The substrate temperature in sputtering plays a critical role in determining the quality and properties of the deposited thin films. It influences factors such as film density, adhesion, crystallinity, stress, and defect density. Higher substrate temperatures generally lead to denser films with improved surface reactions and reduced defect density, while lower temperatures may be necessary for certain materials or applications to control stress and adhesion. The temperature can be optimized to achieve desired film characteristics, and cooling steps may be required in some cases to manage thermal effects. Understanding the relationship between substrate temperature and film properties is essential for optimizing sputtering processes.
Key Points Explained:
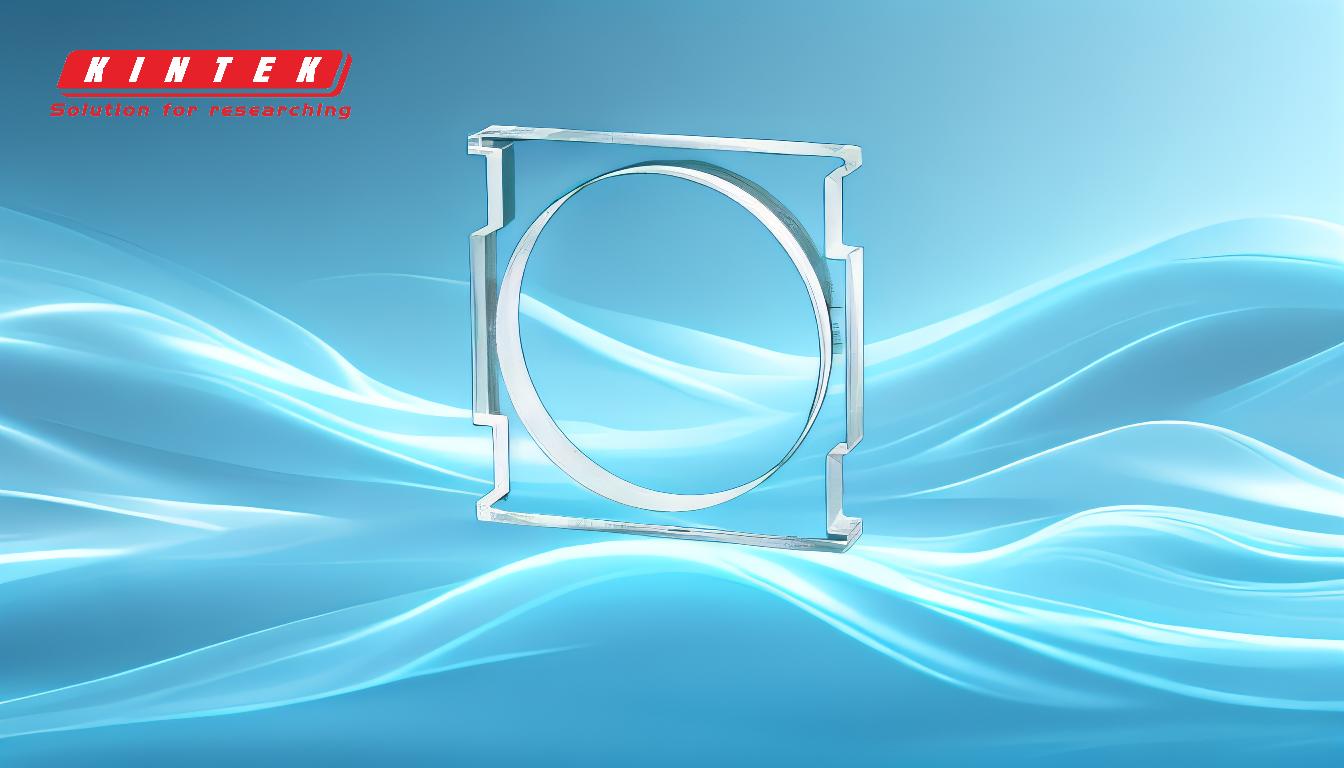
-
Impact on Film Quality:
- Substrate temperature significantly affects the quality of thin films deposited during sputtering.
- Higher temperatures enhance surface reactions, leading to denser films with improved composition.
- Increased temperature helps compensate for dangling bonds on the film surface, reducing defect density and improving local state density, electron mobility, and optical properties.
-
Influence on Deposition Rate:
- Substrate temperature has minimal impact on the deposition rate.
- The primary effect of temperature is on the quality and properties of the film rather than the speed of deposition.
-
Adhesion, Crystallinity, and Stress:
- Temperature affects the adhesion of the film to the substrate, with optimal temperatures improving bonding.
- Crystallinity of the film can be controlled by adjusting the substrate temperature, as higher temperatures promote better crystalline structures.
- Stress in the film is influenced by temperature, as described by the formula:
[ \sigma = E \times \alpha \times (T - T_0) ]
where (\sigma) is the stress, (E) is the Young's modulus, (\alpha) is the coefficient of thermal expansion, (T) is the substrate temperature, and (T_0) is the reference temperature.
-
Optimization of Temperature:
- The substrate temperature can be optimized to achieve specific film properties, such as desired density, adhesion, and stress levels.
- In some cases, heating the substrate to a specific temperature is necessary to enhance film quality.
- Cooling steps may also be required to manage thermal effects and prevent damage to sensitive materials.
-
Material-Specific Considerations:
- Different materials may require different substrate temperatures to achieve optimal film properties.
- For example, materials with high thermal expansion coefficients may need careful temperature control to minimize stress and prevent delamination.
-
Practical Implications for Equipment and Consumables:
- For equipment purchasers, understanding the relationship between substrate temperature and film properties is crucial for selecting the right sputtering system.
- Systems with precise temperature control and cooling capabilities may be necessary for advanced applications.
- Consumables, such as substrates and target materials, should be chosen with consideration of their thermal properties and compatibility with the desired temperature range.
By carefully controlling and optimizing the substrate temperature, sputtering processes can be tailored to produce high-quality thin films with the desired properties for various applications.
Summary Table:
Factor | Impact of Substrate Temperature |
---|---|
Film Density | Higher temperatures lead to denser films with improved surface reactions and reduced defect density. |
Adhesion | Optimal temperatures improve bonding between the film and substrate. |
Crystallinity | Higher temperatures promote better crystalline structures in the film. |
Stress | Stress is influenced by temperature, as described by the thermal expansion formula. |
Deposition Rate | Minimal impact; temperature primarily affects film quality, not deposition speed. |
Material Compatibility | Different materials require specific temperatures for optimal film properties. |
Optimize your sputtering process with precise temperature control—contact our experts today for tailored solutions!