Brazing is a metal-joining technique that utilizes a filler metal with a lower melting point than the base materials being joined. The filler metal is heated until it melts and flows into the joint by capillary action, creating a strong, durable bond upon solidification. This process is distinct from welding, as it does not melt the base materials. Brazing is suitable for joining similar or dissimilar materials, including metals and ceramics, and is particularly valued for its ability to produce smooth, precise, and corrosion-resistant joints with minimal deformation. It is widely used in applications such as precision components, carbide tools, and printed circuit boards.
Key Points Explained:
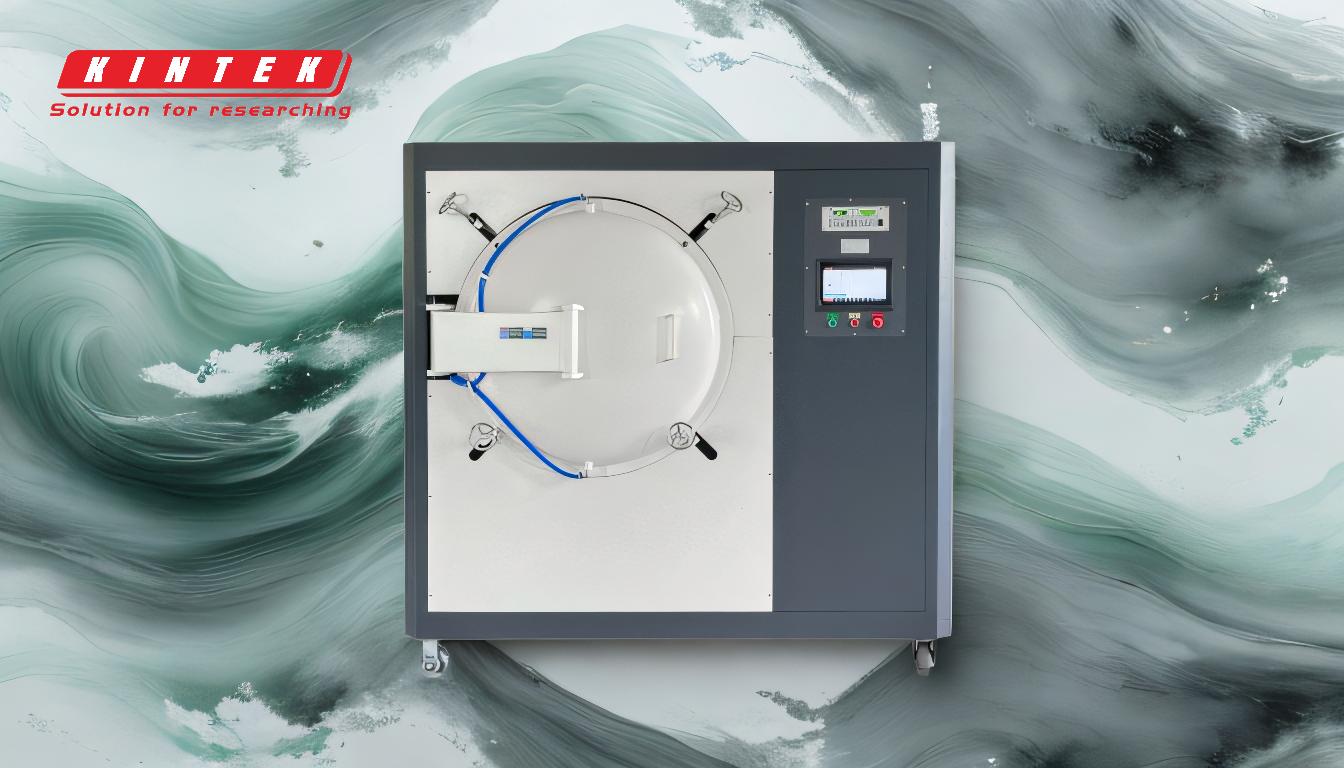
-
Definition and Process of Brazing:
- Brazing is a joining process where a filler metal, with a melting point lower than the base materials, is used to create a bond.
- The filler metal is heated to its melting point, allowing it to flow into the joint by capillary action.
- The joint is formed as the filler metal solidifies, creating a strong and durable connection.
-
Temperature Requirements:
- Brazing requires heating the joint to a temperature above the liquidus temperature of the filler metal but below the solidus temperature of the base materials.
- Technically, brazing is defined as using a filler metal that melts above 450°C. Processes using filler metals below this temperature are classified as soldering.
-
Capillary Action:
- Capillary action is the key mechanism that allows the molten filler metal to flow into the narrow gaps between the base materials.
- This ensures that the filler metal evenly distributes within the joint, creating a uniform and strong bond.
-
Advantages of Brazing:
- Minimal Deformation: Since the base materials are not melted, brazing results in minimal distortion or deformation of the parts being joined.
- Smooth Joints: Brazing produces aesthetically pleasing and smooth joints, making it ideal for precision and complex components.
- Versatility: Brazing can join similar or dissimilar materials, including metals and ceramics, and is suitable for multi-material components.
- Corrosion Resistance: The resulting joints are often corrosion-resistant, enhancing the durability of the assembled parts.
-
Applications of Brazing:
- Precision Components: Brazing is widely used in the manufacturing of precision components, such as carbide tools and printed circuit boards.
- Complex Assemblies: Its ability to join complex and multi-material components makes it a preferred method in industries requiring high precision.
- High-Temperature and High-Pressure Environments: Brazed joints can withstand high temperatures and pressures, making them suitable for demanding applications.
-
Comparison with Welding:
- Unlike welding, brazing does not melt the base materials, which reduces the risk of distortion and allows for the joining of dissimilar materials.
- Welding techniques, such as TIG and laser welding, are used for different applications, particularly where the melting of base materials is required or beneficial.
-
Automatic Brazing Machines:
- Modern brazing processes often utilize automatic brazing machines, which provide precise temperature control for consistent and accurate results.
- These machines enhance the efficiency and reliability of the brazing process, particularly in high-volume production environments.
-
Filler Materials:
- The filler materials used in brazing are typically alloys designed to have specific melting points and flow characteristics.
- The choice of filler material depends on the base materials being joined and the specific requirements of the application.
By understanding these key points, one can appreciate the technical nuances and advantages of brazing as a metal-joining technique. Its ability to create strong, precise, and aesthetically pleasing joints makes it a valuable process in various industrial applications.
Summary Table:
Key Aspect | Details |
---|---|
Definition | Joining process using a filler metal with a lower melting point than base materials. |
Temperature Requirements | Above 450°C for brazing; below for soldering. |
Capillary Action | Ensures even distribution of molten filler metal in joints. |
Advantages | Minimal deformation, smooth joints, versatility, corrosion resistance. |
Applications | Precision components, carbide tools, printed circuit boards, and more. |
Comparison with Welding | Does not melt base materials; suitable for dissimilar materials. |
Automatic Brazing Machines | Provide precise temperature control for consistent results. |
Filler Materials | Alloys with specific melting points and flow characteristics. |
Discover how brazing can enhance your manufacturing process—contact our experts today!