Vacuum sputtering is a physical vapor deposition (PVD) technique used to deposit thin films of material onto a substrate. This process involves bombarding a target material with high-energy particles or ions in a vacuum environment, causing atoms or molecules to be ejected from the target and deposited onto the substrate. The vacuum environment minimizes contamination and ensures a clean deposition process. This method is widely used in industries such as electronics, optics, and coatings due to its precision and ability to produce high-quality thin films.
Key Points Explained:
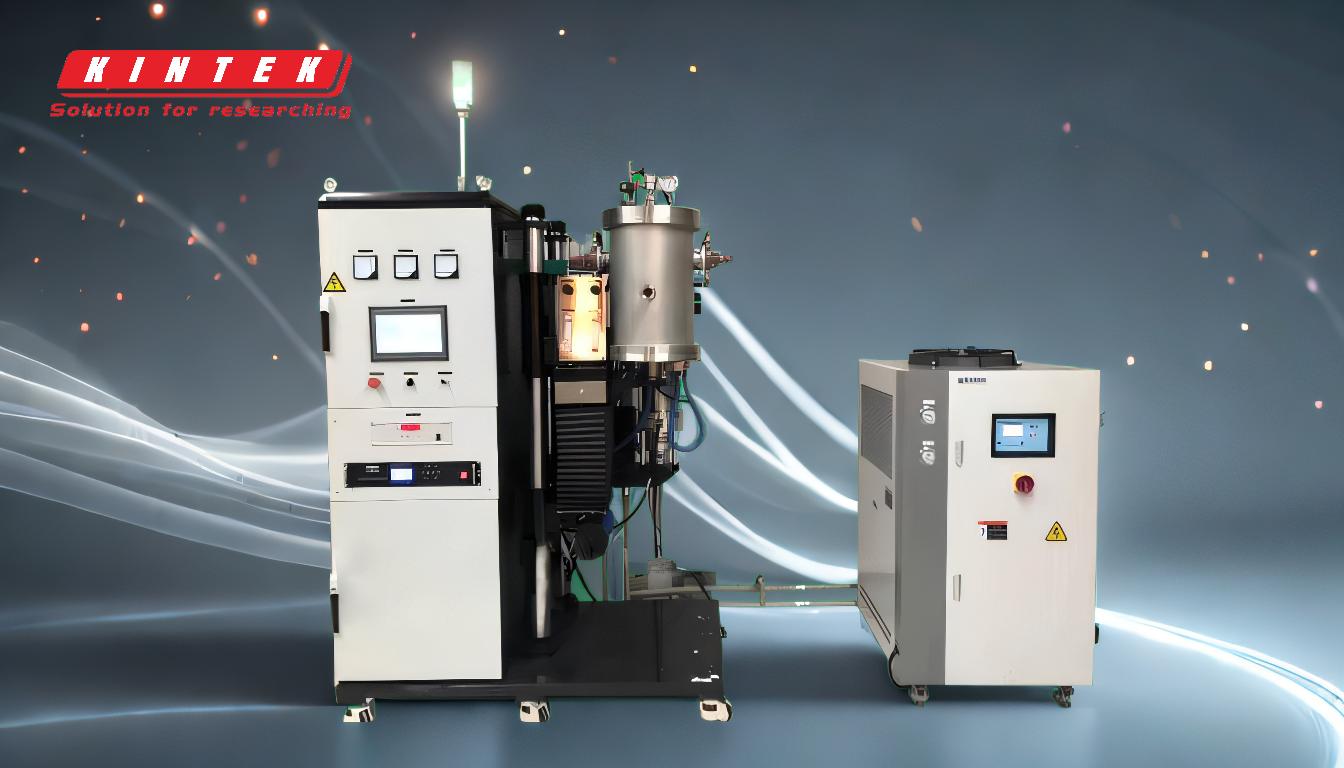
-
Vacuum Environment:
- A vacuum environment is crucial for the sputtering process. It ensures that the deposition occurs in a controlled atmosphere, free from contaminants like oxygen, water vapor, or other gases that could interfere with the film's quality.
- In the context of vacuum sputtering, a vacuum refers to any pressure below normal atmospheric pressure (14.6 psia or 760 torr). While achieving an absolute vacuum is impossible, the goal is to create a low-pressure environment that minimizes the presence of unwanted particles or gases.
-
Sputtering Mechanism:
- Sputtering involves bombarding a target material (the source of the film) with high-energy particles or ions, typically from a plasma. This bombardment ejects atoms or molecules from the target, which then travel through the vacuum and deposit onto the substrate.
- The process is highly controllable, allowing for precise thickness and composition of the deposited film.
-
Applications of Vacuum Sputtering:
- Electronics: Used to deposit thin films for semiconductors, integrated circuits, and displays.
- Optics: Applied in the production of anti-reflective coatings, mirrors, and optical filters.
- Coatings: Utilized for wear-resistant, decorative, or functional coatings on various materials.
-
Advantages of Vacuum Sputtering:
- High Precision: Enables the deposition of ultra-thin films with precise control over thickness and composition.
- Clean Process: The vacuum environment minimizes contamination, resulting in high-quality films.
- Versatility: Can be used with a wide range of materials, including metals, ceramics, and polymers.
-
Connection to Vacuum Furnaces:
- While vacuum sputtering is primarily a deposition technique, it shares similarities with processes like debinding in vacuum furnaces. Both processes rely on a vacuum environment to achieve specific material properties, whether it's removing binders or depositing thin films.
- Vacuum furnaces are also used in heat treatment processes for materials like steels, where the vacuum environment ensures minimal deformation and high-quality results.
-
Challenges and Considerations:
- Achieving and maintaining a high-quality vacuum can be technically challenging and costly.
- The sputtering process requires careful control of parameters such as pressure, temperature, and ion energy to ensure consistent film quality.
By understanding these key points, a purchaser of equipment or consumables can make informed decisions about the use of vacuum sputtering in their specific applications, ensuring optimal results and cost-effectiveness.
Summary Table:
Aspect | Details |
---|---|
Vacuum Environment | Ensures contamination-free deposition; operates below atmospheric pressure. |
Sputtering Mechanism | High-energy particles eject target atoms, depositing them onto a substrate. |
Applications | Electronics, optics, and coatings (e.g., semiconductors, mirrors, coatings). |
Advantages | High precision, clean process, and versatility with various materials. |
Challenges | Requires controlled parameters; achieving high-quality vacuum is costly. |
Ready to enhance your thin film processes? Contact us today to learn more about vacuum sputtering solutions!