Vapour deposition is a widely used method for synthesizing nanoparticles, involving the conversion of a material into its vapor phase, which then condenses to form nanoparticles on a substrate. This technique is highly versatile and can be used to produce nanoparticles with precise control over size, shape, and composition. It is particularly useful in applications requiring high purity and uniformity, such as in electronics, optics, and catalysis. The process can be categorized into two main types: physical vapor deposition (PVD) and chemical vapor deposition (CVD). Both methods involve different mechanisms and conditions but share the common goal of depositing thin films or nanoparticles onto a substrate.
Key Points Explained:
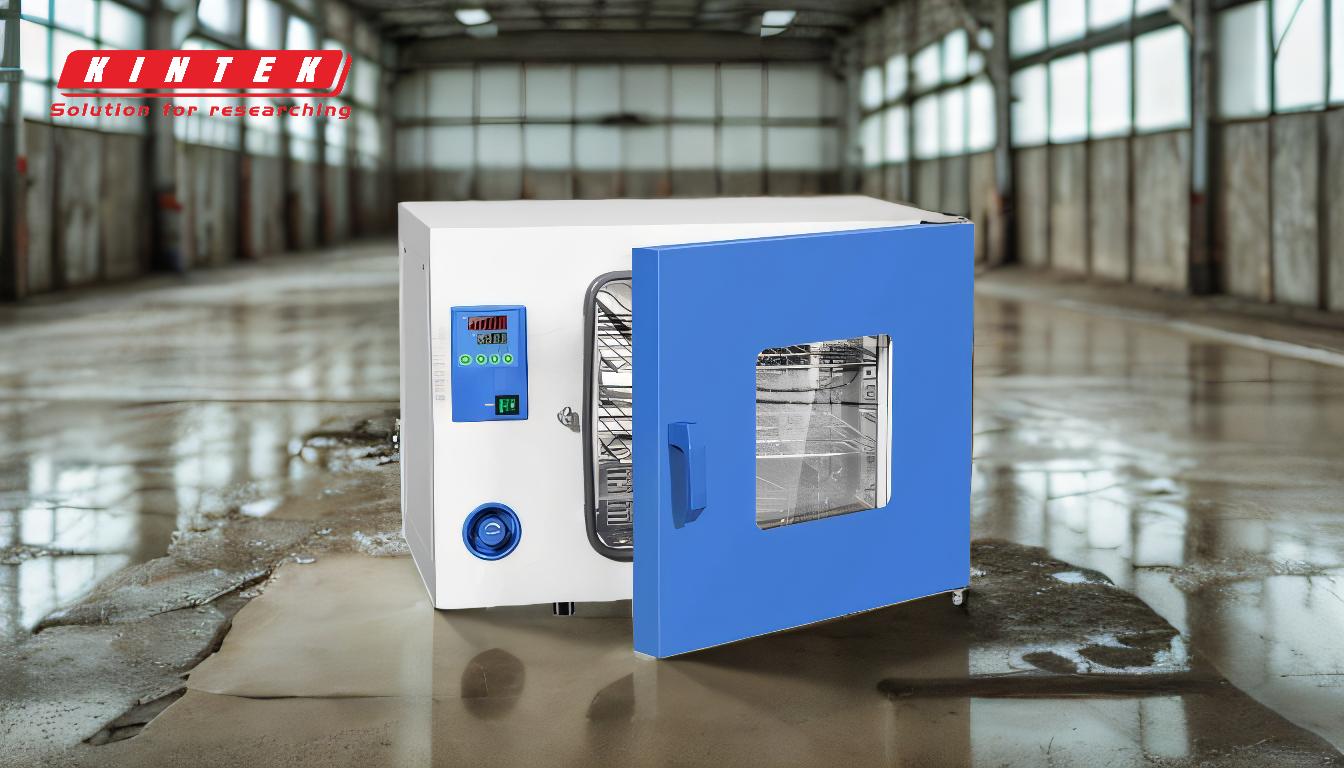
-
Overview of Vapour Deposition Methods:
- Vapour deposition methods are divided into two main categories: Physical Vapor Deposition (PVD) and Chemical Vapor Deposition (CVD).
- PVD involves the physical transformation of a solid material into a vapor, which then condenses to form nanoparticles. Techniques like sputtering, evaporation, and laser ablation fall under PVD.
- CVD involves chemical reactions in the vapor phase to produce nanoparticles. Precursor gases react at high temperatures to form the desired material, which is then deposited onto a substrate.
-
Physical Vapor Deposition (PVD):
- Sputtering: A target material is bombarded with high-energy ions, causing atoms to be ejected and deposited onto a substrate. This method is widely used for creating thin films and nanoparticles with high uniformity.
- Evaporation: The material is heated until it vaporizes, and the vapor condenses on a cooler substrate. This method is effective for producing high-purity nanoparticles.
- Laser Ablation: A high-energy laser is used to vaporize a target material, which then condenses to form nanoparticles. This technique allows for precise control over particle size and composition.
-
Chemical Vapor Deposition (CVD):
- Thermal CVD: Involves heating precursor gases to high temperatures, causing them to react and form nanoparticles on a substrate. This method is commonly used for producing high-quality, uniform coatings.
- Plasma-Enhanced CVD (PECVD): Uses plasma to lower the reaction temperature, making it suitable for depositing nanoparticles on temperature-sensitive substrates.
- Atomic Layer Deposition (ALD): A precise form of CVD where nanoparticles are deposited layer by layer, allowing for excellent control over thickness and composition.
-
Advantages of Vapour Deposition:
- High Purity: The process can produce nanoparticles with minimal impurities, making it ideal for applications requiring high-quality materials.
- Control Over Properties: Vapour deposition allows for precise control over the size, shape, and composition of nanoparticles, enabling the creation of materials with tailored properties.
- Versatility: The method can be used to deposit a wide range of materials, including metals, semiconductors, and ceramics.
-
Applications of Vapour-Deposited Nanoparticles:
- Electronics: Used in the fabrication of semiconductors, thin-film transistors, and other electronic components.
- Optics: Employed in the production of coatings for lenses, mirrors, and other optical devices.
- Catalysis: Nanoparticles synthesized via vapour deposition are used as catalysts in chemical reactions due to their high surface area and reactivity.
-
Challenges and Considerations:
- Cost: Vapour deposition equipment can be expensive, and the process may require high energy consumption.
- Complexity: The process often requires precise control over temperature, pressure, and gas flow rates, making it more complex than other synthesis methods.
- Scalability: While vapour deposition is excellent for producing high-quality nanoparticles, scaling up the process for industrial applications can be challenging.
In summary, vapour deposition is a powerful and versatile method for synthesizing nanoparticles, offering high purity and precise control over material properties. While it has some challenges, its advantages make it a preferred choice for many advanced applications in electronics, optics, and catalysis.
Summary Table:
Aspect | Details |
---|---|
Methods | Physical Vapor Deposition (PVD), Chemical Vapor Deposition (CVD) |
PVD Techniques | Sputtering, Evaporation, Laser Ablation |
CVD Techniques | Thermal CVD, Plasma-Enhanced CVD (PECVD), Atomic Layer Deposition (ALD) |
Advantages | High purity, precise control over size/shape/composition, versatile |
Applications | Electronics, optics, catalysis |
Challenges | High cost, complexity, scalability issues |
Discover how vapour deposition can revolutionize your nanoparticle synthesis—contact our experts today!