The VAR (Vacuum Arc Remelting) process is a critical method in steel and alloy production, particularly for achieving high purity and superior material properties. It involves remelting pre-formed alloy electrodes under a vacuum atmosphere, ensuring controlled solidification in a water-cooled copper crucible. This process is widely used for stainless steel, nickel-based, and titanium-based alloys, producing materials with exceptional homogeneity, soundness, and metallurgical properties. The VAR process is energy-efficient, reproducible, and capable of delivering ingots with uniform chemical composition and crystalline structure, making it indispensable in high-performance applications.
Key Points Explained:
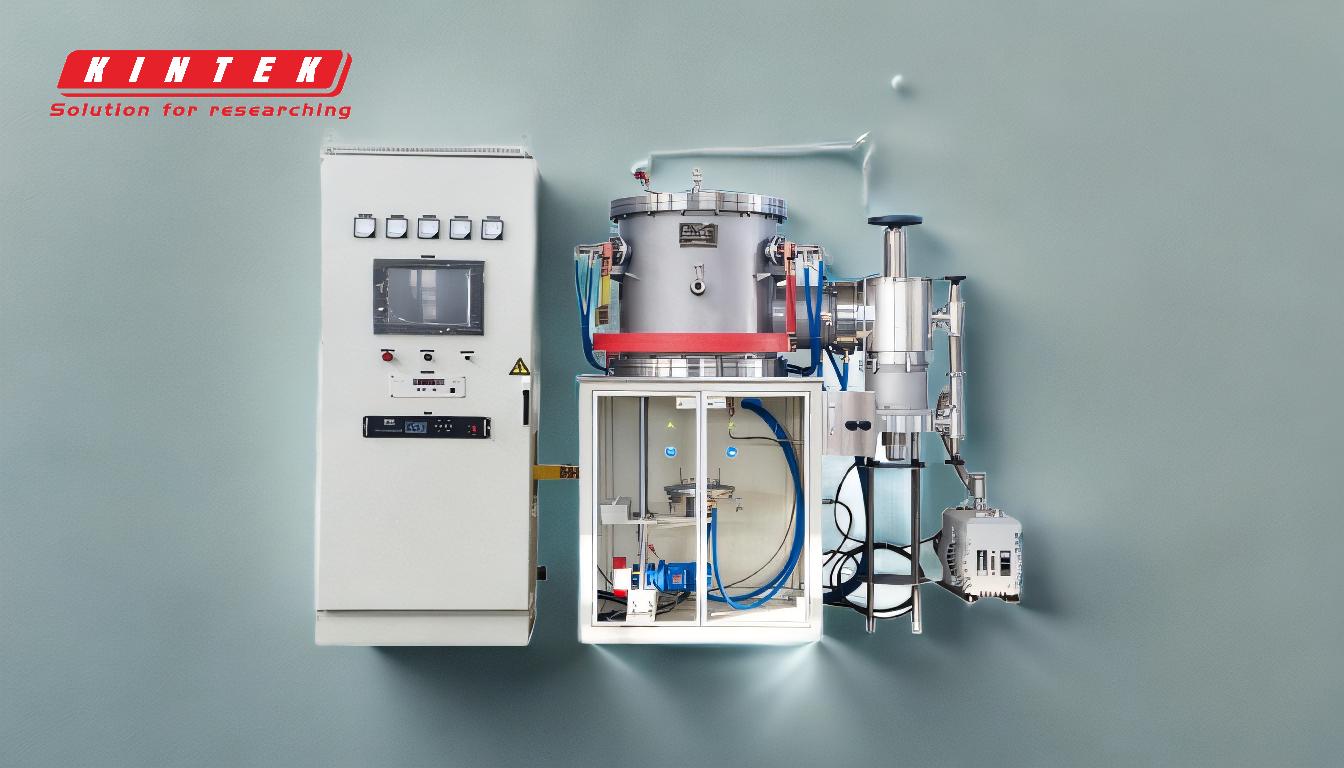
-
Definition and Purpose of VAR:
- VAR stands for Vacuum Arc Remelting, a specialized production method used to refine and purify alloys.
