The temperature of a muffle furnace during ashing is typically set at 815±15°C, as this range ensures complete ashing of the sample without unnecessarily prolonging the process. Muffle furnaces are designed to operate at high temperatures, ranging from 800°C to 1800°C, making them ideal for processes like ashing, which require precise and elevated temperatures. Proper operation and maintenance, such as avoiding excessive humidity or corrosive environments, are critical to ensuring the longevity and efficiency of the furnace.
Key Points Explained:
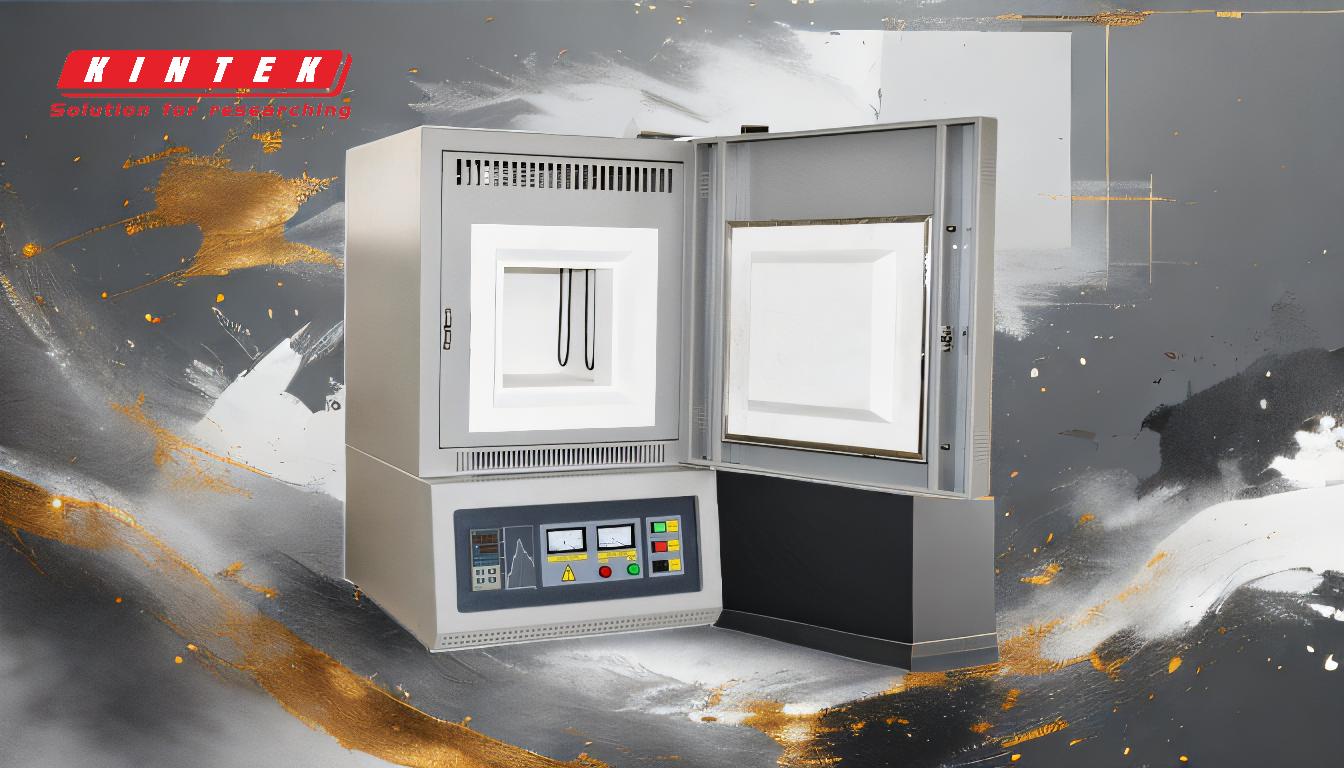
-
Ashing Temperature: 815±15°C
- The standard temperature for ashing in a muffle furnace is 815±15°C. This range ensures that the sample is completely ashed without over-extending the process, which could lead to unnecessary wear on the furnace or energy inefficiency.
- This temperature is chosen because it is high enough to combust organic materials thoroughly while avoiding excessive heat that might damage the furnace or sample.
-
Muffle Furnace Temperature Range
- Muffle furnaces are capable of operating at very high temperatures, typically ranging from 800°C to 1800°C. This makes them suitable for a variety of high-temperature applications, including ashing, annealing, hardening, and other heat treatment processes.
- The wide temperature range allows flexibility for different laboratory or industrial processes, but the specific temperature must be carefully selected based on the material and purpose.
-
Importance of Temperature Control
- Maintaining the correct temperature is critical for both the quality of the ashing process and the longevity of the furnace. Operating the furnace at 50°C below its maximum temperature is recommended to prevent damage to the heating elements and ensure a longer lifespan.
- Overheating or prolonged operation at maximum temperatures can degrade the furnace components, leading to increased maintenance costs and potential downtime.
-
Environmental Conditions for Operation
- Muffle furnaces must be operated in environments with relative humidity not exceeding 85% and free from conductive dust, explosive gases, or corrosive gases. These conditions help prevent damage to the furnace and ensure safe operation.
- When heating materials that release volatile gases, such as metals with grease, sealed containers or appropriate ventilation should be used to protect the heating elements from corrosion.
-
Avoiding Prolonged Ashing Time
- While the ashing process requires sufficient time to ensure complete combustion of the sample, arbitrarily prolonging the process is unfavorable. Prolonged exposure to high temperatures can degrade the sample or furnace components unnecessarily.
- The ashing time should be optimized to balance efficiency and sample integrity.
-
Applications Beyond Ashing
- Muffle furnaces are versatile and can be used for other high-temperature processes, such as annealing, hardening, normalizing, and carburizing. These processes often require precise temperature control and consistent heating conditions.
- Continuous furnaces, a type of muffle furnace, are specialized for specific processes and are operated at permanent temperature conditions for consistent results.
-
Material Considerations
- Only refractory laboratory materials should be used inside the furnace, as they can withstand the high temperatures required for ashing and other processes. Non-refractory materials may degrade or release harmful gases at elevated temperatures.
- Proper material selection ensures the safety and effectiveness of the furnace operation.
By understanding these key points, users can optimize the performance of their muffle furnace for ashing and other high-temperature processes while ensuring the longevity and safety of the equipment.
Summary Table:
Key Aspect | Details |
---|---|
Ashing Temperature | 815±15°C ensures complete ashing without unnecessary wear or energy loss. |
Temperature Range | 800°C to 1800°C, suitable for ashing, annealing, hardening, and more. |
Temperature Control | Operate 50°C below max temperature to prevent damage and extend lifespan. |
Environmental Conditions | Relative humidity ≤ 85%, avoid corrosive or explosive gases. |
Ashing Time | Optimize to balance efficiency and sample integrity. |
Applications | Ashing, annealing, hardening, normalizing, and carburizing. |
Material Considerations | Use only refractory materials to withstand high temperatures safely. |
Need help optimizing your muffle furnace for ashing or other processes? Contact our experts today for personalized advice!