The sintering process is a critical method in materials science and manufacturing, used to create solid, durable products from powdered materials through controlled heating and cooling. It involves several stages, including preparation of raw materials, compaction, heating to facilitate particle bonding, and cooling to solidify the final product. This process ensures the formation of a low-porosity, cohesive structure with enhanced mechanical properties. Below, the key steps and phases of sintering are explained in detail, focusing on the chemical reactions and physical transformations that occur during each stage.
Key Points Explained:
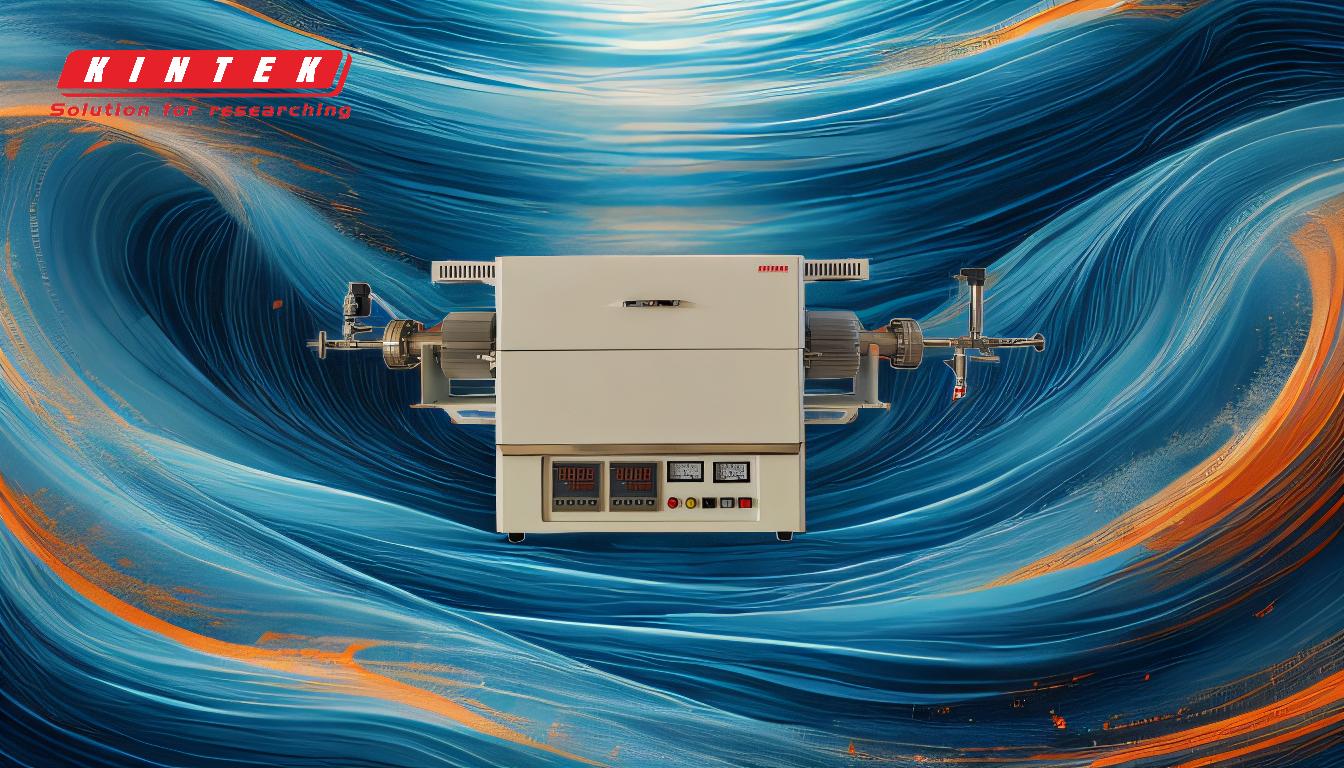
-
Preparation of Raw Materials
- The sintering process begins with the preparation of raw materials, typically in powdered form.
- These powders are mixed with additives such as coupling agents, binders, or deflocculants to improve uniformity and facilitate bonding.
- The mixture is often spray-dried to create a slurry, which is then shaped into the desired form.
- Chemical Reactions: During this stage, no significant chemical reactions occur, but the uniformity of the mixture is critical for ensuring consistent sintering later.
-
Compaction (Powder Compacting)
- The mixed powder is compacted using mechanical pressure, such as cold or hot mold pressing, to form a "green part."
- Compaction eliminates voids and ensures the material has a uniform density, which is essential for achieving a strong final product.
- Chemical Reactions: At this stage, the particles may form cold welds, but no major chemical changes occur.
-
Heating (Sintering or Firing)
- The green part is heated in a controlled environment, typically in a sintering furnace or kiln, to a temperature just below the melting point of the material.
- During heating, particles undergo diffusion, leading to neck formation and densification. This is where the primary chemical reactions and physical transformations occur.
- Neck Formation: Particles bond at their contact points, forming necks that grow as atoms diffuse across the particle surfaces.
- Densification: Voids between particles shrink, and the material becomes denser and stronger.
- Liquid Phase Sintering (LPS): In some cases, a liquid phase may form to accelerate particle merging and densification.
- Chemical Reactions: Depending on the material, oxidation, reduction, or phase transformations may occur. For example, in ceramic sintering, the binder may decompose, and the ceramic particles may fuse.
-
Cooling and Solidification
- After sintering, the material is cooled gradually to allow it to solidify into a rigid, cohesive structure.
- Controlled cooling prevents thermal stresses and ensures the material retains its desired properties.
- Chemical Reactions: No significant chemical reactions occur during cooling, but the microstructure of the material stabilizes.
-
Post-Sintering Treatment
- In some cases, additional treatments such as machining, polishing, or coating may be applied to achieve the final product specifications.
- Chemical Reactions: Post-sintering treatments are primarily mechanical or surface-level and do not involve significant chemical changes.
Importance of Controlled Parameters:
- Temperature: Precise control of temperature is crucial to ensure proper particle bonding without causing complete melting.
- Atmosphere: The sintering environment (e.g., vacuum, inert gas, or reducing atmosphere) can influence the chemical reactions and final properties of the material.
- Time: The duration of heating and cooling affects the extent of densification and microstructure development.
Applications of Sintering:
- Metals: Used to produce components with high strength and wear resistance, such as gears and bearings.
- Ceramics: Used to create durable, heat-resistant products like tiles and insulators.
- Composites: Sintering is employed to combine different materials, such as metals and ceramics, to achieve unique properties.
By understanding the sintering process and its stages, manufacturers can optimize the production of high-quality materials with tailored properties for specific applications.
Summary Table:
Stage | Key Actions | Chemical Reactions |
---|---|---|
Preparation of Raw Materials | Mixing powders with additives, spray-drying to form slurry, shaping. | No significant reactions; uniformity is critical. |
Compaction | Cold or hot mold pressing to form a "green part." | Cold welds may form; no major chemical changes. |
Heating (Sintering) | Heating to just below melting point; neck formation, densification, LPS. | Oxidation, reduction, or phase transformations (e.g., binder decomposition, particle fusion). |
Cooling | Gradual cooling to solidify the material. | No significant reactions; microstructure stabilizes. |
Post-Sintering Treatment | Machining, polishing, or coating for final specifications. | Primarily mechanical or surface-level; no significant chemical changes. |
Optimize your sintering process for high-quality materials—contact our experts today!