Thermal debinding is a critical step in the manufacturing process of metal or ceramic parts produced through powder injection molding (PIM) or similar techniques. It involves the controlled removal of a binder material, which is initially mixed with the metal or ceramic powder to facilitate shaping during the molding process. The binder acts as a temporary support structure, holding the powder particles together. Thermal debinding is achieved by heating the molded part to specific temperatures, causing the binder to decompose, evaporate, or burn off, leaving behind a porous structure of the metal or ceramic powder. This step is essential to prepare the part for the subsequent sintering process, where the powder particles are fused together to achieve the final density and mechanical properties.
Key Points Explained:
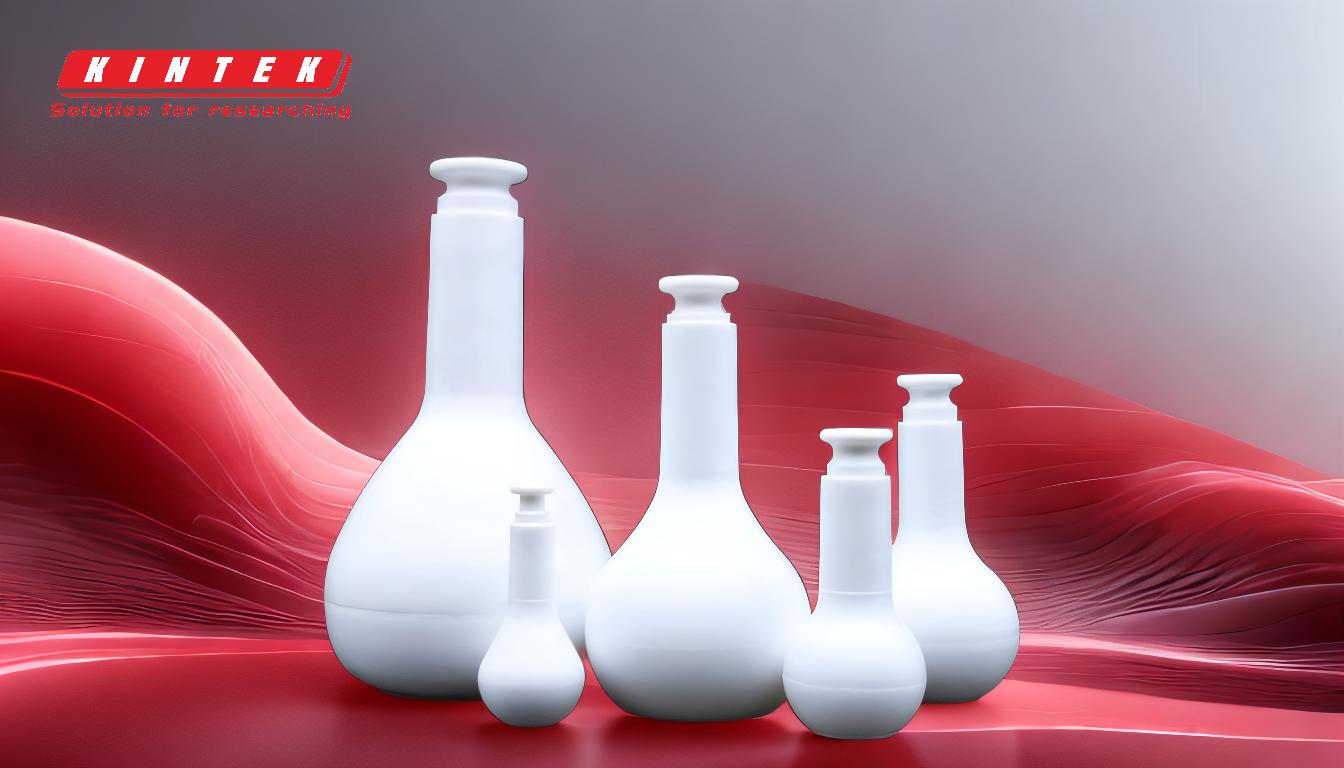
-
Purpose of Thermal Debinding:
- Thermal debinding is used to remove the binder material from the molded part, which is necessary to prepare the part for sintering.
- The binder, typically a polymer or wax, is added to the metal or ceramic powder to improve flowability and enable shaping during the molding process.
- Without debinding, the binder would interfere with the sintering process, leading to defects or incomplete densification.
-
Process Overview:
- Thermal debinding involves heating the molded part in a controlled environment, such as a muffle furnace, to gradually remove the binder.
- The temperature is carefully controlled to avoid rapid decomposition, which could cause cracking or distortion of the part.
- The process is often carried out in multiple stages, with each stage targeting a specific component of the binder system.
-
Types of Binders:
- Single-Component Binders: These are simpler to remove but may require higher temperatures, which can increase the risk of part deformation.
- Multi-Component Binders: These are more complex but allow for staged removal, reducing the risk of defects. For example, a low-temperature component may evaporate first, followed by a high-temperature component that decomposes at a higher temperature.
-
Debinding Mechanisms:
- Evaporation: Some binders are designed to evaporate at specific temperatures, leaving no residue.
- Thermal Decomposition: Other binders break down into gaseous byproducts when heated, which are then removed from the furnace.
- Oxidation: In some cases, binders are burned off in the presence of oxygen, although this requires careful control to avoid damaging the part.
-
Challenges in Thermal Debinding:
- Part Integrity: Rapid or uneven heating can cause cracking, warping, or other defects in the part.
- Binder Residue: Incomplete removal of the binder can lead to contamination during sintering, affecting the final properties of the part.
- Process Control: Precise control of temperature, heating rate, and atmosphere is crucial to ensure successful debinding.
-
Equipment Used:
- Muffle Furnaces: These are commonly used for thermal debinding due to their ability to provide a controlled atmosphere and uniform heating.
- Vacuum Furnaces: These are used for debinding in an oxygen-free environment, which is necessary for certain materials that are sensitive to oxidation.
- Continuous Furnaces: These are used in high-volume production, allowing for a continuous flow of parts through the debinding process.
-
Post-Debinding Considerations:
- After debinding, the part is typically in a fragile, porous state and must be handled carefully to avoid damage.
- The part is then ready for sintering, where it is heated to a temperature just below its melting point to fuse the powder particles together, achieving the desired density and strength.
-
Applications:
- Thermal debinding is widely used in the production of complex metal or ceramic parts, such as gears, medical implants, and aerospace components.
- It is particularly valuable for parts that require high precision and intricate geometries, which are difficult to achieve through traditional manufacturing methods.
In summary, thermal debinding is a vital step in the powder injection molding process, enabling the production of high-quality metal and ceramic parts. It requires careful control of temperature, atmosphere, and heating rates to ensure the successful removal of the binder without compromising the integrity of the part. The process is supported by specialized equipment, such as muffle furnaces, and is essential for achieving the desired properties in the final sintered product.
Summary Table:
Aspect | Details |
---|---|
Purpose | Removes binder material to prepare parts for sintering. |
Process | Controlled heating in environments like muffle or vacuum furnaces. |
Binder Types | Single-component (simpler) or multi-component (staged removal). |
Mechanisms | Evaporation, thermal decomposition, or oxidation. |
Challenges | Part integrity, binder residue, and precise process control. |
Equipment | Muffle furnaces, vacuum furnaces, or continuous furnaces. |
Applications | Used in producing gears, medical implants, and aerospace components. |
Need expert advice on thermal debinding for your manufacturing process? Contact us today!