The temperature maintained in the calcination zone of a rotary kiln typically ranges between 800°C and 1300°C, depending on the specific application and material being processed. For indirect rotary kilns, the furnace tube temperature is often higher, ranging from 1200°C to 1300°C, while the material temperature remains below 1150°C. Temperature control is achieved through advanced systems, including thermocouple probes, real-time monitoring, and automated adjustments. Rotary kilns are versatile, supporting a wide temperature range from 200°C to 2500°C, and feature multiple heating zones that can be independently controlled to meet precise process requirements.
Key Points Explained:
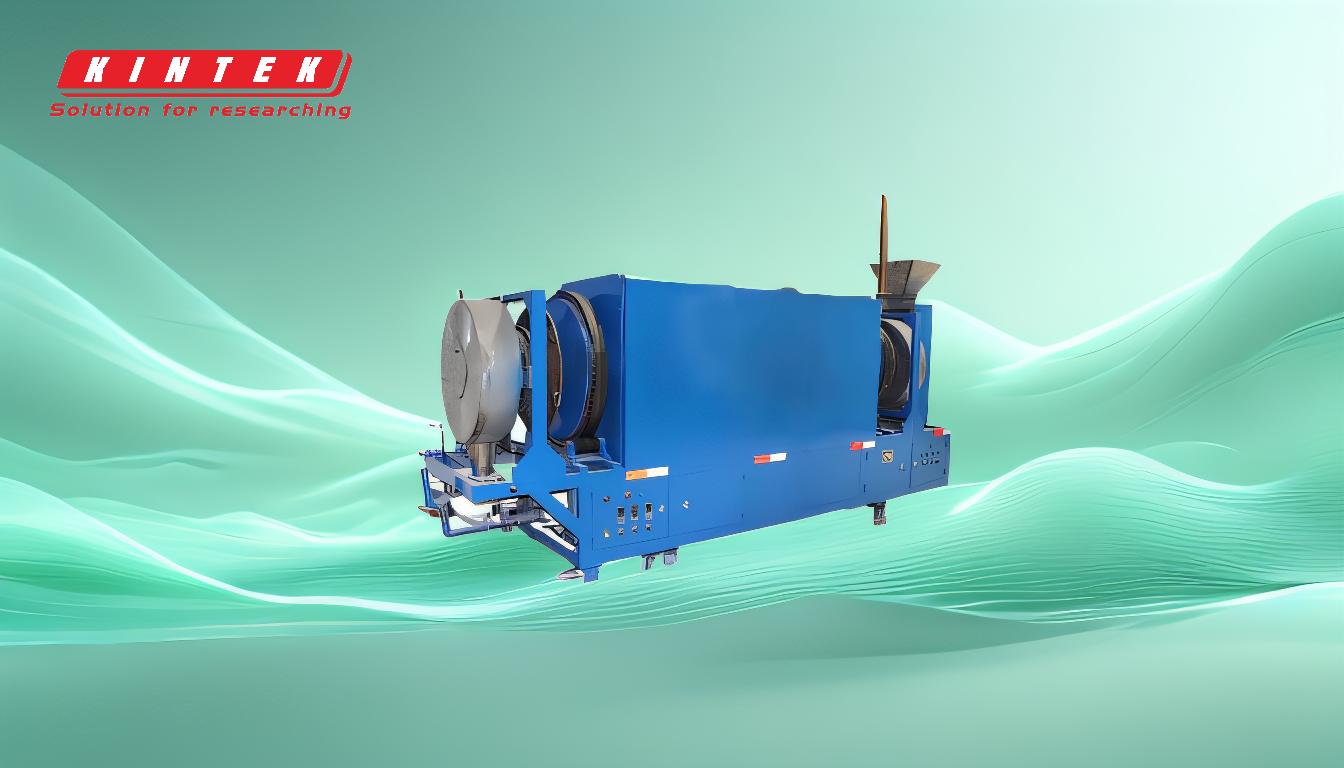
-
Typical Temperature Range in Calcination Zone:
- The calcination zone in a rotary kiln generally operates at temperatures between 800°C and 1300°C. This range is suitable for most industrial processes, such as cement production, lime calcination, and metal oxide processing.
- The specific temperature depends on the material being processed and the desired chemical or physical transformation.
-
Indirect Rotary Kiln Temperatures:
- In indirect rotary kilns, the furnace tube temperature is maintained at 1200°C to 1300°C, while the material temperature is kept below 1150°C. This ensures efficient heat transfer without overheating the material.
-
Temperature Control Mechanisms:
- Thermocouple Probes: Temperature is monitored using thermocouple probes placed at critical locations, such as the exhaust duct of the setting chamber. This allows for real-time temperature tracking.
- Remote Control: Operators can adjust the temperature by controlling the rotation speed of the kiln and stirring mechanisms. If temperatures exceed the desired range, cold ash or other cooling agents can be added.
- Real-Time Monitoring: The rotary kiln system displays real-time temperature change curves, enabling operators to monitor and adjust the process dynamically.
-
Versatility in Temperature Range:
- Rotary kilns are highly versatile and can support processes requiring temperatures as low as 200°C and as high as 2500°C. This makes them suitable for a wide range of industrial applications, from low-temperature drying to high-temperature calcination.
-
Zonal Heating and Independent Control:
- Rotary kilns often feature multiple heating zones, such as a pre-heating zone and a high-temperature heating zone. Each zone can be independently controlled to meet specific process requirements, ensuring optimal temperature distribution and material processing.
-
Stable Atmosphere Control:
- The rotary kiln's airtight structure ensures a stable atmosphere, which is crucial for maintaining consistent temperatures and preventing contamination or unwanted chemical reactions.
-
Data Recording and Process Optimization:
- The system records all temperature adjustment data, which can be used for process analysis and optimization. This feature helps improve efficiency and consistency in industrial operations.
By understanding these key points, equipment and consumable purchasers can make informed decisions about selecting rotary kilns that meet their specific temperature and process requirements.
Summary Table:
Key Aspect | Details |
---|---|
Calcination Zone Temperature | 800°C to 1300°C, depending on material and application. |
Indirect Kiln Temperatures | Furnace tube: 1200°C to 1300°C; Material: below 1150°C. |
Temperature Control | Thermocouple probes, real-time monitoring, remote adjustments. |
Versatility | Supports 200°C to 2500°C for diverse applications. |
Heating Zones | Multiple zones (e.g., pre-heating, high-temperature) with independent control. |
Atmosphere Control | Airtight structure ensures stable temperatures and prevents contamination. |
Data Recording | Records temperature adjustments for process optimization. |
Need a rotary kiln tailored to your process? Contact us today for expert guidance!