Vacuum heat treatment is a specialized process used to enhance the properties of materials, particularly metals, by heating them in a vacuum environment to prevent oxidation and contamination. The temperature range for vacuum heat treatment varies widely depending on the material and the desired outcome, typically ranging from 175°C to 2400°C. The process involves precise temperature control, often using advanced systems like PID controllers or PLC automation, to ensure uniform heating and avoid temperature overshoots. The vacuum environment changes the heat transfer dynamics, requiring careful management of heating rates and soak times. This method is widely used in industries and research settings for applications like sintering, annealing, and hardening.
Key Points Explained:
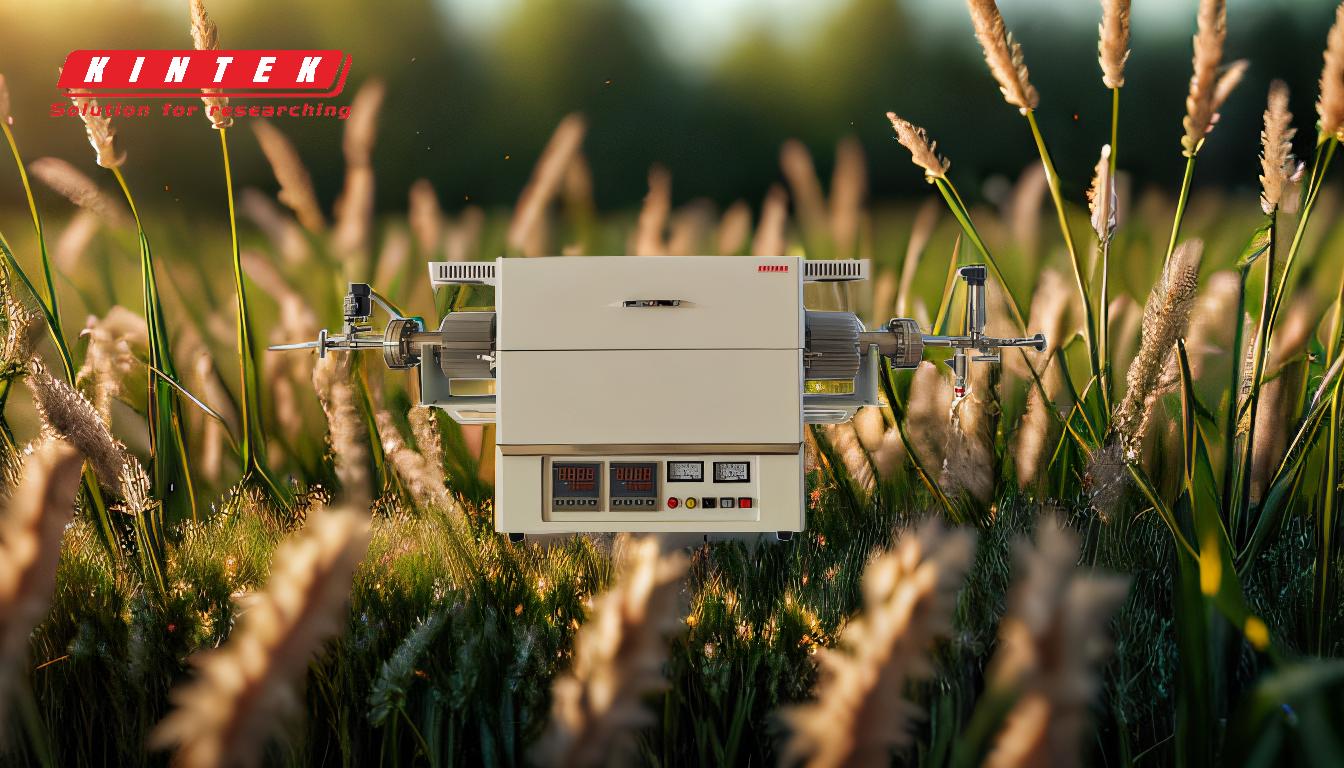
-
Temperature Range in Vacuum Heat Treatment:
- Vacuum heat treatment operates across a broad temperature spectrum, from as low as 175°C (350°F) for low-temperature processes to as high as 2400°C for specialized applications.
- Standard processes often fall within 800°C to 1100°C, with specific hold times to ensure material properties are achieved.
- For example, a typical program might start at 800°C, hold for 20 minutes, then slowly ramp up to 1100°C over an hour, followed by a 1.5-hour soak.
-
Temperature Control Systems:
- Precise temperature control is critical in vacuum heat treatment due to the unique heat transfer characteristics in a vacuum environment.
- Systems often include thermocouples for accurate temperature measurement and PID controllers, touch screens, or PLCs for regulation.
- Rapid heating rates and the transition from conduction/convection to radiation require advanced control mechanisms to prevent overshooting setpoints.
-
Challenges in Heat Transfer:
- In a vacuum, heat transfer shifts from conduction and convection to radiation, which complicates temperature management.
- This necessitates precise control over heating rates and soak times to ensure uniform treatment and avoid defects.
-
Equipment Features:
- A vacuum heat treat furnace typically includes water-cooled doors, gas flow systems with flowmeters, and the ability to introduce gases like hydrogen, argon, or nitrogen.
- These furnaces can achieve high vacuum levels (up to 5 Pa) and are designed for energy efficiency, rapid heating, and precise temperature control.
-
Applications and Material Considerations:
- The heating temperature is selected based on the material, technical requirements, and desired outcomes (e.g., hardness, strength, or reduced deformation).
- For instance, low-temperature processes (175-730°C) are used for specific applications, while higher temperatures (up to 2400°C) are reserved for specialized treatments.
-
Vacuum System Components:
- The vacuum system includes vacuum pumps, valves, measuring instruments, and pipelines, which work together to maintain the required vacuum level and ensure consistent performance.
-
Process Optimization:
- The goal is to find the optimal heating temperature that minimizes deformation while meeting performance requirements.
- This involves balancing factors like heating rate, soak time, and cooling rate to achieve the desired material properties.
By understanding these key points, equipment and consumable purchasers can make informed decisions about selecting and operating vacuum heat treatment systems for their specific needs.
Summary Table:
Aspect | Details |
---|---|
Temperature Range | 175°C to 2400°C, depending on material and application |
Standard Process Range | 800°C to 1100°C with specific hold times |
Temperature Control | PID controllers, PLCs, and thermocouples for precise regulation |
Heat Transfer Challenges | Shifts to radiation in a vacuum, requiring careful heating rate management |
Equipment Features | Water-cooled doors, gas flow systems, high vacuum levels (up to 5 Pa) |
Applications | Sintering, annealing, hardening, and specialized treatments |
Optimization Goal | Minimize deformation while achieving desired material properties |
Need help selecting the right vacuum heat treatment system? Contact our experts today for personalized advice!