A hydrogen furnace, specifically a hydrogen atmosphere furnace, is a specialized heating device used in various industrial and laboratory applications, such as sintering, brazing, and annealing. The temperature of a hydrogen furnace can vary significantly depending on the specific application and design. Typically, these furnaces operate within a range of 800°C to 1600°C, but some advanced models can reach temperatures up to 1800°C or higher. The precise temperature control and uniformity are critical for ensuring the quality of the processes, especially when dealing with materials sensitive to oxidation or requiring precise thermal conditions. The use of hydrogen as the atmosphere prevents oxidation and allows for clean, high-temperature processing of metals and ceramics.
Key Points Explained:
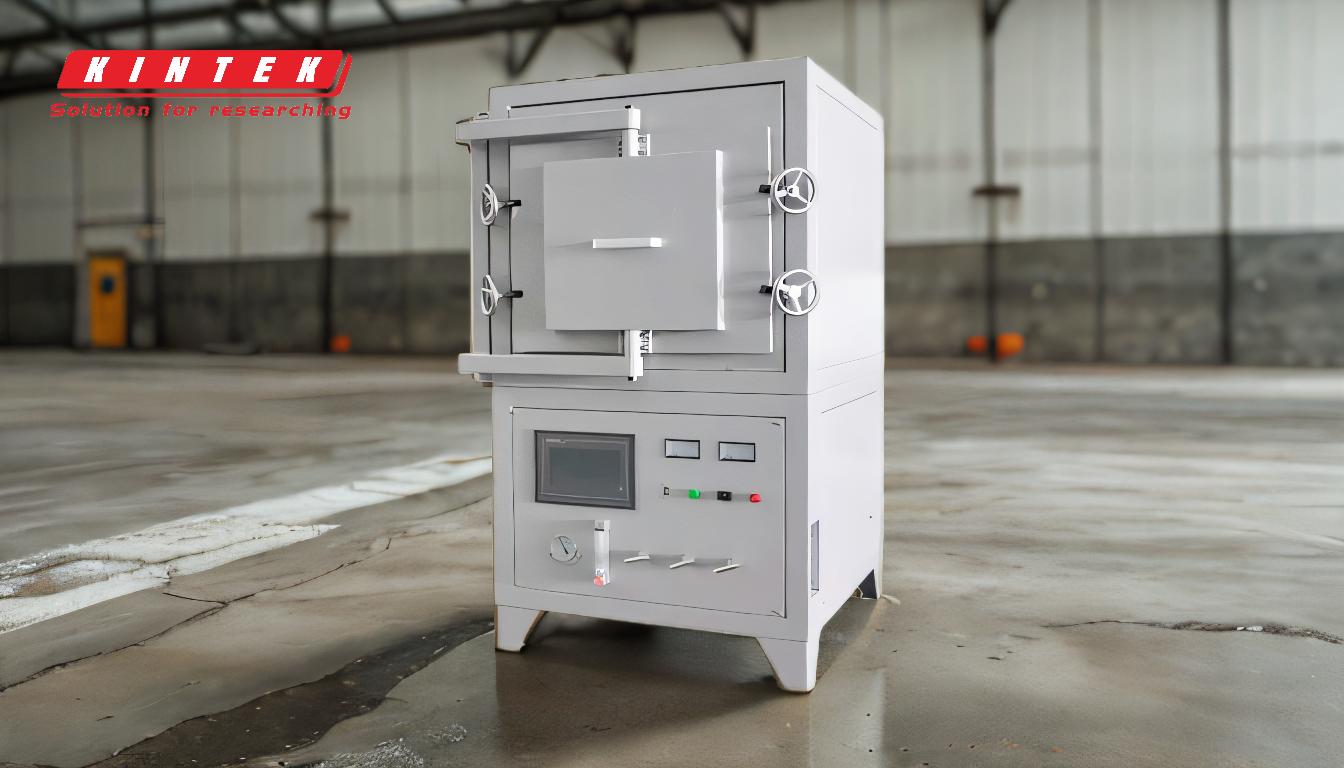
-
Definition and Purpose of a Hydrogen Furnace:
- A hydrogen furnace is a type of furnace that uses hydrogen gas as the atmosphere to create an oxygen-free environment. This is particularly important for processes like sintering, brazing, and annealing, where oxidation must be avoided to maintain material integrity.
