Refractory lining materials in kilns are selected based on the specific requirements of the process, including temperature resistance, thermal conductivity, wear resistance, and chemical compatibility. Commonly used materials include magnesia spinel bricks, high alumina bricks with silicon carbide, silica-mullite bricks, and magnesite bricks. Additionally, advanced materials like high-purity alumina fiber, vacuum-formed fiber, and lightweight alumina ceramic fiber are used for their excellent thermal insulation and rapid heat resistance properties. The choice of material depends on factors such as the kiln type (e.g., cement kiln, muffle furnace), process conditions, and desired performance characteristics like low heat loss and energy efficiency.
Key Points Explained:
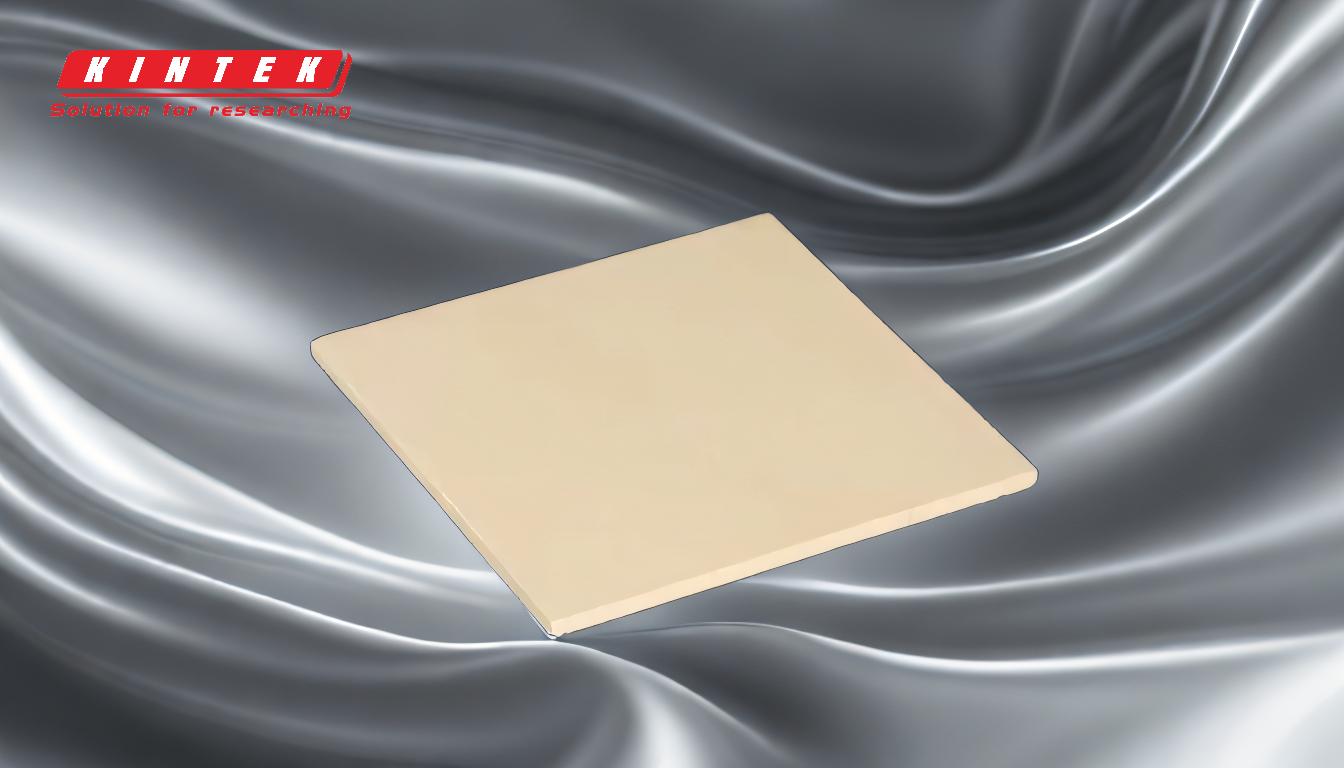
-
Magnesia Spinel Bricks:
- Widely used in cement kiln linings due to their excellent thermal stability and resistance to chemical corrosion.
- However, they have higher thermal conductivity compared to other materials like high alumina bricks with silicon carbide.
-
High Alumina Bricks with Silicon Carbide:
- Known for their lower thermal conductivity and high strength, making them suitable for high-temperature applications.
- Often used as an alternative to magnesia spinel bricks in cement kilns.
-
Silica-Mullite Bricks:
- Considered one of the best options for large-scale cement rotary kilns due to their superior thermal shock resistance and durability.
- Ideal for environments with fluctuating temperatures.
-
Magnesite Bricks:
- Commonly used in cement kilns for their high refractoriness and resistance to basic slags.
- Suitable for processes involving high temperatures and abrasive materials.
-
High-Purity Alumina Fiber and Vacuum-Formed Fiber:
- Provide high service temperatures, rapid heat and cold resistance, and excellent thermal insulation.
- Used in furnace linings for their lightweight properties and ability to minimize heat loss.
-
Lightweight Alumina Ceramic Fiber and Insulation Boards:
- Multi-layer insulation designs using these materials ensure low heat loss and energy efficiency.
- Free from asbestos, making them environmentally friendly and safe for use.
-
Material Selection Based on Process Requirements:
- The thickness, physical properties, and chemical composition of refractory materials are tailored to the specific kiln process.
- For example, low-iron alumina or magnesium-spinel bricks are used in iron ore reduction kilns, while magnesite bricks are preferred in cement kilns.
-
Castable vs. Brick Refractories:
- Castable Refractories: Poured into place, easier to install but less wear-resistant.
- Brick Refractories: Laid manually, more wear-resistant and suitable for abrasive materials, but labor-intensive to install.
-
Kiln Construction Materials:
- Direct-Fired Kilns: Typically made from carbon steel.
- Indirect-Fired Kilns: Constructed from heat-resistant alloys to withstand higher temperatures.
By understanding these key points, a purchaser can make informed decisions about the most suitable refractory lining materials for their specific kiln applications, ensuring optimal performance and longevity.
Summary Table:
Material Type | Key Features | Common Applications |
---|---|---|
Magnesia Spinel Bricks | High thermal stability, chemical corrosion resistance | Cement kilns |
High Alumina Bricks with SiC | Low thermal conductivity, high strength | High-temperature applications |
Silica-Mullite Bricks | Superior thermal shock resistance, durability | Large-scale cement rotary kilns |
Magnesite Bricks | High refractoriness, resistance to basic slags | Cement kilns, abrasive material processes |
High-Purity Alumina Fiber | Excellent thermal insulation, rapid heat resistance | Furnace linings |
Lightweight Alumina Ceramic Fiber | Low heat loss, energy efficiency, asbestos-free | Multi-layer insulation designs |
Need help selecting the right refractory lining for your kiln? Contact our experts today for tailored solutions!