Brazing is a highly relevant and widely used process in various industries due to its cost-effectiveness, versatility, and ability to join dissimilar materials. It is particularly advantageous for automated and mass production, offering faster lead times and consistent results. Brazing is applied in critical industries such as aerospace, medical devices, heating and cooling systems, and advanced research, where precision and reliability are paramount. Its ability to create strong, leak-proof joints in complex assemblies makes it indispensable for manufacturing components like heat exchangers, sensors, and structural parts. Additionally, specialized techniques like hydrogen brazing are used in high-tech applications, including medical and research equipment, further underscoring its industrial significance.
Key Points Explained:
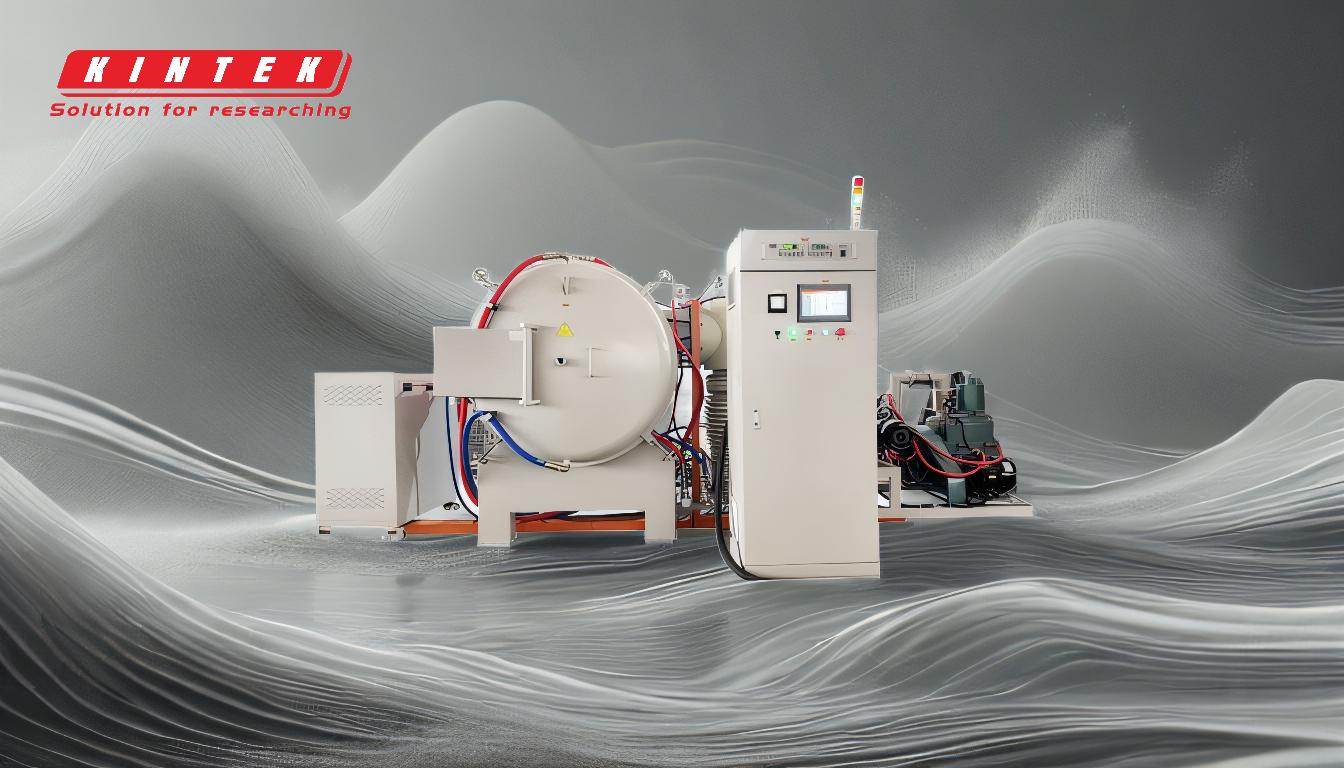
-
Cost-Effectiveness and Efficiency in Production
- Brazing, particularly furnace brazing, is cost-effective due to its lower operator skill requirements and faster production cycles.
- It ensures consistent results from batch to batch, making it ideal for automated and mass production environments.
- This efficiency reduces manufacturing costs and improves scalability, which is crucial for industries requiring high-volume production.
-
Versatility in Applications
- Brazing is used across a wide range of industries, including heating and cooling systems, aerospace, medical devices, and structural components.
- It is particularly effective for joining dissimilar materials, such as metals and ceramics, which are often required in advanced applications.
- Examples include micro-channel heat exchangers, aircraft components, and sensors, where precision and durability are critical.
-
Specialized Techniques for Advanced Applications
- Hydrogen brazing is a specialized form of brazing used in high-tech industries, such as medical, research, and security fields.
- It is employed in the production of X-ray tubes, traveling wave tubes, and linear gas pedals, where the bonding of metals and ceramics is essential.
- This technique ensures high-quality, leak-proof joints in components used in ion or electron beam devices, highlighting its importance in cutting-edge technology.
-
Strong and Reliable Joints
- Brazing creates strong, durable, and leak-proof joints, which are essential for components exposed to high temperatures, pressures, or corrosive environments.
- This reliability is critical in industries like aerospace and medical devices, where failure is not an option.
- The process also allows for the joining of complex geometries, enabling the production of intricate and high-performance assemblies.
-
Role in Automation and Mass Production
- The consistency and repeatability of brazing make it a preferred method for automated production lines.
- It reduces the need for manual intervention, minimizing human error and increasing throughput.
- This capability is particularly valuable in industries like automotive and electronics, where high-volume production is the norm.
-
Environmental and Safety Considerations
- Brazing is often performed in controlled environments, such as furnaces, which reduce exposure to harmful fumes and ensure operator safety.
- The use of hydrogen brazing, for example, requires strict safety protocols but offers clean and precise bonding without the need for flux, reducing environmental impact.
In summary, brazing is a cornerstone of modern manufacturing, offering a unique combination of cost-effectiveness, versatility, and reliability. Its applications span from everyday industrial components to advanced medical and research equipment, making it an indispensable process across multiple sectors.
Summary Table:
Key Aspect | Details |
---|---|
Cost-Effectiveness | Lower operator skill requirements, faster production cycles, consistent results. |
Versatility | Joins dissimilar materials (metals, ceramics), used in aerospace, medical, and more. |
Specialized Techniques | Hydrogen brazing for high-tech applications like X-ray tubes and research equipment. |
Strong Joints | Creates durable, leak-proof joints for high-temperature and high-pressure environments. |
Automation & Mass Production | Ideal for automated production, reducing human error and increasing throughput. |
Environmental Safety | Controlled environments minimize harmful fumes, hydrogen brazing reduces flux use. |
Discover how brazing can enhance your manufacturing process—contact our experts today!