- The hydrogen atmosphere furnace is designed to provide precise temperature control and uniformity, making it suitable for high-temperature applications in industries such as metallurgy, ceramics, and electronics.
-
Temperature Range of Hydrogen Furnaces:
- The operating temperature of a hydrogen furnace typically ranges from 800°C to 1600°C. However, advanced models can achieve temperatures up to 1800°C or higher.
- The specific temperature depends on the application. For example:
- Sintering: Often requires temperatures between 1200°C and 1600°C.
- Brazing: Typically performed at lower temperatures, around 800°C to 1100°C.
- Annealing: Can vary widely but often falls within 800°C to 1200°C.
-
Factors Influencing Temperature:
- Material Being Processed: Different materials require different temperature profiles. For instance, refractory metals like tungsten or molybdenum may need higher temperatures compared to standard steel alloys.
- Furnace Design: The insulation, heating elements, and control systems of the furnace determine its maximum achievable temperature and thermal uniformity.
- Hydrogen Purity: The quality of the hydrogen gas used can affect the furnace's performance, as impurities can lead to oxidation or contamination.
-
Advantages of Using Hydrogen Atmosphere:
- Oxidation Prevention: Hydrogen reacts with any residual oxygen, preventing oxidation of the materials being processed.
- Clean Processing: Hydrogen reduces surface oxides and contaminants, resulting in cleaner and higher-quality finished products.
- High Thermal Conductivity: Hydrogen has excellent thermal conductivity, enabling efficient and uniform heating.
-
Applications of Hydrogen Furnaces:
- Metallurgy: Used for sintering metal powders, annealing, and heat treatment of alloys.
- Ceramics: Essential for sintering ceramic materials and producing high-purity components.
- Electronics: Used in the production of semiconductors and other electronic components where oxidation must be avoided.
-
Safety Considerations:
- Hydrogen is highly flammable, so safety measures such as leak detection, proper ventilation, and explosion-proof designs are critical.
- The furnace must be equipped with precise temperature and atmosphere control systems to prevent overheating or hydrogen buildup.
-
Choosing the Right Hydrogen Furnace:
- When selecting a hydrogen atmosphere furnace, consider:
- Temperature Requirements: Ensure the furnace can reach and maintain the required temperature for your application.
- Atmosphere Control: Look for models with precise hydrogen flow and purity control.
- Thermal Uniformity: Opt for furnaces with excellent temperature uniformity to ensure consistent results.
- Safety Features: Prioritize furnaces with robust safety mechanisms to handle hydrogen gas safely.
- When selecting a hydrogen atmosphere furnace, consider:
-
Future Trends in Hydrogen Furnace Technology:
- Advances in materials and control systems are enabling higher temperatures and more precise thermal management.
- Integration with automation and IoT (Internet of Things) for real-time monitoring and control is becoming more common.
- Development of eco-friendly hydrogen production methods is reducing the environmental impact of using hydrogen furnaces.
By understanding the temperature capabilities and operational nuances of a hydrogen furnace, purchasers can make informed decisions to meet their specific processing needs while ensuring safety and efficiency.
Summary Table:
Aspect | Details |
---|---|
Temperature Range | 800°C to 1600°C (up to 1800°C+ for advanced models) |
Applications | Sintering (1200°C-1600°C), Brazing (800°C-1100°C), Annealing (800°C-1200°C) |
Key Advantages | Oxidation prevention, clean processing, high thermal conductivity |
Safety Considerations | Flammability of hydrogen requires leak detection and explosion-proof designs |
Selection Factors | Temperature requirements, atmosphere control, thermal uniformity, safety |
Need a hydrogen furnace for your high-temperature applications? Contact us today to find the perfect solution!