An electric muffle furnace operates as a highly efficient and controlled heating device, primarily used in laboratories, industrial settings, and research facilities. It works by utilizing electric heating elements to generate high temperatures within an insulated chamber, ensuring uniform heat distribution and preventing contamination of the materials being heated. The furnace's design includes a separate heating chamber and combustion chamber, which isolates the heating process from combustion byproducts. This allows for precise temperature control and makes it ideal for applications like heat treatment, material analysis, and element detection.
Key Points Explained:
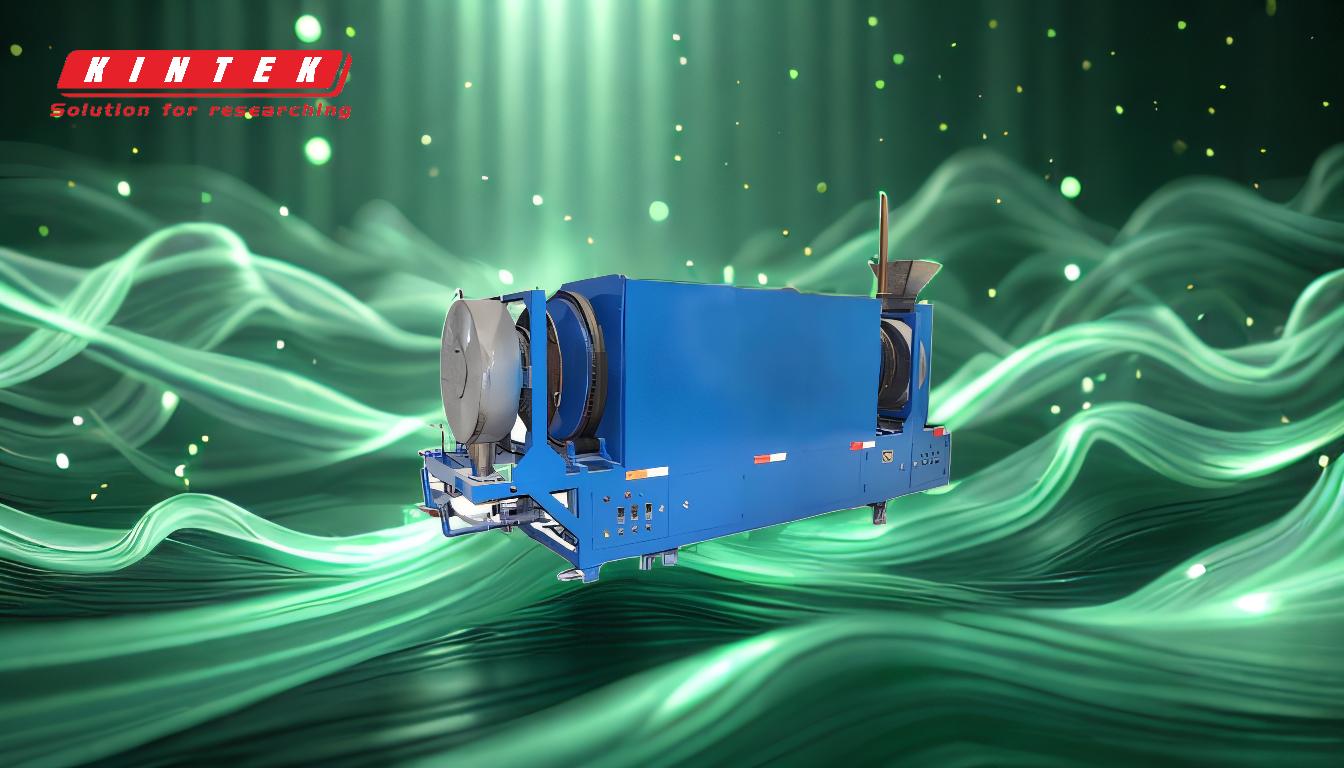
-
Basic Structure and Components:
- An electric muffle furnace consists of a heating coil surrounded by insulated materials, typically ceramic, to withstand high temperatures.
- The furnace includes two main chambers: the heating chamber (where materials are placed) and the combustion chamber (where heat is generated).
- Modern designs use high-temperature electric heating elements, which eliminate the need for fuel combustion, ensuring cleaner and more controlled heating.
-
Working Principle:
- The furnace generates heat through electric resistance heating, where electric current passes through the heating elements, causing them to heat up.
- The heat is then transferred to the heating chamber, where the material is placed. The chamber is airtight, preventing contamination from external sources.
- Unlike traditional furnaces, the muffle furnace isolates the heating process from combustion byproducts, ensuring a clean environment for sensitive applications.
-
Temperature Control and Uniformity:
- Electric muffle furnaces are designed to achieve precise temperature control, often ranging up to 1400°C or higher.
- The insulated ceramic chamber ensures uniform heat distribution, which is critical for processes like annealing, hardening, and tempering.
- Advanced models include digital controllers and thermocouples for real-time temperature monitoring and adjustments.
-
Applications:
- Muffle furnaces are widely used in laboratories for material analysis, such as detecting elements in coal or other substances.
- They are also employed in industrial settings for small-scale heat treatment processes, including hardening, annealing, and tempering of metals.
- Their ability to provide a contamination-free environment makes them suitable for scientific research and high-precision manufacturing.
-
Advantages Over Other Furnace Types:
- Compared to fuel-based furnaces, electric muffle furnaces offer cleaner operation, as they do not produce combustion byproducts.
- They provide better temperature control and uniformity, which is essential for consistent results in heat treatment and material analysis.
- The absence of direct combustion also reduces maintenance requirements and extends the lifespan of the furnace.
-
Comparison with Electric Arc Furnaces:
- Unlike electric arc furnaces, which use an electric arc to generate heat directly in contact with the material, muffle furnaces rely on indirect heating through electric elements.
- Electric arc furnaces are typically used for melting metals, while muffle furnaces are better suited for controlled heating and material processing.
- Muffle furnaces are more suitable for applications requiring a contamination-free environment and precise temperature control.
By understanding the working principle and key features of an electric muffle furnace, users can make informed decisions about its suitability for specific applications, ensuring optimal performance and results.
Summary Table:
Aspect | Details |
---|---|
Heating Method | Electric resistance heating via high-temperature elements |
Chambers | Heating chamber (material placement) and combustion chamber (heat generation) |
Temperature Range | Up to 1400°C or higher |
Heat Distribution | Uniform heating ensured by insulated ceramic chamber |
Applications | Material analysis, heat treatment, annealing, hardening, and tempering |
Advantages | Clean operation, precise temperature control, low maintenance |
Comparison | Superior to fuel-based furnaces and electric arc furnaces for controlled heating |
Looking for a reliable electric muffle furnace? Contact our experts today to find the perfect solution for your needs!