A rotary hearth furnace is a specialized industrial furnace designed for high-temperature heat treatment processes. Its structure is engineered to ensure efficient heating, rotation, and material handling. The furnace consists of a circular hearth or platform that rotates on wheels or rollers, made of refractory materials to withstand extreme temperatures. The furnace chamber is enclosed and heated using burners or other heat sources. Key components include the furnace body, refractory lining, drive mechanism, charging and tapping ports, and exhaust systems. The furnace is typically inclined to facilitate material movement and mixing during rotation. Below, the structure and its components are explained in detail.
Key Points Explained:
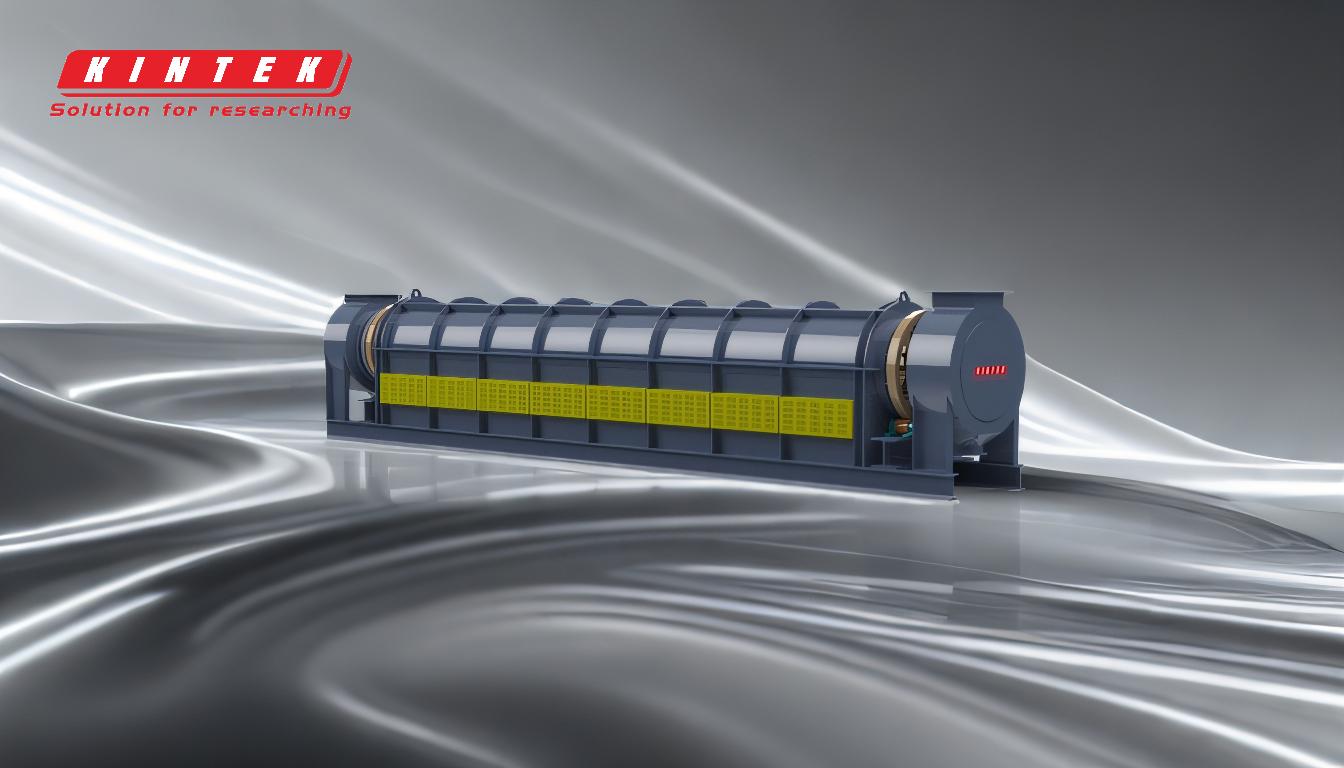
-
Hearth or Rotating Platform:
- The hearth is the circular platform that rotates within the furnace. It is typically made of refractory materials to withstand high temperatures and thermal stress.
