an advanced sintering technique designed to densify ceramic and metallic powders rapidly and efficiently. It leverages the principles of electric spark discharge and Joule heating to achieve high-density materials at lower temperatures and shorter times compared to conventional sintering methods. The process involves applying a pulsed direct current (DC) through a conductive die and the material itself, generating localized high temperatures and plasma that facilitate particle bonding and densification. SPS is particularly advantageous for producing materials with enhanced properties, such as nanostructured or high-density composites, and is widely used in applications ranging from electronics to biomedical engineering.
Key Points Explained:
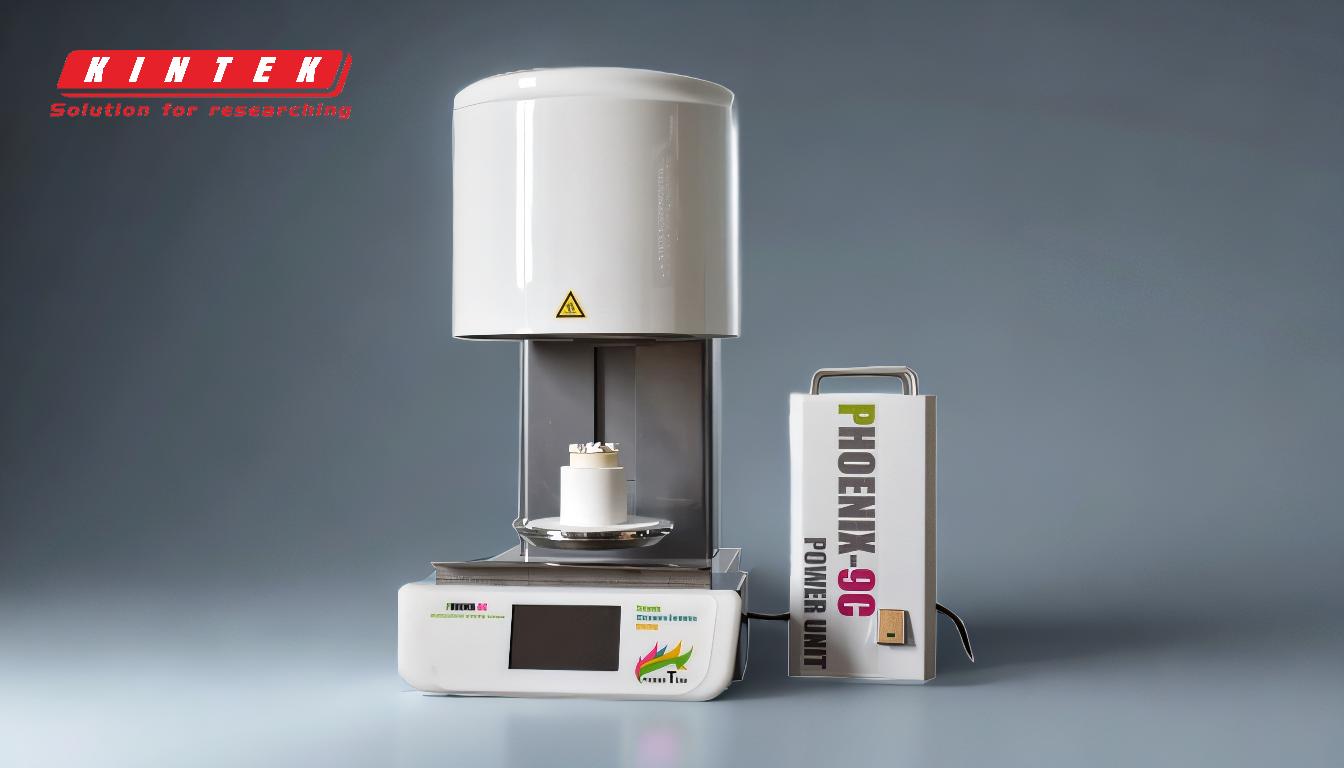
-
Principle of Operation:
- SPS utilizes a high-energy pulsed current to generate electric spark discharge between powder particles, reaching temperatures as high as 10,000°C (18,032°F).
- This rapid heating causes surface contaminants to oxidize or evaporate, while the particle surfaces melt and fuse, forming "necks" that evolve into dense structures.
- The process combines pressure and an electric field to enhance densification, enabling sintering at lower temperatures and shorter times than conventional methods.
-
Mechanism of Densification:
- The pulsed DC current creates localized high temperatures and plasma, which reduce the gaps between particles and promote surface diffusion and boundary defect diffusion.
- The powder particles bond at their interfaces, leading to rapid densification and high solid densities, often exceeding 99%.
-
Advantages of SPS:
- Speed: SPS completes sintering in less than 20 minutes, significantly faster than traditional methods.
- Cost-Effectiveness: The use of low-voltage pulsating currents and short cycle times reduces operational costs.
- Versatility: SPS can sinter both conductive and insulating materials, making it suitable for a wide range of applications.
- Enhanced Properties: The process preserves nanostructures and produces materials with superior magnetic, piezoelectric, thermoelectric, optical, or biomedical properties.
-
Applications:
- SPS is used to prepare advanced materials such as carbon nanotubes for field electron emission electrodes.
- It is ideal for producing high-density composites, nanostructured materials, and components requiring precise control over microstructure and properties.
-
Alternative Names and Clarifications:
- Despite its name, research has shown that plasma is not a significant factor in the process. Alternative names include Field Assisted Sintering Technique (FAST), Electric Field Assisted Sintering (EFAS), and Direct Current Sintering (DCS).
-
Comparison to Conventional Sintering:
- SPS achieves densification at temperatures several hundred degrees lower than conventional sintering.
- It avoids the coarsening of nanostructures, which is a common issue in standard densification routes.
-
Equipment and Process Control:
- SPS requires specialized equipment, including a conductive die (typically graphite) and a power control device capable of generating pulsed DC currents.
- The process allows for precise control over heating and cooling rates, as well as holding times, ensuring optimal densification and material properties.
By combining rapid heating, pressure, and electric fields, Spark Plasma Sintering offers a highly efficient and versatile method for producing advanced materials with exceptional properties. Its ability to densify powders without compromising nanostructures makes it a valuable tool in modern materials science and engineering.
Summary Table:
Aspect | Details |
---|---|
Principle | Uses pulsed DC current for rapid heating, plasma generation, and densification. |
Mechanism | Localized high temperatures reduce particle gaps, promoting bonding. |
Advantages | Faster sintering (<20 mins), cost-effective, versatile, preserves nanostructures. |
Applications | Electronics, biomedical engineering, high-density composites, nanostructured materials. |
Alternative Names | Field Assisted Sintering Technique (FAST), Electric Field Assisted Sintering (EFAS). |
Comparison to Conventional Sintering | Lower temperatures, avoids nanostructure coarsening. |
Equipment | Requires conductive die (e.g., graphite) and pulsed DC power control device. |
Unlock the potential of Spark Plasma Sintering for your materials—contact our experts today!