Physical Vapor Deposition (PVD) is a thin-film deposition technique where a solid material is vaporized in a vacuum environment and then deposited onto a substrate to form a thin film. Unlike Chemical Vapor Deposition (CVD), which relies on chemical reactions between gaseous precursors and the substrate, PVD is a physical process involving the transfer of material from a solid source to the substrate. PVD is widely used in industries such as semiconductors, optics, and tool coatings due to its ability to produce high-quality, durable films at relatively low temperatures. The process is versatile, with variations like sputtering and evaporation, each suited to specific applications.
Key Points Explained:
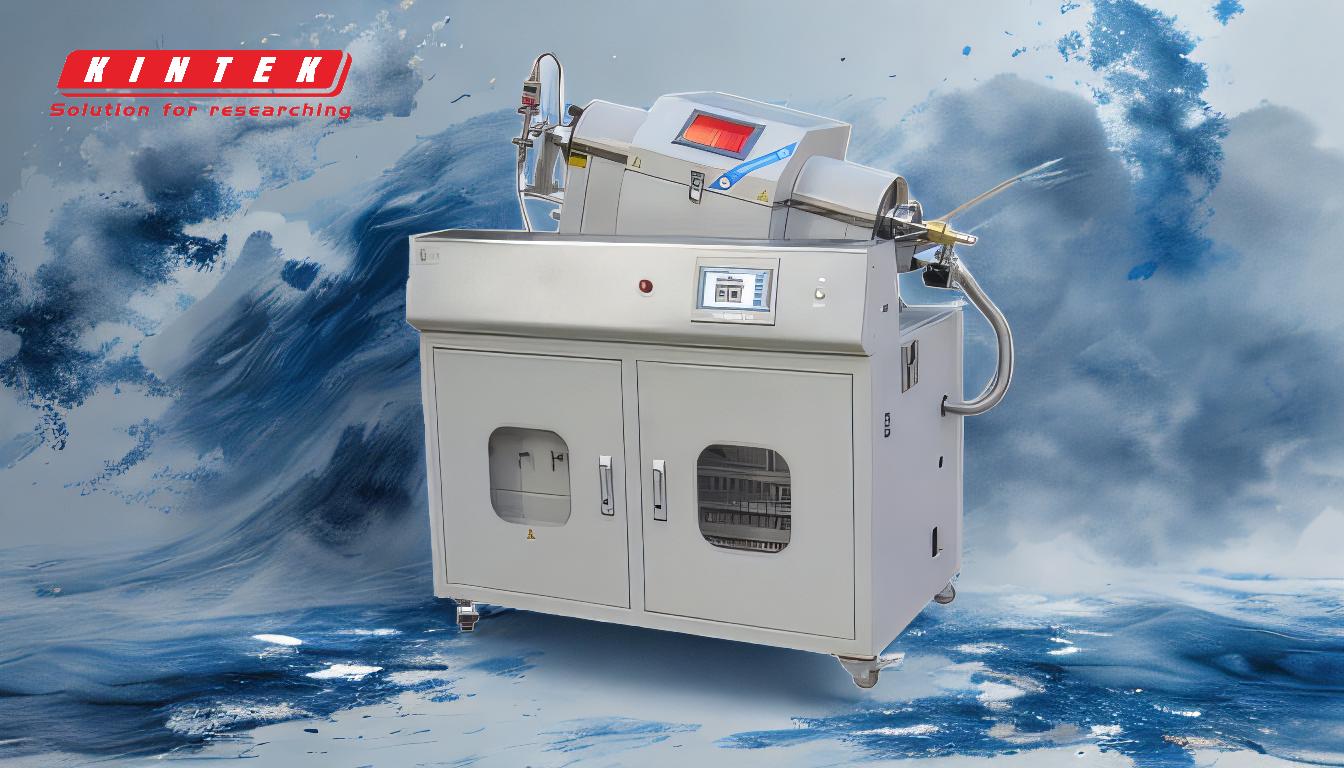
-
Definition of PVD:
- PVD stands for Physical Vapor Deposition, a technique used to deposit thin films onto a substrate by physically vaporizing a solid material in a vacuum environment.
- The process involves three main steps: vaporization of the target material, transportation of the vaporized material through a vacuum, and condensation of the material onto the substrate to form a thin film.
-
Comparison with CVD:
-
Process Differences:
- PVD uses solid materials that are vaporized and deposited onto the substrate, while CVD uses gaseous precursors that chemically react with the substrate to form a film.
- PVD is a line-of-sight process, meaning the material is deposited directly onto the substrate without chemical interaction, whereas CVD involves multidirectional deposition with chemical reactions.
-
Temperature Differences:
- PVD typically operates at lower temperatures (250°C~450°C), making it suitable for temperature-sensitive substrates.
- CVD requires higher temperatures (450°C to 1050°C), which can lead to the formation of corrosive by-products and impurities in the film.
-
Process Differences:
-
Advantages of PVD:
- Lower Deposition Temperatures: PVD can be performed at lower temperatures, reducing the risk of damaging temperature-sensitive substrates.
- No Corrosive By-products: Unlike CVD, PVD does not produce corrosive gaseous products, resulting in cleaner films.
- High Material Utilization Efficiency: Techniques like Electron Beam PVD (EBPVD) offer high deposition rates (0.1 to 100 μm/min) with excellent material utilization.
-
Applications of PVD:
- Semiconductors: PVD is used to deposit metal layers and dielectric films in semiconductor manufacturing.
- Optics: It is employed to create reflective and anti-reflective coatings on optical components.
- Tool Coatings: PVD is widely used to apply hard, wear-resistant coatings on cutting tools and machine parts.
-
Variations of PVD:
- Sputtering: A common PVD technique where ions bombard a target material, causing atoms to be ejected and deposited onto the substrate.
- Evaporation: Another PVD method where the target material is heated until it evaporates, and the vapor condenses on the substrate.
- Microwave Plasma Chemical Vapor Deposition: While not a PVD technique, it is worth noting that microwave plasma chemical vapor deposition is a related method that uses plasma to enhance chemical reactions for film deposition.
-
Limitations of PVD:
- Lower Deposition Rates: Compared to CVD, PVD generally has lower deposition rates, which can be a limitation for high-throughput applications.
- Line-of-Sight Limitation: Since PVD is a line-of-sight process, it may not be suitable for coating complex geometries or internal surfaces.
In summary, PVD is a versatile and widely used thin-film deposition technique that offers several advantages over CVD, particularly in terms of lower deposition temperatures and cleaner film formation. Its applications span various industries, and it continues to be a critical technology in modern manufacturing and materials science.
Summary Table:
Aspect | Details |
---|---|
Definition | PVD is a thin-film deposition technique using solid material vaporization. |
Process Steps | Vaporization, transportation in vacuum, condensation on substrate. |
Comparison with CVD | Lower temperatures, no corrosive by-products, line-of-sight deposition. |
Advantages | Cleaner films, high material efficiency, suitable for sensitive substrates. |
Applications | Semiconductors, optics, tool coatings. |
Variations | Sputtering, evaporation. |
Limitations | Lower deposition rates, line-of-sight limitation. |
Interested in PVD technology? Contact us today to learn how it can benefit your applications!