Heat treatment ovens, also known as heat treatment furnaces, are specialized heating chambers used to alter the physical and mechanical properties of metals and alloys through controlled heating and cooling processes. They are essential in industries like aerospace, automotive, and manufacturing, where material performance is critical. These ovens ensure uniform heating, which is vital for achieving consistent material properties such as strength, hardness, and ductility. By regulating temperature precisely, heat treatment ovens enhance the durability, fatigue resistance, and overall performance of components, making them suitable for demanding applications.
Key Points Explained:
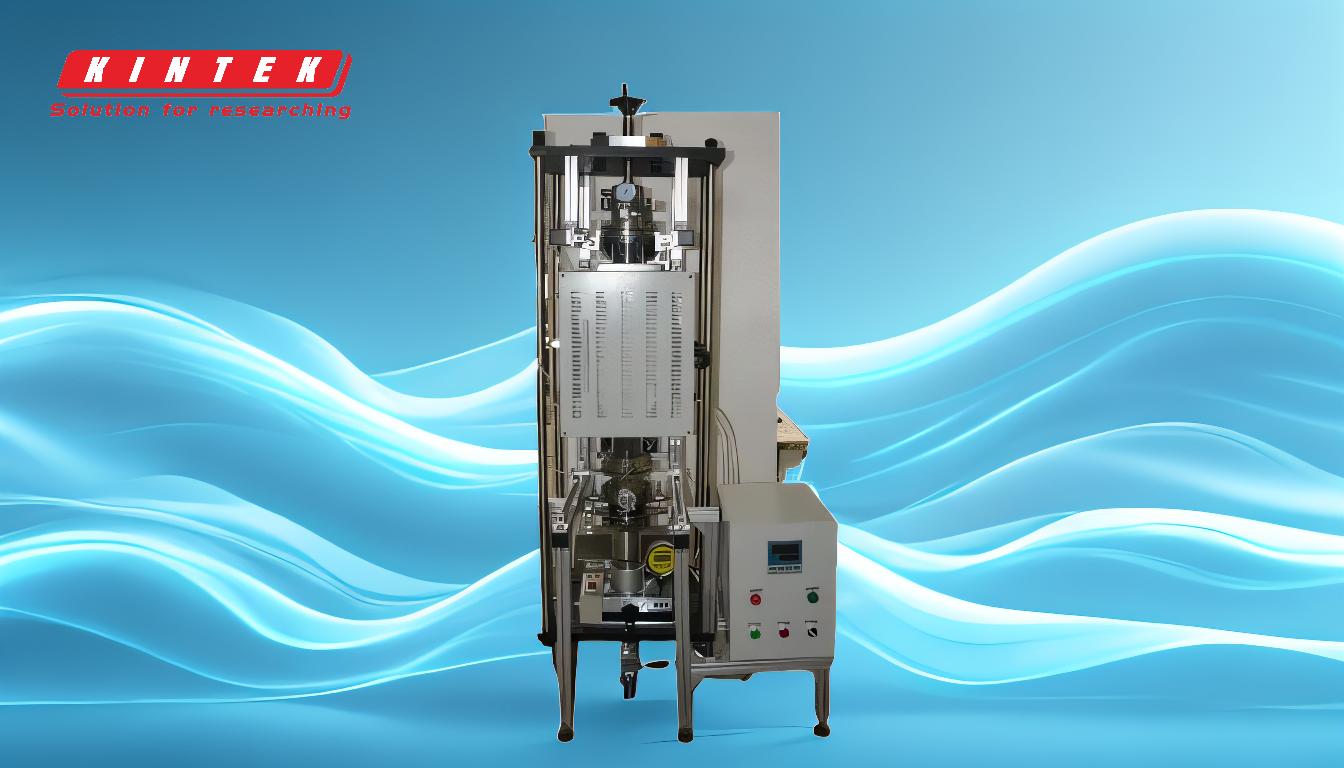
-
Purpose of Heat Treatment Ovens:
- Heat treatment ovens are designed to heat metals and alloys to specific temperatures and then cool them in a controlled manner. This process alters the material's microstructure, improving its mechanical properties.
- They are used to enhance properties such as hardness, strength, toughness, and ductility, making materials more suitable for industrial applications.
-
Applications in Aerospace and Other Industries:
- In aerospace, heat treatment ovens are critical for ensuring that components can withstand extreme conditions. They improve grain structure, reduce stress, and enhance fatigue life, which are essential for aircraft safety and performance.
- Other industries, such as automotive and manufacturing, also rely on heat treatment ovens to produce durable and reliable components.
-
Uniform Heating and Temperature Control:
- Maintaining a constant and uniform temperature is crucial in heat treatment. Uneven heating can lead to inconsistent material properties, such as underheated or overheated areas, compromising the quality of the treated components.
- Heat treatment ovens are designed to regulate and maintain precise temperatures, ensuring that all parts of the material are heated uniformly.
-
Types of Heat Treatment Processes:
- Annealing: Softens the material, improves ductility, and reduces internal stresses.
- Hardening: Increases hardness and strength by heating and then rapidly cooling the material.
- Tempering: Reduces brittleness and improves toughness after hardening.
- Normalizing: Refines the grain structure and improves mechanical properties.
-
Benefits of Heat Treatment Ovens:
- Enhanced Material Properties: Improves strength, hardness, and wear resistance.
- Extended Component Lifespan: Increases fatigue life and durability, reducing the need for frequent replacements.
- Versatility: Can be used for both ferrous and non-ferrous metals, making them suitable for a wide range of applications.
-
Key Features of Heat Treatment Ovens:
- Precision Temperature Control: Ensures consistent and reproducible results.
- Uniform Heating Chambers: Prevents hotspots and ensures even heat distribution.
- Durability and Reliability: Built to withstand high temperatures and prolonged use.
- Customization: Can be tailored to meet specific industry requirements, such as size, temperature range, and heating method.
-
Importance in Industrial Applications:
- Heat treatment ovens are indispensable in industries where material performance is critical. They ensure that components meet stringent quality standards and perform reliably under demanding conditions.
- By improving material properties, these ovens contribute to the safety, efficiency, and longevity of industrial machinery and equipment.
In summary, heat treatment ovens are vital tools in modern manufacturing and engineering. They enable precise control over material properties, ensuring that components meet the rigorous demands of industries like aerospace, automotive, and beyond. Their ability to enhance strength, durability, and performance makes them an essential investment for any organization focused on quality and reliability.
Summary Table:
Key Aspect | Details |
---|---|
Purpose | Alter physical and mechanical properties of metals and alloys. |
Applications | Aerospace, automotive, manufacturing. |
Key Benefits | Enhanced strength, hardness, durability, and fatigue resistance. |
Types of Processes | Annealing, hardening, tempering, normalizing. |
Key Features | Precision temperature control, uniform heating, durability, customization. |
Industrial Importance | Ensures quality, reliability, and performance of critical components. |
Upgrade your material performance with heat treatment ovens—contact our experts today!