- The primary goal is to achieve high-purity materials with superior metallurgical properties, such as homogeneity, soundness, and controlled chemical composition.
- It is particularly effective for stainless steel, nickel-based, and titanium-based alloys, which are often used in demanding applications like aerospace, medical devices, and energy systems.
-
Process Overview:
- The VAR process begins with a pre-formed alloy electrode, typically created using vacuum induction melting (VIM) or ladle refining (airmelt).
- The electrode is placed in a water-cooled copper crucible within a vacuum chamber.
- A high-current electric arc is struck between the electrode and the crucible, causing the electrode to melt.
- The molten metal solidifies in a controlled manner, ensuring uniform cooling and minimizing defects.
-
Key Components and Their Roles:
- Vacuum Atmosphere: The vacuum environment (0.001–0.1 mmHg or 0.1–13.3 Pa) prevents contamination from atmospheric gases, ensuring high purity.
- Water-Cooled Copper Crucible: Facilitates controlled solidification, resulting in a homogeneous and defect-free ingot.
- Electric Arc: Provides the heat necessary to melt the electrode, with precise control over the melting rate and solidification process.
-
Advantages of VAR:
- High Purity: The vacuum environment eliminates impurities and gases, leading to cleaner materials.
- Controlled Solidification: Ensures uniform microstructure and minimizes defects like porosity and segregation.
- Reproducibility: The process is highly consistent, making it ideal for producing high-quality ingots in large quantities.
- Energy Efficiency: VAR is known for its low power consumption and high melting speed, making it cost-effective.
-
Applications of VAR:
- Aerospace: VAR-processed materials are used in critical components like turbine blades and structural parts due to their high strength and reliability.
- Medical Devices: Titanium alloys produced via VAR are used in implants and surgical instruments because of their biocompatibility and mechanical properties.
- Energy Sector: Nickel-based superalloys made using VAR are essential for high-temperature applications in power generation and oil refining.
-
Comparison with Other Melting Methods:
- Vacuum Induction Melting (VIM): While VIM is used to create the initial electrode, it does not offer the same level of control over solidification as VAR.
- Electroslag Remelting (ESR): ESR is another refining method, but it operates under a slag layer rather than a vacuum, making it less effective for removing certain impurities.
- Air Melting: Traditional air melting methods are prone to contamination and lack the precision of VAR, making them unsuitable for high-performance applications.
-
Technical Considerations for Equipment Purchasers:
- Vacuum System: Ensure the system can achieve and maintain the required vacuum levels (0.001–0.1 mmHg).
- Cooling System: The water-cooled crucible must have efficient heat removal capabilities to ensure controlled solidification.
- Power Supply: A stable and high-current power supply is essential for maintaining the electric arc.
- Automation and Control: Advanced control systems are necessary to monitor and adjust parameters like melting rate, temperature, and vacuum levels.
-
Future Trends and Innovations:
- Improved Automation: Enhanced control systems and AI-driven monitoring could further optimize the VAR process.
- Material Advancements: Research into new alloy compositions may expand the range of materials suitable for VAR processing.
- Sustainability: Efforts to reduce energy consumption and waste in the VAR process are likely to gain importance.
By understanding the VAR process and its advantages, equipment and consumable purchasers can make informed decisions to meet their specific needs, ensuring the production of high-quality materials for critical applications.
Summary Table:
Aspect | Details |
---|---|
Purpose | Refines and purifies alloys for high-purity materials with superior properties. |
Key Components | Vacuum atmosphere, water-cooled copper crucible, electric arc. |
Advantages | High purity, controlled solidification, reproducibility, energy efficiency. |
Applications | Aerospace, medical devices, energy systems. |
Comparison with Others | Outperforms VIM, ESR, and air melting in purity and control. |
Future Trends | Improved automation, new alloy research, sustainability efforts. |
Discover how the VAR process can enhance your material production—contact our experts today for tailored solutions!