Vacuum casting is a manufacturing process primarily used for producing high-quality, detailed prototypes and small-batch production parts. It involves using a vacuum to draw liquid material, such as polyurethane resin, into a silicone mold, ensuring precise replication of intricate details. This method is widely adopted in industries like product design, automotive, aerospace, and medical devices for creating functional prototypes, concept models, and end-use parts. It is cost-effective for low-volume production and allows for the use of materials that mimic the properties of final production materials. Below, the key aspects of vacuum casting are explained in detail.
Key Points Explained:
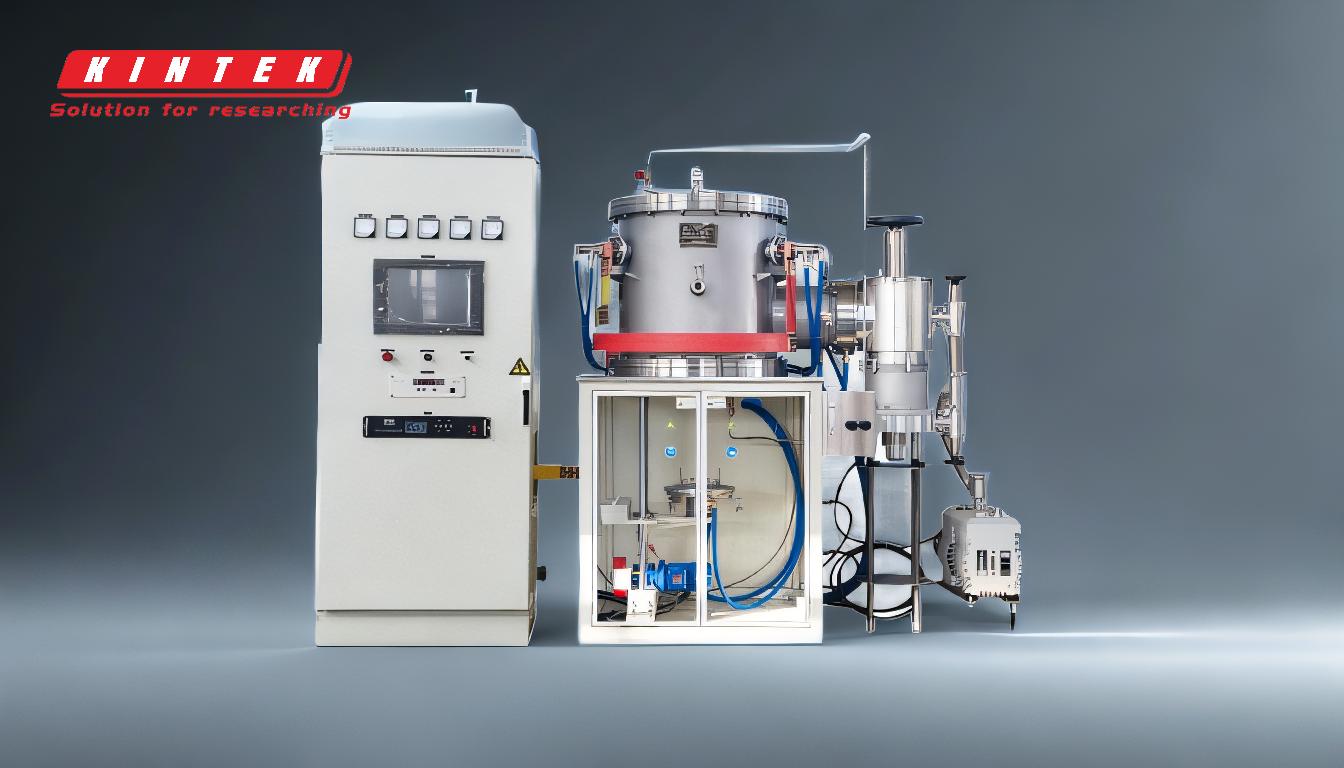
-
Definition and Process of Vacuum Casting
- Vacuum casting is a technique where liquid material, typically polyurethane resin, is poured into a silicone mold under vacuum conditions.
- The vacuum removes air bubbles, ensuring a smooth and accurate replication of the mold's details.
- The process is ideal for creating parts with complex geometries and fine surface finishes.
-
Applications in Various Industries
- Product Design and Prototyping: Used to create functional prototypes for testing and validation before mass production.
- Automotive: Produces lightweight, durable components for testing and low-volume production.
- Aerospace: Manufactures parts with high precision and material properties similar to final products.
- Medical Devices: Enables the production of biocompatible and sterilizable components for testing and small-scale use.
- Consumer Goods: Ideal for creating concept models and end-use parts for electronics, appliances, and other products.
-
Advantages of Vacuum Casting
- Cost-Effectiveness: More affordable than traditional manufacturing methods like injection molding for small batches.
- Material Versatility: Allows the use of resins that mimic the properties of plastics, rubber, and even metals.
- High Detail and Accuracy: Capable of reproducing intricate details and fine textures.
- Rapid Turnaround: Faster production cycles compared to other methods, making it suitable for tight deadlines.
-
Limitations of Vacuum Casting
- Mold Durability: Silicone molds have a limited lifespan, typically producing 20-25 parts before degrading.
- Material Constraints: While versatile, the range of materials is still limited compared to injection molding.
- Volume Restrictions: Not suitable for high-volume production due to mold wear and slower cycle times.
-
Comparison with Other Manufacturing Methods
- Injection Molding: Vacuum casting is more cost-effective for small batches but lacks the scalability and material diversity of injection molding.
- 3D Printing: Offers faster prototyping but may not achieve the same level of surface finish and material properties as vacuum casting.
- CNC Machining: Provides high precision but is often more expensive and less efficient for complex geometries.
-
Future Trends and Innovations
- Advanced Materials: Development of new resins with enhanced properties, such as higher temperature resistance or biocompatibility.
- Automation: Integration of automated systems to improve efficiency and reduce labor costs.
- Sustainability: Use of eco-friendly materials and processes to minimize environmental impact.
In summary, vacuum casting is a versatile and cost-effective solution for producing high-quality prototypes and small-batch parts across various industries. Its ability to replicate intricate details and use a wide range of materials makes it a valuable tool for product development and low-volume manufacturing. However, its limitations in mold durability and material options highlight the need for careful consideration when choosing this method for specific applications.
Summary Table:
Aspect | Details |
---|---|
Process | Liquid material (e.g., polyurethane resin) poured into silicone molds under vacuum. |
Applications | Product design, automotive, aerospace, medical devices, consumer goods. |
Advantages | Cost-effective, material versatility, high detail, rapid turnaround. |
Limitations | Limited mold durability, material constraints, not suitable for high volume. |
Comparison | More cost-effective than injection molding for small batches; better surface finish than 3D printing. |
Future Trends | Advanced materials, automation, sustainability. |
Discover how vacuum casting can elevate your prototyping process—contact us today for expert guidance!