Sintering is a thermal process that transforms loose fine particles into a solid, coherent mass by applying heat and/or pressure without fully melting the materials. This process is widely used in industries such as powder metallurgy, ceramics, and plastics to create durable and strong components. The sintering process typically involves three stages: forming a green part with a bonding agent, removing the bonding agent through heating, and fusing the particles at elevated temperatures. During sintering, atoms diffuse across particle boundaries, bonding them together to form a solid piece. This method is particularly useful for materials with high melting points, such as tungsten and molybdenum, and is essential for producing complex shapes and enhancing material properties.
Key Points Explained:
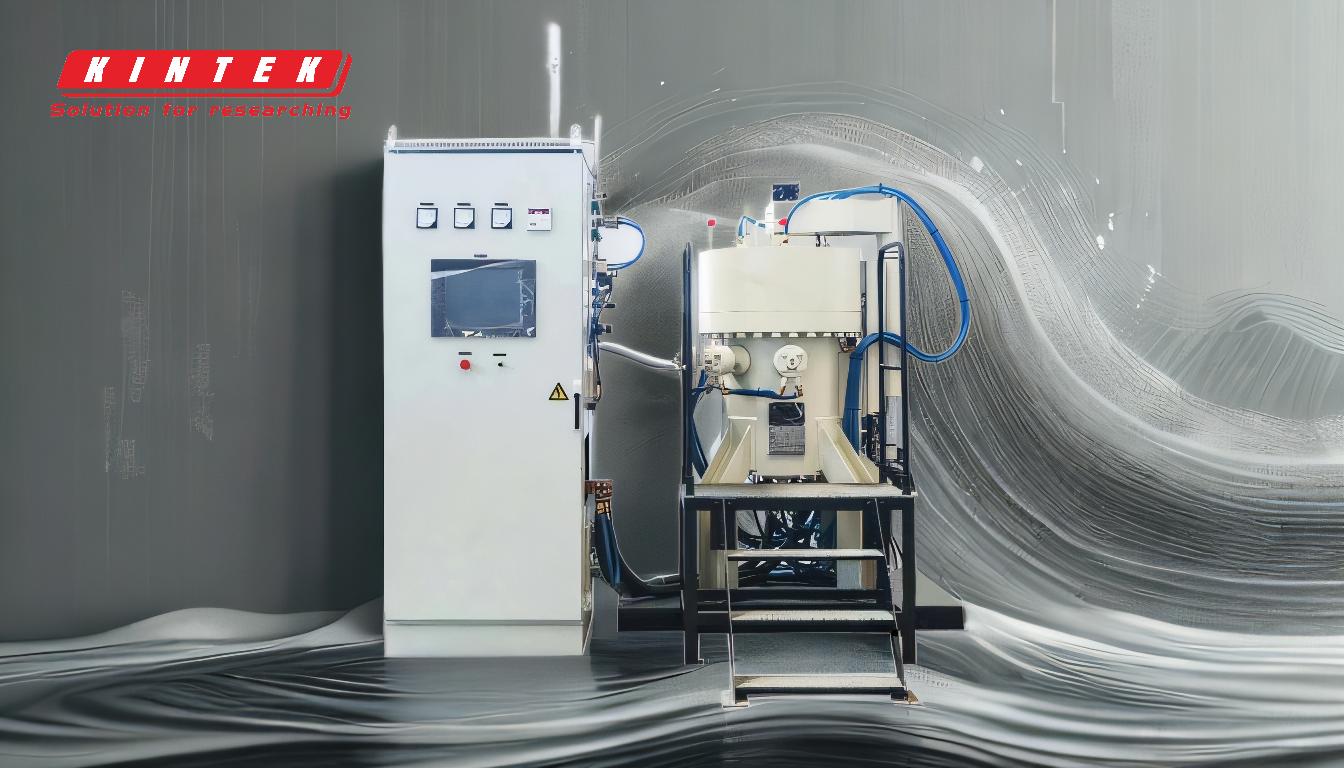
-
Definition of Sintering:
- Sintering is a thermal process that converts loose fine particles into a solid mass by applying heat and/or pressure without fully melting the materials.