- The rotation is facilitated by a set of wheels or rollers, ensuring smooth and consistent movement of materials placed on the hearth.
- The hearth's design allows for continuous processing of materials, making it ideal for applications like metal reduction, heat treatment, and waste processing.
-
Furnace Body and Shell:
- The furnace body is a long, barrel-shaped steel cylinder lined with refractory materials. This steel shell provides structural integrity and supports the internal components.
- The refractory lining insulates the steel body, protecting it from high temperatures and corrosion, while also improving energy efficiency by retaining heat.
-
Drive Mechanism:
- The furnace is driven by an electric motor connected to a gear system. This mechanism ensures slow and controlled rotation of the hearth.
- The drive system is mounted on a fabricated chassis, which supports the entire furnace structure and ensures stability during operation.
-
Inclination and Rotation:
- The furnace body is slightly inclined (typically 3% to 6%) to allow materials to move from the charging end to the tapping end as the hearth rotates.
- This inclination, combined with rotation, facilitates mixing or stirring of materials, ensuring uniform heat treatment.
-
Charging and Tapping Ports:
- The furnace has a charging door for loading materials and two tapping ports for emptying processed materials.
- These ports are strategically placed to optimize material flow and minimize heat loss during loading and unloading.
-
Heat Source and Burners:
- The furnace is heated using burners or other heat sources, which can be automatic or manual. These burners are typically located near the charging door.
- The heat source can be gas or electric, utilizing conduction, convection, or radiation to achieve the required furnace temperature.
-
Exhaust System:
- An exhaust door is provided to carry flue gases out of the furnace chamber for further processing or emission control.
- This system ensures proper ventilation and maintains the furnace's internal environment for efficient operation.
-
Supporting Wheels and Rollers:
- The furnace body is supported on several pairs of supporting wheels or rollers, which enable smooth rotation and reduce friction.
- These components are critical for maintaining the furnace's structural integrity and operational efficiency.
-
Integrated Control Systems:
- Modern rotary hearth furnaces often include integrated control systems for temperature regulation, feeder control, and temperature measurement.
- These systems ensure precise control over the heating process, improving consistency and quality of the heat-treated materials.
-
Applications and Customization:
- The structure of a rotary hearth furnace can vary depending on the application. For example, the length of the furnace body and the type of refractory materials used may be customized to suit specific industrial needs.
- Common applications include metal reduction, waste processing, and heat treatment of materials like steel and ceramics.
In summary, the structure of a rotary hearth furnace is a sophisticated combination of mechanical and thermal engineering. Its key components—such as the rotating hearth, refractory lining, drive mechanism, and heat source—are designed to work together seamlessly, ensuring efficient and reliable operation for high-temperature industrial processes. The furnace's ability to rotate and incline, combined with precise control systems, makes it a versatile and essential tool in various industries.
Summary Table:
Component | Description |
---|---|
Hearth/Rotating Platform | Circular platform made of refractory materials, rotates on wheels/rollers. |
Furnace Body & Shell | Barrel-shaped steel cylinder lined with refractory materials for insulation. |
Drive Mechanism | Electric motor and gear system for controlled rotation. |
Inclination & Rotation | Slight incline (3%-6%) for material movement and mixing. |
Charging & Tapping Ports | Ports for loading/unloading materials, minimizing heat loss. |
Heat Source & Burners | Gas or electric burners for heating, located near the charging door. |
Exhaust System | Removes flue gases for ventilation and emission control. |
Supporting Wheels/Rollers | Enable smooth rotation and reduce friction. |
Control Systems | Integrated systems for temperature regulation and process control. |
Applications | Metal reduction, waste processing, heat treatment of steel, ceramics, and more. |
Discover how a rotary hearth furnace can optimize your industrial processes—contact us today for expert advice!