The refractory materials used in muffle furnaces are critical for ensuring high-temperature resistance, durability, and effective heat transfer. The primary materials include alumina (Al₂O₃) for its excellent high-temperature and corrosion resistance, silicon carbide (SiC) for its strength and thermal conductivity, and zirconia board for extreme temperatures up to 1600°C. Additionally, quartz glass is used in some designs for its transparency, allowing observation of processes. The choice of material depends on the operating temperature, chemical environment, and specific application requirements.
Key Points Explained:
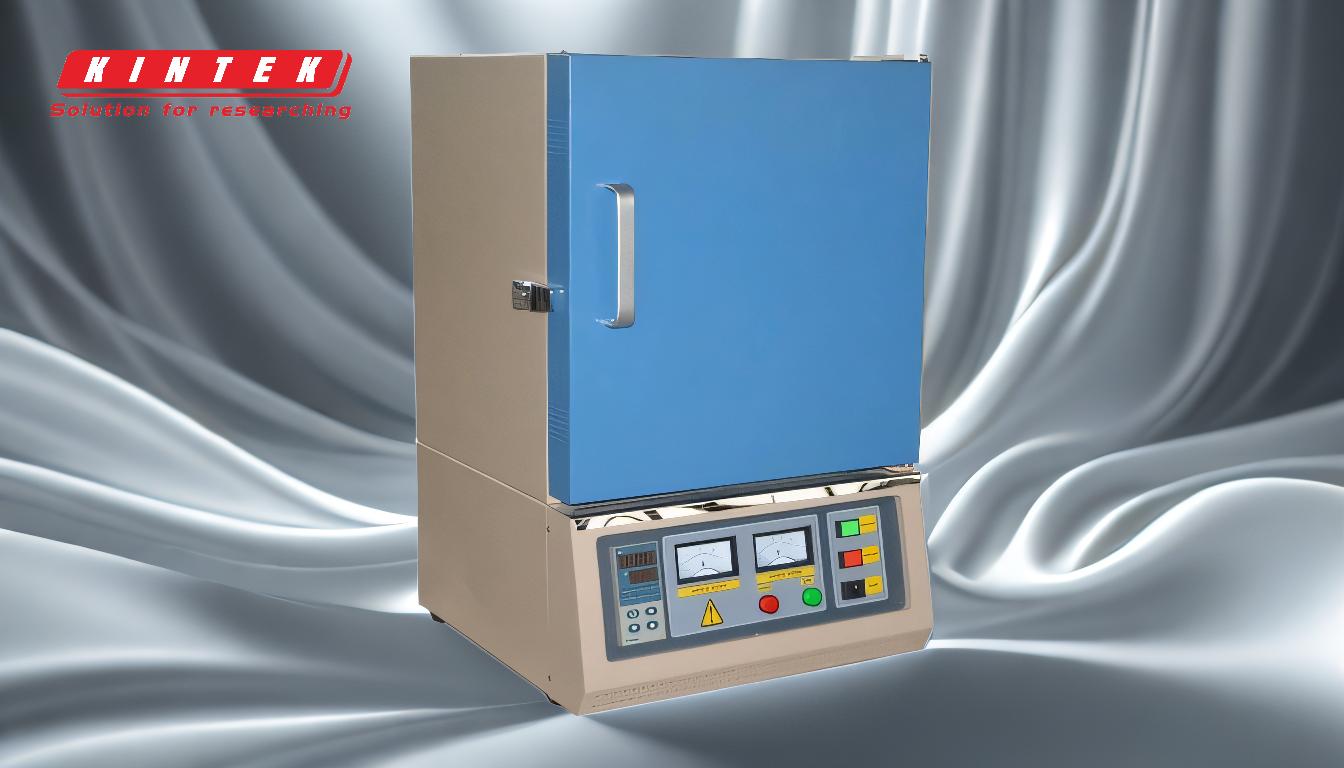
-
Primary Refractory Materials:
-
Alumina (Al₂O₃):
- Alumina is the most commonly used refractory material in muffle furnaces due to its exceptional high-temperature resistance (up to 1800°C) and resistance to chemical corrosion. It is used in the form of ceramic tiles, bricks, or linings.
