Heat treatment is a critical process in metallurgy and materials science, used to alter the physical and sometimes chemical properties of materials, primarily metals. The temperature range for heat treatment varies widely depending on the material being treated and the desired outcome. Typically, heat treatment involves heating the material to a specific temperature, holding it at that temperature for a certain period, and then cooling it in a controlled manner. The temperature ranges can be as low as 200°C for some tempering processes to as high as 1200°C for processes like austenitizing in steel. The choice of temperature is crucial as it directly affects the microstructure and, consequently, the mechanical properties of the material.
Key Points Explained:
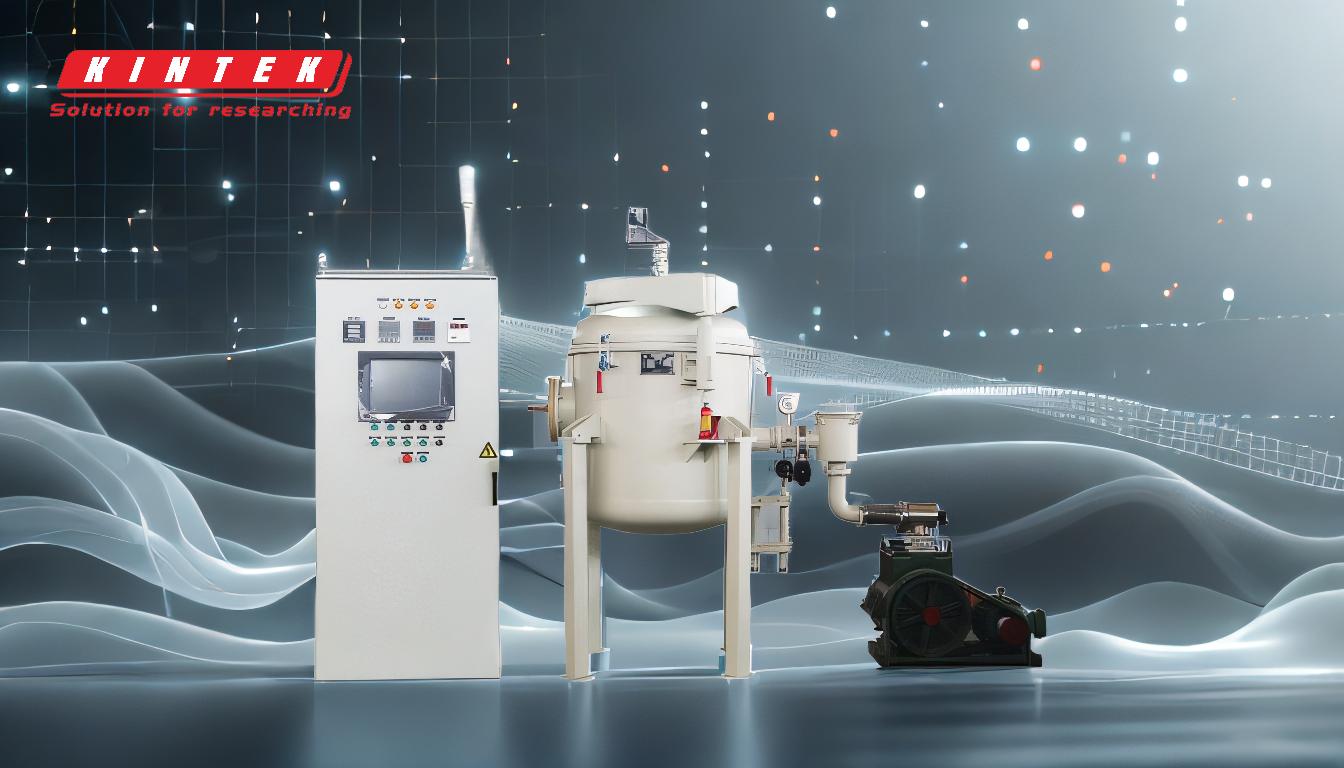
-
Purpose of Heat Treatment:
- Heat treatment is used to enhance properties such as hardness, strength, toughness, ductility, and resistance to wear and corrosion. The process can also relieve internal stresses, improve machinability, and prepare the material for further processing.
-
Common Heat Treatment Processes and Their Temperature Ranges:
- Annealing: Typically involves heating the material to a temperature between 700°C and 900°C for steel, holding it at that temperature, and then slowly cooling it. This process softens the material, improves ductility, and refines the grain structure.
- Normalizing: Similar to annealing but involves cooling in air. The temperature range is usually between 800°C and 950°C for steel. This process results in a finer pearlitic structure and improved mechanical properties.
- Quenching: Involves heating the material to a temperature above its critical point (around 850°C to 950°C for steel) and then rapidly cooling it, often in water, oil, or air. This process increases hardness and strength but may reduce ductility.
- Tempering: After quenching, the material is reheated to a lower temperature (between 150°C and 650°C) to reduce brittleness and improve toughness. The exact temperature depends on the desired balance between hardness and toughness.
- Austenitizing: Involves heating steel to a temperature above its upper critical temperature (around 900°C to 1200°C) to form austenite, followed by quenching to achieve high hardness.
-
Material-Specific Considerations:
- Steel: The most commonly heat-treated material, with temperature ranges varying based on the type of steel (e.g., carbon steel, alloy steel, stainless steel). For example, carbon steel is typically heated to between 800°C and 900°C for annealing.
- Aluminum: Heat treatment temperatures are generally lower, ranging from 400°C to 500°C for processes like solution heat treatment, followed by aging at lower temperatures (100°C to 200°C).
- Titanium: Heat treatment involves heating to temperatures between 700°C and 1000°C, depending on the alloy and desired properties.
-
Factors Influencing Temperature Selection:
- Material Composition: Different alloys have different critical temperatures and phase transformation points.
- Desired Properties: The end goal (e.g., hardness, toughness) dictates the specific temperature and cooling rate.
- Component Geometry: Thicker sections may require longer soaking times or different cooling rates to achieve uniform properties.
- Heating and Cooling Rates: Controlled rates are essential to avoid cracking, warping, or undesirable microstructures.
-
Equipment Used in Heat Treatment:
- Furnaces: Various types of furnaces are used, including box furnaces, pit furnaces, and continuous furnaces, depending on the scale and type of heat treatment.
- Quenching Media: Water, oil, polymer solutions, and air are common quenching media, each providing different cooling rates.
- Temperature Control: Precise temperature control is crucial, often achieved using thermocouples and advanced control systems.
Understanding the temperature range for heat treatment is essential for achieving the desired material properties. Each process and material requires careful consideration of temperature, time, and cooling rate to ensure optimal results.
Summary Table:
Process | Temperature Range | Key Effects |
---|---|---|
Annealing | 700°C - 900°C (Steel) | Softens material, improves ductility, refines grain structure. |
Normalizing | 800°C - 950°C (Steel) | Produces finer pearlitic structure, enhances mechanical properties. |
Quenching | 850°C - 950°C (Steel) | Increases hardness and strength, may reduce ductility. |
Tempering | 150°C - 650°C | Reduces brittleness, improves toughness. |
Austenitizing | 900°C - 1200°C (Steel) | Forms austenite, achieves high hardness after quenching. |
Aluminum Treatment | 400°C - 500°C | Solution heat treatment, followed by aging at 100°C - 200°C. |
Titanium Treatment | 700°C - 1000°C | Varies by alloy, enhances specific properties. |
Need expert advice on heat treatment processes? Contact us today to achieve optimal material performance!