Plasma-enhanced chemical vapor deposition (PECVD) is a process widely used in the semiconductor and thin-film industries due to its ability to deposit films at relatively low temperatures while maintaining a high deposition rate. The speed of PECVD, or its deposition rate, is influenced by various factors, including the operating parameters of the equipment, the type of material being deposited, and the specific application requirements. PECVD is favored for its ability to produce films with good electrical properties, adhesion, and step coverage, although the quality of PECVD films may not match that of low-pressure chemical vapor deposition (LPCVD) films. The deposition rate of PECVD is generally higher than that of LPCVD, making it suitable for applications requiring faster processing times.
Key Points Explained:
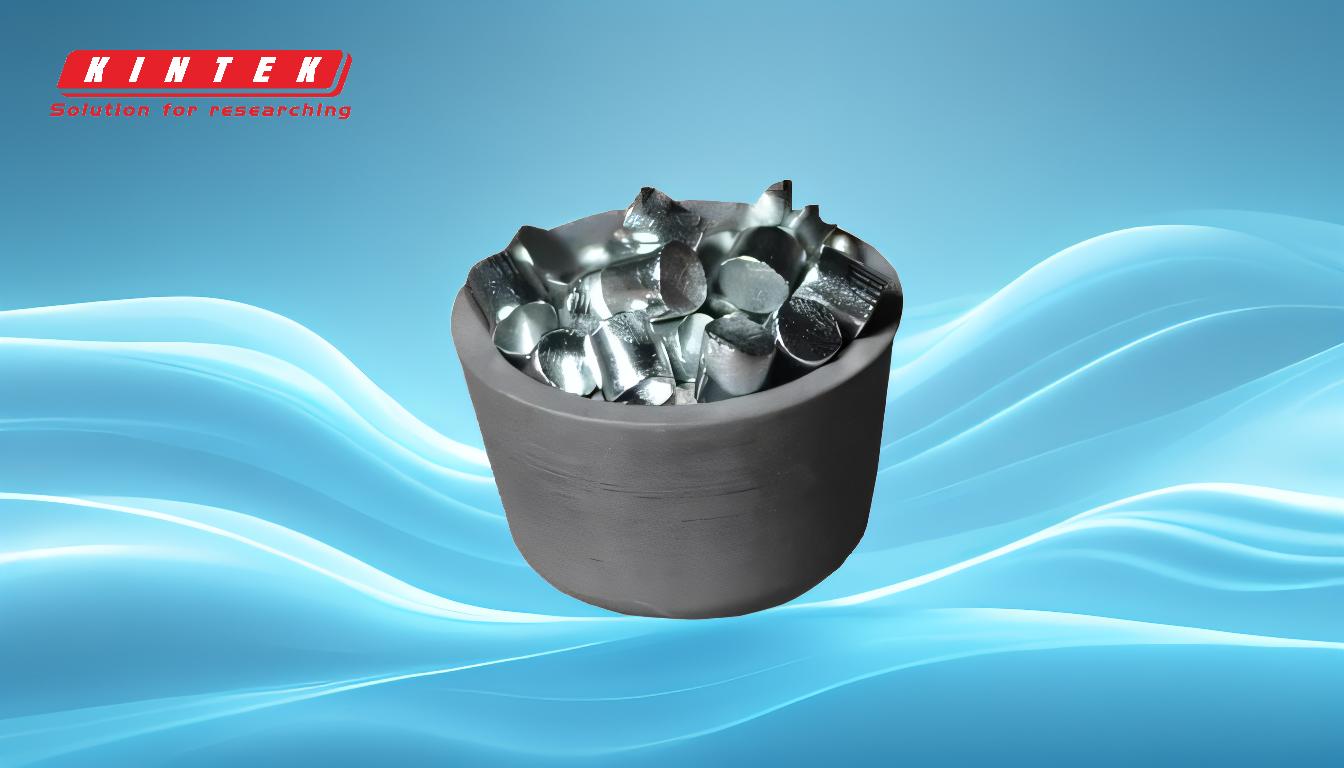
-
Deposition Rate of PECVD:
- PECVD is known for its relatively high deposition rate compared to other CVD techniques, such as LPCVD. This is primarily due to the use of plasma, which enhances the chemical reactions in the gas phase, allowing for faster film formation.
- The deposition rate of PECVD can vary depending on the specific material being deposited and the operating conditions, but it is generally in the range of tens to hundreds of nanometers per minute.
-
Factors Influencing Deposition Speed:
- RF Power and Frequency: The power and frequency of the radio frequency (RF) power supply play a significant role in determining the deposition rate. Higher RF power can increase the energy of the plasma, leading to faster deposition. The frequency of the RF power supply also affects the ion bombardment and film density, which can influence the deposition rate.
- Plate Spacing and Chamber Dimensions: The spacing between the plates in the reaction chamber and the overall dimensions of the chamber can affect the uniformity and speed of deposition. Optimal plate spacing ensures efficient plasma generation and uniform film deposition.
- Gas Pressure and Flow Rate: The pressure within the reaction chamber and the flow rate of the precursor gases are critical factors. Higher gas pressure and flow rates can increase the deposition rate, but they must be carefully controlled to avoid compromising film quality.
- Substrate Temperature: Although PECVD operates at lower temperatures compared to other CVD methods, the substrate temperature still plays a role in determining the deposition rate. Higher substrate temperatures can enhance the reaction kinetics, leading to faster deposition.
-
Trade-offs Between Speed and Film Quality:
- While PECVD offers higher deposition rates, there is often a trade-off between speed and film quality. PECVD films may have higher hydrogen content, pinholes, and lower density compared to LPCVD films, especially for thinner films (<4000Å).
- The deposition rate can be optimized to balance speed and quality, depending on the specific application requirements. For example, in applications where high throughput is more critical than film quality, higher deposition rates may be preferred.
-
Applications and Implications of High Deposition Rates:
- The high deposition rate of PECVD makes it particularly suitable for applications requiring rapid processing, such as the coating of electronic components before fabrication or repair.
- PECVD's ability to deposit films at low temperatures reduces thermal damage and interdiffusion between the film and substrate, making it ideal for temperature-sensitive materials and devices.
-
Comparison with Other CVD Techniques:
- Compared to LPCVD, PECVD offers faster deposition rates but may result in films with lower quality. LPCVD, on the other hand, provides higher-quality films but at slower deposition rates.
- The choice between PECVD and other CVD techniques depends on the specific requirements of the application, including the desired film properties, processing time, and substrate compatibility.
In summary, the speed of PECVD is influenced by a combination of factors, including RF power, plate spacing, gas pressure, and substrate temperature. While PECVD offers relatively high deposition rates, it is important to balance speed with film quality to meet the specific needs of the application. The ability to deposit films quickly at low temperatures makes PECVD a valuable technique in the semiconductor and thin-film industries.
Summary Table:
Aspect | Details |
---|---|
Deposition Rate | Tens to hundreds of nanometers per minute |
Key Influencing Factors | RF power, plate spacing, gas pressure, substrate temperature |
Advantages | High speed, low-temperature processing, good electrical properties |
Trade-offs | Higher hydrogen content, pinholes, lower density compared to LPCVD |
Applications | Coating electronic components, temperature-sensitive materials |
Optimize your semiconductor processes with PECVD—contact our experts today for tailored solutions!