- It ensures uniform heat distribution and durability, making it suitable for a wide range of high-temperature applications.
-
Silicon Carbide (SiC):
- Silicon carbide is another key material, known for its high strength, thermal conductivity, and resistance to thermal shock. It is often used in insulating firebricks.
- SiC is ideal for applications requiring rapid heating and cooling cycles, as it maintains structural integrity under extreme conditions.
-
Zirconia Board:
- Zirconia is used in high-temperature muffle furnaces (up to 1600°C) due to its superior thermal stability and resistance to wear. It is often employed in specialized applications requiring extreme heat.
-
Alumina (Al₂O₃):
-
Material Selection Based on Temperature:
- Ceramic Tiles: Suitable for temperatures up to 1200°C, ceramic tiles are cost-effective and provide good insulation.
- Zirconia Board: Used for temperatures up to 1600°C, zirconia offers higher thermal stability than alumina.
- High Alumina Bricks: Capable of withstanding temperatures up to 1800°C, these bricks are ideal for ultra-high-temperature applications.
-
Additional Materials for Specific Applications:
- Quartz Glass: Used in high-temperature muffle furnaces where transparency is required for observing the experimental process. Quartz glass can withstand high temperatures but is more fragile compared to ceramic materials.
- Heat-Resisting Stainless Steel or Inconel: In some cases, muffles are made from these metals, depending on customer requirements. These materials are used when chemical resistance and mechanical strength are prioritized over thermal insulation.
-
Structural Components:
- Outer Body: The outer body of a muffle furnace is typically made of thick mild steel, powder-coated for durability. In some cases, stainless steel (SS 304/316) is used for applications requiring higher corrosion resistance or compliance with GMP standards.
- Inner Chamber: The inner chamber, or heating zone, is constructed using refractory materials like ceramic tiles, zirconia board, or high alumina bricks, depending on the temperature requirements.
-
Importance of Refractory Linings:
- Refractory linings, made of alumina or silicon carbide, ensure accurate and uniform process conditions by providing thermal insulation and preventing heat loss.
- These linings also protect the furnace structure from thermal stress and chemical reactions, extending the lifespan of the furnace.
-
Factors Influencing Material Choice:
- Operating Temperature: The maximum temperature of the furnace determines the type of refractory material used.
- Chemical Environment: Materials must resist corrosion from gases, liquids, or solids present in the furnace.
- Thermal Conductivity: Depending on the application, materials with high or low thermal conductivity may be preferred.
- Mechanical Strength: Materials must withstand mechanical stress during heating and cooling cycles.
By understanding these key points, purchasers can make informed decisions about the refractory materials for muffle furnaces, ensuring optimal performance and longevity for their specific applications.
Summary Table:
Material | Key Properties | Temperature Range | Applications |
---|---|---|---|
Alumina (Al₂O₃) | High-temperature resistance, corrosion resistance, uniform heat distribution | Up to 1800°C | Ceramic tiles, bricks, linings for general high-temperature applications |
Silicon Carbide (SiC) | High strength, thermal conductivity, resistance to thermal shock | Up to 1600°C | Insulating firebricks for rapid heating/cooling cycles |
Zirconia Board | Superior thermal stability, wear resistance | Up to 1600°C | Specialized applications requiring extreme heat |
Quartz Glass | Transparency, high-temperature resistance | Up to 1200°C | Experimental observation in high-temperature processes |
High Alumina Bricks | Ultra-high-temperature resistance | Up to 1800°C | Ultra-high-temperature applications |
Need help selecting the right refractory materials for your muffle furnace? Contact our experts today for tailored solutions!