Surface hardening is a critical process in materials engineering aimed at enhancing the durability and performance of metal components. It involves altering the surface layer of a metal to improve its hardness while maintaining the toughness of the core material. This process is essential in industries where components are subjected to high wear, fatigue, or impact, such as automotive, aerospace, and manufacturing. Surface hardening not only extends the lifespan of parts but also reduces maintenance costs and improves overall efficiency. The techniques used for surface hardening vary depending on the material and application, but they all share the common goal of creating a hard, wear-resistant surface without compromising the structural integrity of the component.
Key Points Explained:
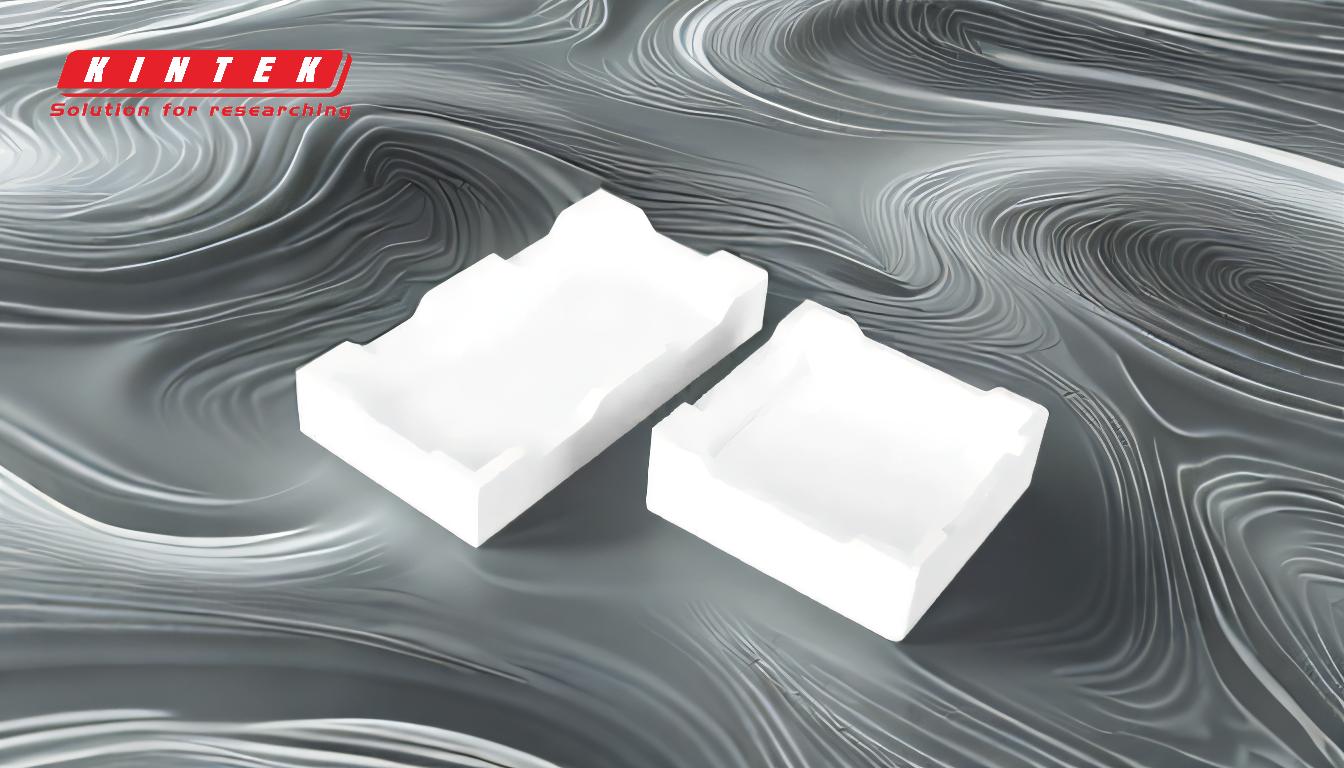
-
Enhanced Wear Resistance:
- Surface hardening significantly increases the hardness of the outer layer of a metal component, making it more resistant to wear and abrasion. This is particularly important for parts that are in constant contact with other surfaces, such as gears, bearings, and cutting tools. By hardening the surface, the component can withstand the mechanical stresses and friction it encounters during operation, thereby reducing the rate of wear and extending its service life.
-
Improved Fatigue Strength:
- Fatigue failure occurs when a material is subjected to repeated cyclic stresses, leading to the formation of cracks and eventual failure. Surface hardening processes, such as case hardening or nitriding, introduce compressive residual stresses on the surface of the material. These stresses counteract the tensile stresses that cause fatigue cracks, thereby improving the fatigue strength of the component. This is crucial for parts that undergo cyclic loading, such as springs, shafts, and structural components.
-
Maintained Core Toughness:
- One of the key advantages of surface hardening is that it allows the core of the material to retain its original toughness and ductility. While the surface becomes hard and wear-resistant, the core remains tough and able to absorb impact energy without fracturing. This combination of a hard surface and a tough core is ideal for components that need to withstand both wear and impact, such as gears, crankshafts, and camshafts.
-
Corrosion Resistance:
- Certain surface hardening techniques, such as nitriding and carburizing, can also improve the corrosion resistance of metal components. These processes create a hardened surface layer that is less susceptible to corrosion, making the component more durable in harsh environments. This is particularly beneficial for parts exposed to corrosive substances, such as those used in chemical processing or marine applications.
-
Cost-Effectiveness:
- Surface hardening is a cost-effective solution for improving the performance of metal components. Instead of using expensive high-alloy materials throughout the entire component, surface hardening allows manufacturers to use less expensive base materials while achieving the desired surface properties. This reduces material costs and makes the production process more economical.
-
Versatility in Applications:
- Surface hardening techniques are versatile and can be applied to a wide range of materials and components. Whether it's a small precision part or a large industrial component, surface hardening can be tailored to meet specific requirements. This versatility makes it a valuable process in various industries, including automotive, aerospace, tool manufacturing, and more.
-
Environmental Benefits:
- By extending the lifespan of components and reducing the need for frequent replacements, surface hardening contributes to environmental sustainability. Fewer replacements mean less material waste and lower energy consumption associated with manufacturing new parts. Additionally, some surface hardening processes, such as induction hardening, are energy-efficient and produce minimal waste, further enhancing their environmental benefits.
In summary, surface hardening is a vital process that enhances the performance, durability, and cost-effectiveness of metal components. By improving wear resistance, fatigue strength, and corrosion resistance while maintaining core toughness, surface hardening ensures that components can withstand the demanding conditions of modern industrial applications. Its versatility and environmental benefits make it an indispensable technique in materials engineering.
Summary Table:
Key Benefit | Description |
---|---|
Enhanced Wear Resistance | Increases surface hardness, reducing wear and extending component lifespan. |
Improved Fatigue Strength | Introduces compressive stresses to prevent fatigue cracks under cyclic loading. |
Maintained Core Toughness | Keeps the core tough and ductile while hardening the surface. |
Corrosion Resistance | Certain techniques improve resistance to corrosion in harsh environments. |
Cost-Effectiveness | Reduces material costs by using less expensive base materials. |
Versatility in Applications | Applicable to a wide range of materials and components across industries. |
Environmental Benefits | Extends component lifespan, reducing waste and energy consumption. |
Optimize your metal components with surface hardening—contact our experts today to learn more!