- It is used in various industries, including powder metallurgy, ceramics, and plastics, to create durable and strong components.
-
Stages of the Sintering Process:
-
Stage 1: Forming the Green Part:
- A primary powder blend is mixed with a bonding agent (often a wax or polymer) and formed into the desired shape.
- The bonding agent temporarily holds the powder particles together.
-
Stage 2: Removal of the Bonding Agent:
- The green part is heated, causing the bonding agent to evaporate or burn away.
- This step prepares the material for the final bonding stage.
-
Stage 3: Particle Fusion:
- The temperature is increased to a point where the particles begin to fuse:
- Surface Melting: The surfaces of the particles melt slightly, causing them to bond at their contact points.
- Intermediate Bonding: An intermediate bonding agent (e.g., bronze) melts and couples the particles without altering the primary material.
- This stage results in a solid, cohesive mass with improved mechanical properties.
- The temperature is increased to a point where the particles begin to fuse:
-
Stage 1: Forming the Green Part:
-
Mechanism of Sintering:
-
Atomic Diffusion:
- Atoms diffuse across the boundaries of the particles, fusing them together.
- This diffusion occurs due to the high temperature and pressure applied during the process.
-
No Full Melting:
- The materials are not melted to the point of liquefaction, preserving their original properties while enhancing strength and durability.
-
Atomic Diffusion:
-
Applications of Sintering:
-
Powder Metallurgy:
- Used to produce metal components with complex shapes and high strength.
-
Ceramics:
- Enables the creation of durable ceramic products, such as pottery and industrial components.
-
Plastics and Other Materials:
- Applied to bond plastic particles or other materials into solid forms.
-
Powder Metallurgy:
-
Advantages of Sintering:
-
Material Efficiency:
- Minimizes material waste by using fine powders.
-
Complex Shapes:
- Allows for the production of intricate and precise shapes that are difficult to achieve with traditional manufacturing methods.
-
Enhanced Properties:
- Improves the mechanical properties of materials, such as hardness, strength, and durability.
-
High-Temperature Materials:
- Ideal for materials with extremely high melting points, such as tungsten and molybdenum.
-
Material Efficiency:
-
Materials Suitable for Sintering:
- Metals: Commonly sintered metals include iron, copper, and stainless steel.
- Ceramics: Used for pottery, tiles, and industrial ceramics.
- Plastics: Applied in the production of plastic components.
- High-Melting-Point Materials: Tungsten, molybdenum, and other refractory metals.
-
Key Considerations for Sintering:
-
Temperature Control:
- Precise temperature regulation is crucial to ensure proper particle fusion without full melting.
-
Pressure Application:
- Pressure aids in compacting the particles and enhancing atomic diffusion.
-
Bonding Agent Selection:
- The choice of bonding agent affects the green part's stability and the final product's quality.
-
Material Properties:
- The sintering process must be tailored to the specific material's melting point, particle size, and desired properties.
-
Temperature Control:
In summary, sintering is a versatile and efficient thermal process that transforms fine particles into solid, durable materials without fully melting them. By understanding its stages, mechanisms, and applications, manufacturers can leverage sintering to produce high-quality components across various industries.
Summary Table:
Aspect | Details |
---|---|
Definition | A thermal process converting fine particles into a solid mass using heat/pressure. |
Stages | 1. Forming the green part 2. Removing the bonding agent 3. Particle fusion |
Key Mechanism | Atomic diffusion across particle boundaries without full melting. |
Applications | Powder metallurgy, ceramics, plastics, and high-melting-point materials. |
Advantages | Material efficiency, complex shapes, enhanced properties, high-temperature suitability. |
Materials | Metals (iron, copper), ceramics, plastics, tungsten, molybdenum. |
Key Considerations | Temperature control, pressure application, bonding agent selection, material properties. |
Discover how sintering can optimize your production process—contact our experts today for tailored solutions!