Measuring and monitoring high temperatures in heat treating processes is critical for ensuring the quality and consistency of the treated materials. The two primary methods for temperature measurement in industrial furnace tubes are indirect measurement using infrared thermometers and direct measurement using temperature elements in contact with the tubes. Each method has its advantages and limitations, and the choice depends on factors such as accuracy requirements, furnace design, and operational conditions. Below, we explore these methods in detail, along with their applications and considerations.
Key Points Explained:
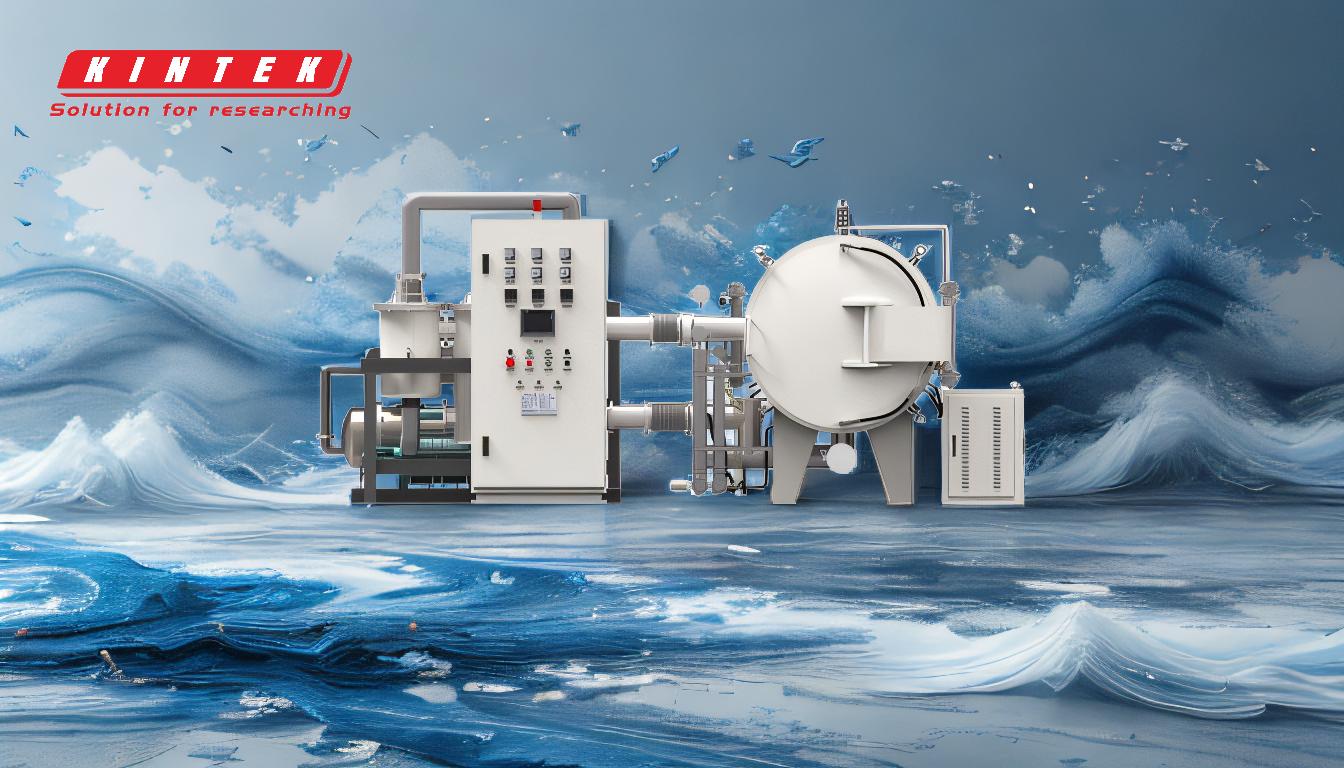
-
Indirect Temperature Measurement Using Infrared Thermometers
- How It Works: Infrared thermometers measure the thermal radiation emitted by the furnace tubes without physical contact. This method requires a clear line of sight to the tubes, often achieved through a peek window in the furnace.
-
Advantages:
- Non-contact measurement avoids interference with the furnace environment.
- Suitable for high-temperature applications where direct contact is impractical.
- Provides real-time temperature readings.
-
Limitations:
- Accuracy depends on the emissivity of the tube material, which can vary.
- Requires a clear line of sight, which may be obstructed by furnace components or process conditions.
- Calibration is necessary to account for environmental factors like dust or gas interference.
- Applications: Ideal for monitoring temperatures in furnaces with limited access or where direct contact is not feasible.
-
Direct Temperature Measurement Using Temperature Elements
- How It Works: Temperature elements, such as thermocouples or resistance temperature detectors (RTDs), are placed in direct contact with the furnace tubes to measure their temperature.
-
Advantages:
- High accuracy and reliability due to direct contact with the tubes.
- Suitable for continuous monitoring in harsh environments.
- Can be integrated into automated control systems for precise temperature regulation.
-
Limitations:
- Physical contact may introduce wear and tear on the elements, requiring periodic maintenance or replacement.
- Installation can be complex, especially in high-temperature or corrosive environments.
- May interfere with the furnace's thermal dynamics if not properly designed.
- Applications: Commonly used in processes requiring precise temperature control, such as heat treating, annealing, and tempering.
-
Factors to Consider When Choosing a Measurement Method
- Accuracy Requirements: Direct methods generally offer higher accuracy, while indirect methods are more suitable for approximate measurements.
- Furnace Design: The availability of peek windows or access points may determine the feasibility of indirect measurement.
- Operational Conditions: High-temperature, corrosive, or dusty environments may favor one method over the other.
- Cost and Maintenance: Indirect methods may have lower initial costs but require calibration, while direct methods may involve higher maintenance due to wear and tear.
-
Emerging Technologies and Trends
- Advanced Infrared Sensors: Improved infrared sensors with enhanced emissivity correction and higher resolution are becoming more common.
- Wireless Monitoring Systems: Wireless temperature sensors are being adopted for easier installation and reduced maintenance.
- Integration with IoT: Both direct and indirect measurement methods are increasingly integrated into IoT platforms for real-time data analysis and predictive maintenance.
By understanding the strengths and limitations of each method, equipment and consumable purchasers can make informed decisions to ensure accurate and reliable temperature monitoring in heat treating processes. The choice of method should align with the specific requirements of the application, balancing accuracy, cost, and operational feasibility.
Summary Table:
Method | Advantages | Limitations | Applications |
---|---|---|---|
Infrared Thermometers | Non-contact, real-time readings, suitable for high-temp environments | Accuracy depends on emissivity, requires clear line of sight, needs calibration | Monitoring in limited-access or non-contact scenarios |
Temperature Elements | High accuracy, continuous monitoring, integrates with automated control systems | Wear and tear, complex installation, may interfere with thermal dynamics | Precise control in heat treating, annealing, and tempering processes |
Need help choosing the right temperature measurement method for your furnace? Contact our experts today for personalized advice!