The vacuum level for brazing in a vacuum brazing furnace is critical for achieving high-quality joints, particularly in industries like aerospace, medical devices, and metallurgical research. A vacuum environment minimizes oxidation, ensures even heat distribution, and allows for precise temperature control. The highest achievable vacuum degree in such furnaces is typically around 7 × 10^-3 Pa, which is essential for removing residual gases and preventing contamination during the brazing process. The furnace operates at temperatures ranging from 500°C to 1200°C, depending on the materials being joined, and ensures consistent results for high-volume or continuous brazing applications.
Key Points Explained:
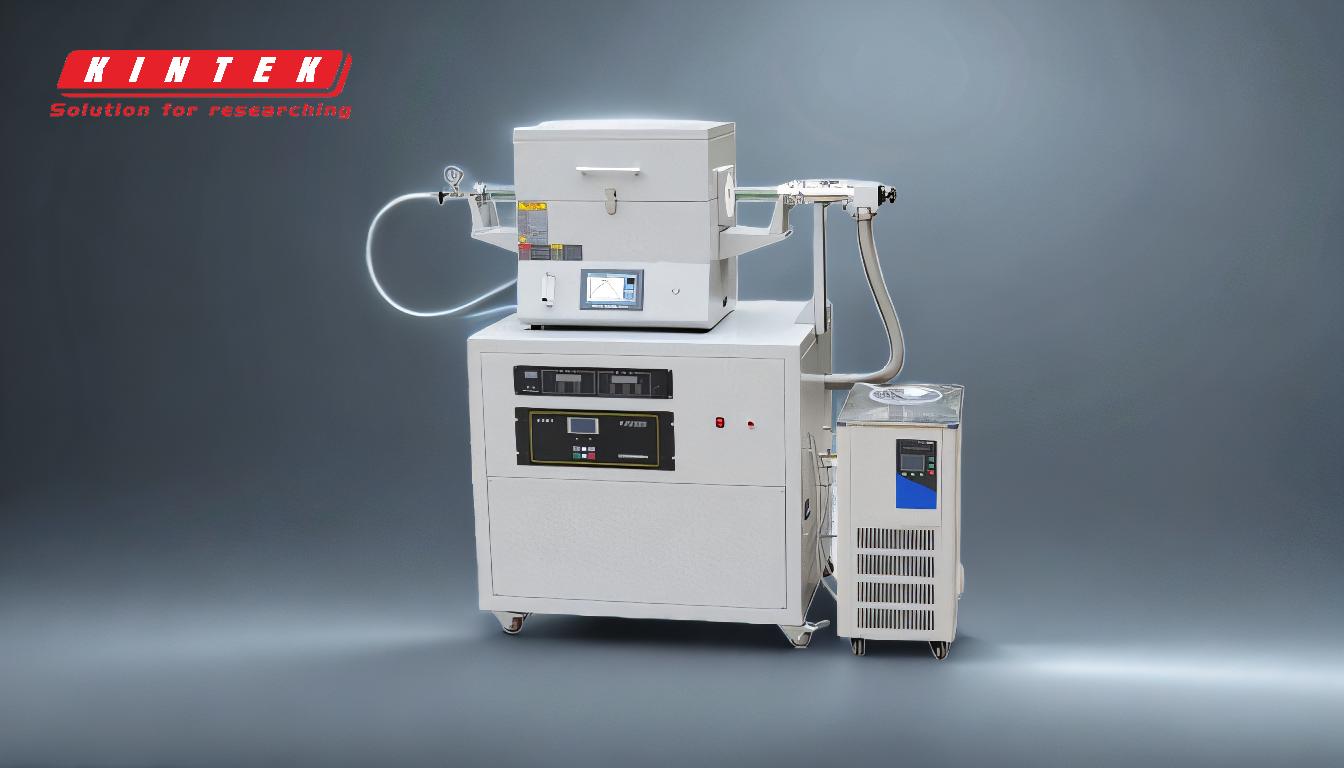
-
Importance of Vacuum Level in Brazing:
- A vacuum environment is crucial for brazing as it prevents oxidation and contamination, which can weaken joints. The vacuum level ensures that residual gases are removed, creating a clean environment for the filler metal to flow and bond with the base metals.
- The highest vacuum degree achievable in a vacuum brazing furnace is generally 7 × 10^-3 Pa. This level is sufficient for most brazing applications, especially in industries requiring high precision, such as aerospace and medical devices.
-
Temperature Range for Brazing:
- Brazing in a vacuum furnace typically occurs at temperatures between 500°C and 1200°C. This range allows the filler metal to melt and flow, creating strong, durable joints.
- The furnace's ability to maintain precise temperature control ensures consistent results, even for complex or high-volume brazing processes.
-
Advantages of Vacuum Brazing:
- Oxidation Prevention: The vacuum environment eliminates the need for flux, reducing oxidation and corrosion issues.
- Even Heat Distribution: Uniform heating ensures consistent part production and clean joints.
- Repeatable Heating Cycles: The furnace can accurately repeat heating cycles, making it ideal for continuous or high-volume brazing.
-
Applications of Vacuum Brazing:
- Vacuum brazing is widely used in industries such as aerospace, particle physics, and metallurgical research. It is also employed for joining components in heating and cooling assemblies, micro-channel heat exchangers, aircraft components, sensors, and medical devices.
- The process meets stringent industry standards, such as NADCAP requirements, ensuring high-quality results.
-
Operational Considerations:
- During the brazing process, operators must monitor water pressure, flow, and temperature to ensure the furnace operates safely and efficiently. Cooling water must continue to flow even after the furnace is stopped to prevent damage.
- The furnace's sophisticated cycle programming allows for precise control, ensuring optimal results for each workpiece.
By understanding the vacuum level, temperature range, and operational considerations, users can effectively utilize a vacuum brazing furnace for high-quality brazing applications.
Summary Table:
Key Aspect | Details |
---|---|
Vacuum Level | 7 × 10^-3 Pa (highest achievable) |
Temperature Range | 500°C to 1200°C |
Advantages | Oxidation prevention, even heat distribution, repeatable heating cycles |
Applications | Aerospace, medical devices, metallurgical research, and more |
Operational Considerations | Monitor water pressure, flow, and temperature for safe and efficient use |
Ready to achieve flawless brazing results? Contact us today to learn more about our vacuum brazing furnaces!