Compression molding is a manufacturing process used to shape materials like plastics, composites, and rubber by applying heat and pressure. The temperature range for compression molding varies depending on the material being processed, but it typically falls between 120°C to 200°C (248°F to 392°F) for thermoplastics and 130°C to 180°C (266°F to 356°F) for thermosetting materials. The process involves heating the material to a pliable state, placing it into a mold, and applying pressure to shape it. The temperature must be carefully controlled to ensure proper curing, flow, and final product quality. Factors like material type, mold design, and desired properties influence the specific temperature range used.
Key Points Explained:
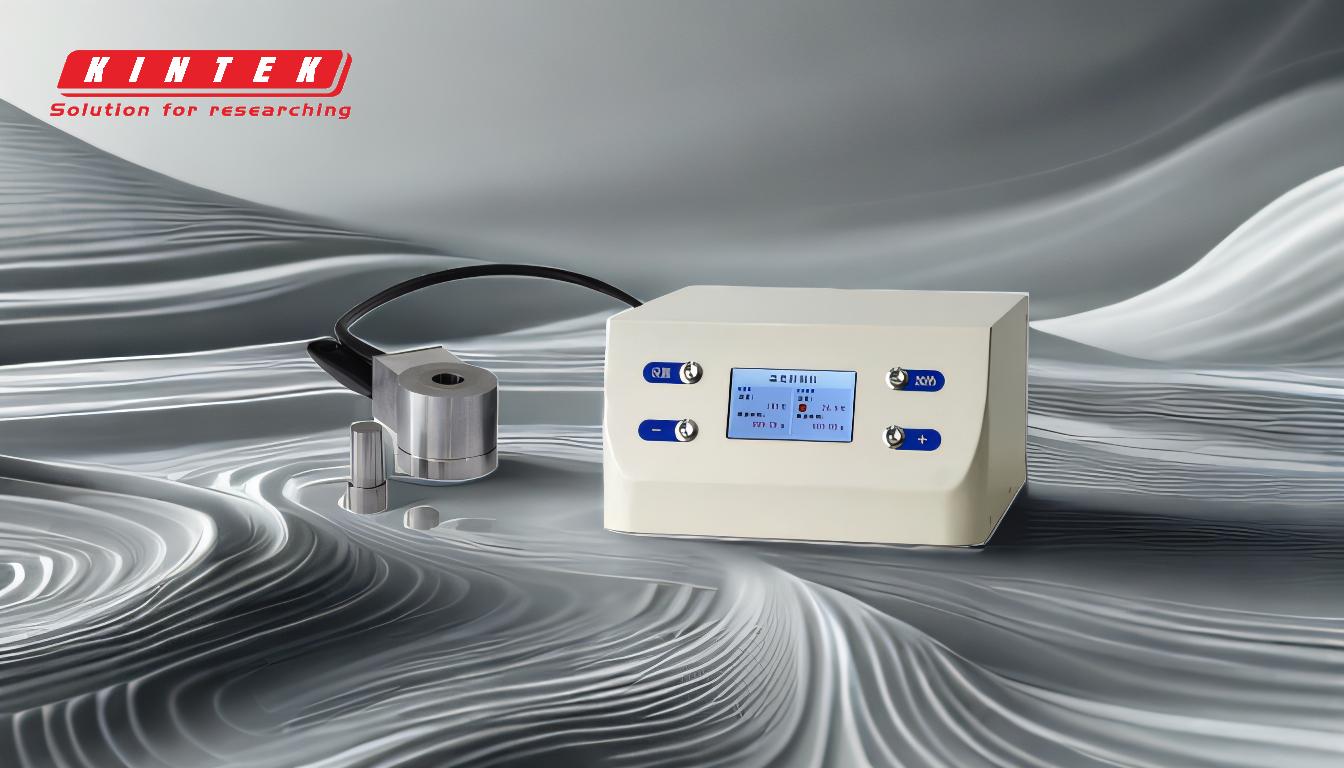
-
Temperature Range for Thermoplastics:
- Thermoplastics, such as polyethylene and polypropylene, typically require a temperature range of 120°C to 200°C (248°F to 392°F) for compression molding.
- This range ensures the material becomes soft and pliable enough to flow into the mold cavity without degrading.
- Higher temperatures may cause thermal degradation, while lower temperatures can result in incomplete molding.
-
Temperature Range for Thermosetting Materials:
- Thermosetting materials, such as phenolic resins and epoxy, generally require a slightly lower temperature range of 130°C to 180°C (266°F to 356°F).
- These materials undergo a chemical reaction (curing) during molding, which hardens them into their final shape.
- The temperature must be precise to ensure proper curing and avoid defects like under-curing or over-curing.
-
Factors Influencing Temperature Selection:
- Material Properties: Different materials have unique melting points, thermal stability, and curing requirements.
- Mold Design: Complex molds may require higher temperatures to ensure material flows into all cavities.
- Product Requirements: Desired properties like strength, flexibility, and surface finish influence the temperature settings.
- Cycle Time: Higher temperatures can reduce cycle times but must be balanced against the risk of material degradation.
-
Importance of Temperature Control:
- Precise temperature control is critical to achieving consistent product quality.
- Uneven heating can lead to defects like warping, voids, or incomplete curing.
- Modern compression molding machines often use advanced heating systems and sensors to maintain uniform temperatures.
-
Common Applications and Materials:
- Compression molding is widely used in industries like automotive, aerospace, and consumer goods.
- Common materials include rubber (for seals and gaskets), composites (for lightweight parts), and thermoplastics (for durable components).
- Each material has specific temperature requirements to optimize performance and durability.
-
Comparison with Other Molding Processes:
- Compression molding typically operates at lower temperatures compared to injection molding, which can reach up to 300°C (572°F).
- The process is ideal for large, relatively simple parts and materials that require high strength and durability.
By understanding the temperature range and its influencing factors, manufacturers can optimize the compression molding process for high-quality, consistent results.
Summary Table:
Material Type | Temperature Range | Key Considerations |
---|---|---|
Thermoplastics | 120°C to 200°C (248°F-392°F) | Ensures pliability without degradation; avoid higher or lower temperatures. |
Thermosetting Materials | 130°C to 180°C (266°F-356°F) | Requires precise curing; avoid under- or over-curing for optimal results. |
Factors Influencing Range | - Material properties, mold design, product requirements, and cycle time. |
Need help optimizing your compression molding process? Contact our experts today for tailored solutions!