The voltage of a vacuum arc, particularly in the context of a vacuum arc furnace, varies depending on the specific conditions and materials involved. Generally, the voltage of a vacuum arc is relatively low, typically in the range of 10 to 50 volts, but it can vary based on factors such as the type of material being processed, the distance between the electrodes, and the current density. The vacuum environment plays a crucial role in stabilizing the arc and preventing contamination, which is why maintaining a clean environment is essential for optimal operation.
Key Points Explained:
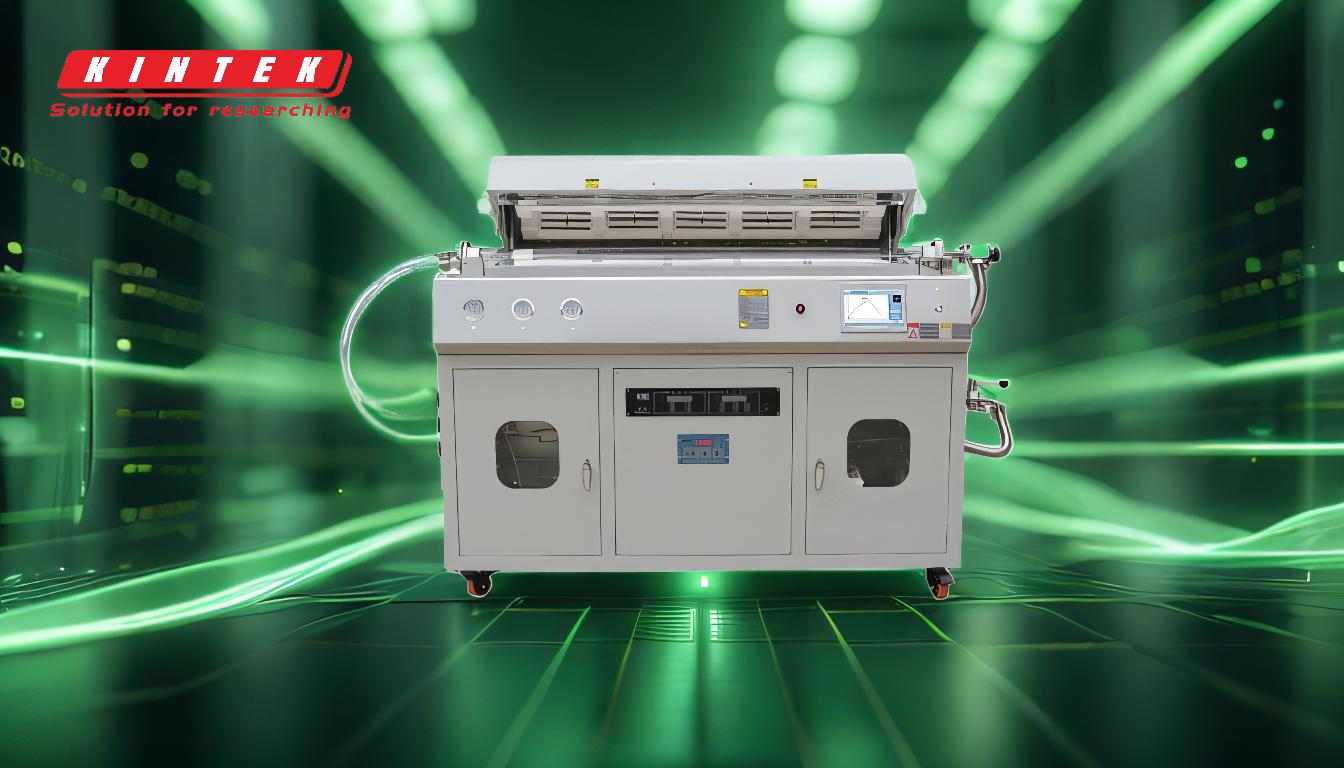
-
Voltage Range of a Vacuum Arc:
- The voltage of a vacuum arc typically falls between 10 to 50 volts. This range is influenced by the specific conditions of the arc, such as the material being processed and the distance between the electrodes.
- In a vacuum arc furnace, the low voltage is sufficient to maintain a stable arc due to the absence of air or other gases that could otherwise disrupt the arc.
-
Factors Affecting Arc Voltage:
- Material Type: Different materials have different electrical properties, which can affect the voltage required to sustain the arc.
- Electrode Distance: The distance between the electrodes (anode and cathode) in the vacuum arc furnace can influence the voltage. A larger distance may require a higher voltage to maintain the arc.
- Current Density: The current density, or the amount of current per unit area, can also affect the voltage. Higher current densities may require higher voltages to sustain the arc.
-
Importance of a Clean Environment:
- The environment for operating a vacuum furnace must be clean to prevent contamination. Operators must wear clean garments and white gloves to handle vacuum-treated pieces, as gloveless hands can leave imprints that create rust stains.
- Pieces must be packed in plastic envelopes and sealed after filling with nitrogen to maintain a contamination-free environment. This cleanliness is crucial for the stability and efficiency of the vacuum arc.
-
Components of a Vacuum Furnace:
- High-Speed Diffusion Pump: This component helps maintain the vacuum by removing gases from the chamber, ensuring a stable environment for the arc.
- Vacuum Chamber with High-Temperature Hot Zone: The chamber provides the space where the vacuum arc is generated and maintained. The high-temperature hot zone is essential for processing materials at elevated temperatures.
- Control Cabinet: This component houses the controls for managing the furnace's operations, including the voltage and current settings for the arc.
-
Role of Vacuum in Arc Stability:
- The vacuum environment is critical for stabilizing the arc. In a vacuum, there are no gases to ionize, which helps maintain a consistent arc voltage and prevents fluctuations that could occur in a gaseous environment.
- The absence of air or other gases also reduces the risk of contamination, which is essential for high-purity applications such as metal refining or semiconductor manufacturing.
-
Applications of Vacuum Arc Furnaces:
- Vacuum arc furnaces are used in various applications, including the refining of metals, production of high-purity materials, and manufacturing of components for the aerospace and electronics industries.
- The low voltage and stable arc provided by the vacuum environment make these furnaces ideal for processes that require precise control over the material properties and purity.
In summary, the voltage of a vacuum arc in a vacuum arc furnace typically ranges from 10 to 50 volts, influenced by factors such as material type, electrode distance, and current density. Maintaining a clean environment and the proper functioning of the furnace components are essential for the stability and efficiency of the arc. The vacuum environment plays a crucial role in stabilizing the arc and preventing contamination, making it ideal for high-purity applications.
Summary Table:
Aspect | Details |
---|---|
Voltage Range | 10 to 50 volts |
Key Factors | Material type, electrode distance, current density |
Importance of Cleanliness | Prevents contamination; requires clean garments, gloves, and nitrogen packing |
Components | High-speed diffusion pump, vacuum chamber, control cabinet |
Applications | Metal refining, high-purity materials, aerospace, and electronics industries |
Interested in optimizing your vacuum arc furnace operations? Contact us today for expert guidance!