The remelting process involves melting a material, typically a metal, to either fuse it with another material or to reform it to alter its physical properties. This process is widely used in manufacturing to achieve desired characteristics such as improved strength, ductility, or corrosion resistance. By remelting, manufacturers can refine the microstructure of the material, remove impurities, and enhance its overall performance. Below is a detailed explanation of the key aspects of the remelting process.
Key Points Explained:
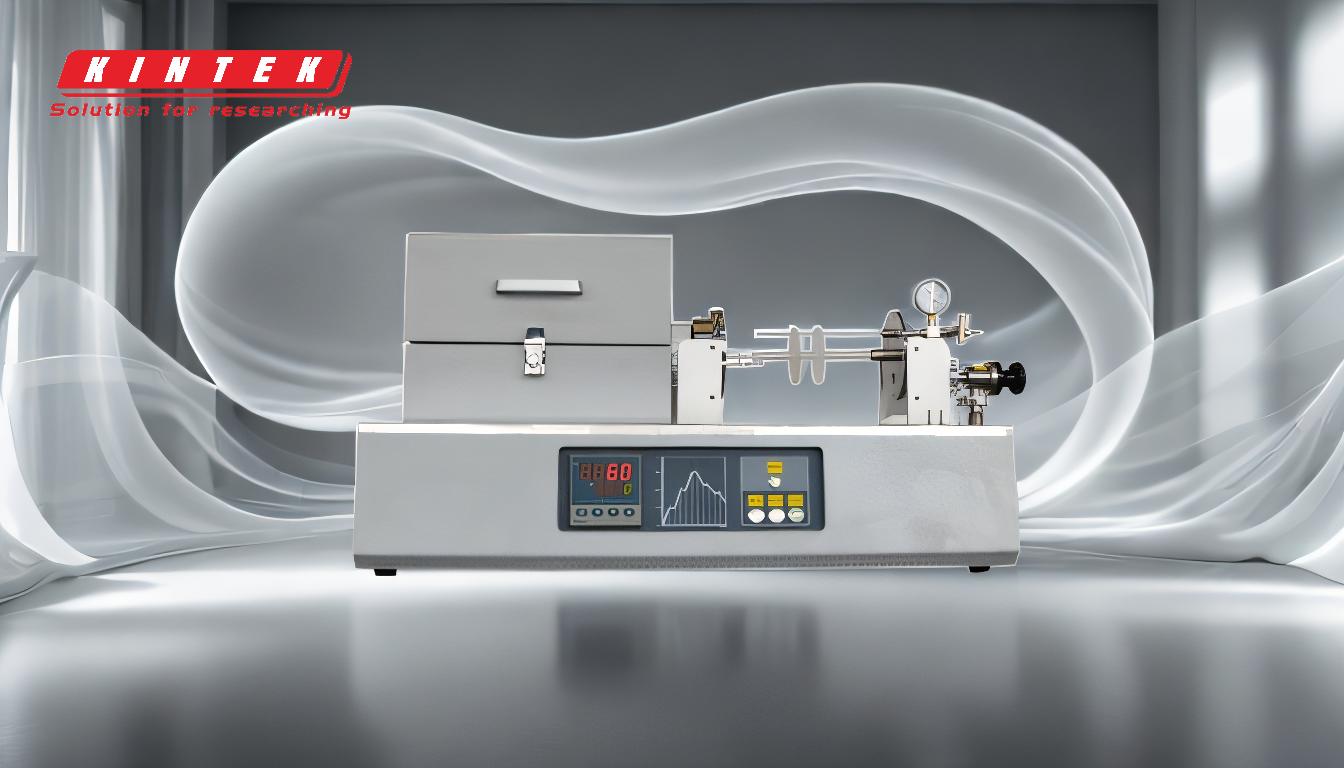
-
Definition and Purpose of Remelting:
- Remelting is the process of melting a material, often a metal, to either combine it with another material or to reform it. This is done to achieve specific physical or mechanical properties.
- The primary purposes of remelting include:
- Fusing two objects together (e.g., welding or brazing).
- Altering the material's properties, such as improving strength, ductility, or corrosion resistance.
- Refining the material's microstructure to remove impurities or defects.
-
Applications in Manufacturing:
- Fusing Objects: Remelting is commonly used in processes like welding, soldering, and brazing, where two materials are joined by melting a filler material or the base materials themselves.
- Reforming Metals: Remelting is used to reshape metals into new forms, such as casting ingots or creating alloys with specific properties.
- Property Enhancement: By remelting, manufacturers can refine the grain structure of metals, which improves their mechanical properties and performance in demanding applications.
-
Benefits of Remelting:
- Improved Material Properties: Remelting can enhance the strength, ductility, and corrosion resistance of metals by refining their microstructure.
- Impurity Removal: The process allows for the removal of impurities and inclusions, resulting in a cleaner and more uniform material.
- Versatility: Remelting can be applied to a wide range of materials and processes, making it a versatile technique in manufacturing.
-
Key Steps in the Remelting Process:
- Heating: The material is heated to its melting point using a heat source such as a furnace, arc, or laser.
- Melting: The material transitions from a solid to a liquid state, allowing it to be reshaped or combined with other materials.
- Refining: During the liquid phase, impurities can be removed, and the material's microstructure can be adjusted.
- Solidification: The molten material is cooled and solidified into the desired shape or form.
-
Types of Remelting Processes:
- Vacuum Arc Remelting (VAR): Used for high-purity metals and alloys, particularly in aerospace and medical industries.
- Electroslag Remelting (ESR): A process that refines the metal by passing an electric current through a molten slag layer.
- Induction Melting: Uses electromagnetic induction to heat and melt metals, commonly used in foundries.
- Casting and Recasting: Involves melting and reshaping metals into new forms, such as ingots or components.
-
Considerations for Equipment and Consumables Purchasers:
- Material Compatibility: Ensure the remelting equipment is suitable for the specific materials being processed.
- Energy Efficiency: Choose energy-efficient systems to reduce operational costs.
- Quality Control: Invest in systems that allow for precise temperature control and impurity removal to ensure high-quality output.
- Scalability: Consider the throughput and scalability of the remelting process to meet production demands.
By understanding the remelting process and its applications, manufacturers can make informed decisions about equipment and consumables to achieve optimal results in their operations.
Summary Table:
Aspect | Key Details |
---|---|
Definition | Melting a material to fuse or reform it, altering physical/mechanical properties. |
Applications | Welding, brazing, reshaping metals, and enhancing material properties. |
Benefits | Improved strength, ductility, corrosion resistance, and impurity removal. |
Key Steps | Heating, melting, refining, and solidification. |
Types of Processes | Vacuum Arc Remelting (VAR), Electroslag Remelting (ESR), Induction Melting, etc. |
Purchasing Considerations | Material compatibility, energy efficiency, quality control, and scalability. |
Optimize your manufacturing process with advanced remelting techniques—contact us today for expert guidance!