Thermal evaporation deposition is a process where a solid material is heated in a high vacuum chamber to produce vapor pressure, leading to the formation of a thin film on a substrate. The temperature required for this process varies depending on the material being evaporated, as each material has a unique vapor pressure curve. Generally, the temperature must be high enough to generate sufficient vapor pressure for deposition but must also consider the thermal stability and properties of both the source material and the substrate. The process temperature is a critical parameter that influences deposition rate, film quality, and the final properties of the deposited film.
Key Points Explained:
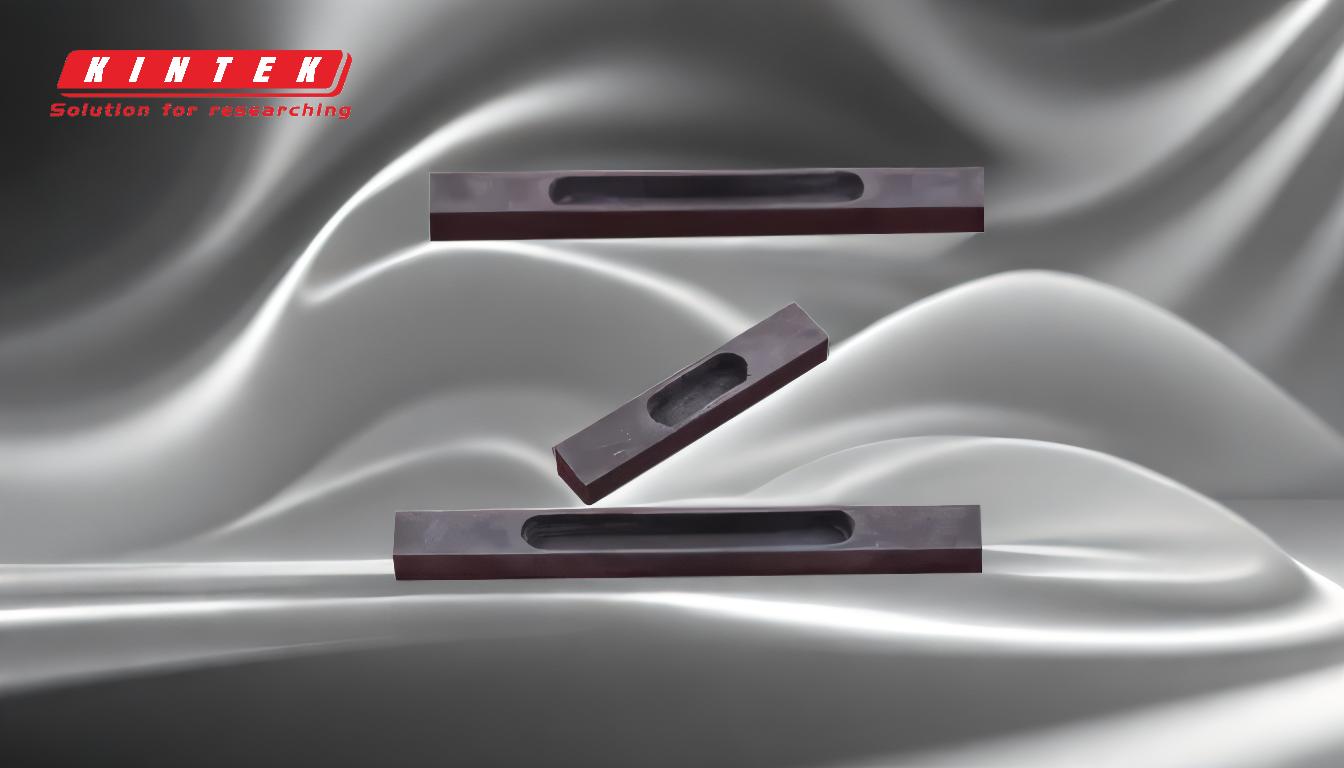
-
Temperature and Vapor Pressure Relationship:
- The temperature of thermal evaporation deposition is directly related to the vapor pressure of the material being evaporated. Higher temperatures increase vapor pressure, leading to more efficient evaporation and deposition.
- Each material has a specific temperature range at which it transitions from a solid to a vapor phase, known as its evaporation temperature. This temperature is determined by the material's vapor pressure curve.
-
Material-Specific Evaporation Temperatures:
- Different materials require different evaporation temperatures. For example, metals like aluminum evaporate at around 1200°C, while organic materials may evaporate at much lower temperatures, often below 300°C.
- The choice of material for thermal evaporation deposition depends on its reaction characteristics and thermal stability. Materials with high melting points require higher evaporation temperatures.
-
Impact of Temperature on Deposition Rate and Film Quality:
- Higher temperatures generally result in higher deposition rates due to increased vapor pressure. However, excessively high temperatures can lead to issues such as material decomposition or unwanted reactions.
- The temperature must be carefully controlled to ensure uniform film thickness, adhesion strength, and desired optical or electrical properties.
-
Vacuum Environment and Temperature Control:
- Thermal evaporation deposition occurs in a high vacuum chamber to minimize impurities and ensure a long mean free path for the vaporized material molecules.
- The vacuum environment allows for relatively low vapor pressures to be effective, meaning that even moderate temperatures can achieve sufficient evaporation.
-
Substrate Considerations:
- The substrate's thermal stability and surface properties must be considered when selecting the evaporation temperature. High temperatures can damage sensitive substrates or alter their properties.
- Substrate rotation and surface roughness also play a role in ensuring uniform deposition and film quality.
-
Practical Temperature Ranges:
- For most metals, evaporation temperatures range from 1000°C to 2000°C, depending on the material.
- Organic materials and polymers typically require much lower temperatures, often below 500°C, to avoid decomposition.
-
Temperature Control Mechanisms:
- The evaporation boat or filament is heated using an electric current, and the temperature is regulated by adjusting the power supply.
- Advanced systems may include feedback mechanisms to maintain precise temperature control, ensuring consistent deposition rates and film properties.
In summary, the temperature of thermal evaporation deposition is a critical parameter that varies depending on the material being evaporated and the desired film properties. It must be carefully controlled to balance deposition rate, film quality, and substrate integrity. Understanding the relationship between temperature, vapor pressure, and material properties is essential for optimizing the thermal evaporation process.
Summary Table:
Key Factor | Description |
---|---|
Temperature & Vapor Pressure | Higher temperatures increase vapor pressure, improving evaporation efficiency. |
Material-Specific Temperatures | Metals (e.g., aluminum) require ~1200°C; organics need <300°C. |
Deposition Rate & Film Quality | Controlled temperature ensures uniform thickness and desired properties. |
Vacuum Environment | High vacuum minimizes impurities and enables effective evaporation. |
Substrate Considerations | Thermal stability and surface properties must align with evaporation temperature. |
Practical Temperature Ranges | Metals: 1000°C–2000°C; organics: <500°C. |
Temperature Control Mechanisms | Electric current heats the evaporation boat, with feedback for precision. |
Need help optimizing your thermal evaporation deposition process? Contact our experts today!