Vacuum casting is a manufacturing process used to create high-quality replicas of original parts using silicone molds. The process involves pouring liquid resin into a silicone mold under vacuum conditions to eliminate air bubbles and ensure a high-quality finish. The mold itself is held together by a combination of mechanical and physical forces, primarily due to the design of the mold, the properties of the silicone material, and the vacuum pressure applied during the process. The silicone mold is flexible yet durable, allowing it to maintain its shape and integrity while being subjected to vacuum pressure. Additionally, the mold is often placed in a rigid frame or casing to provide structural support during the casting process. This ensures that the mold remains intact and the final product retains the desired dimensions and details.
Key Points Explained:
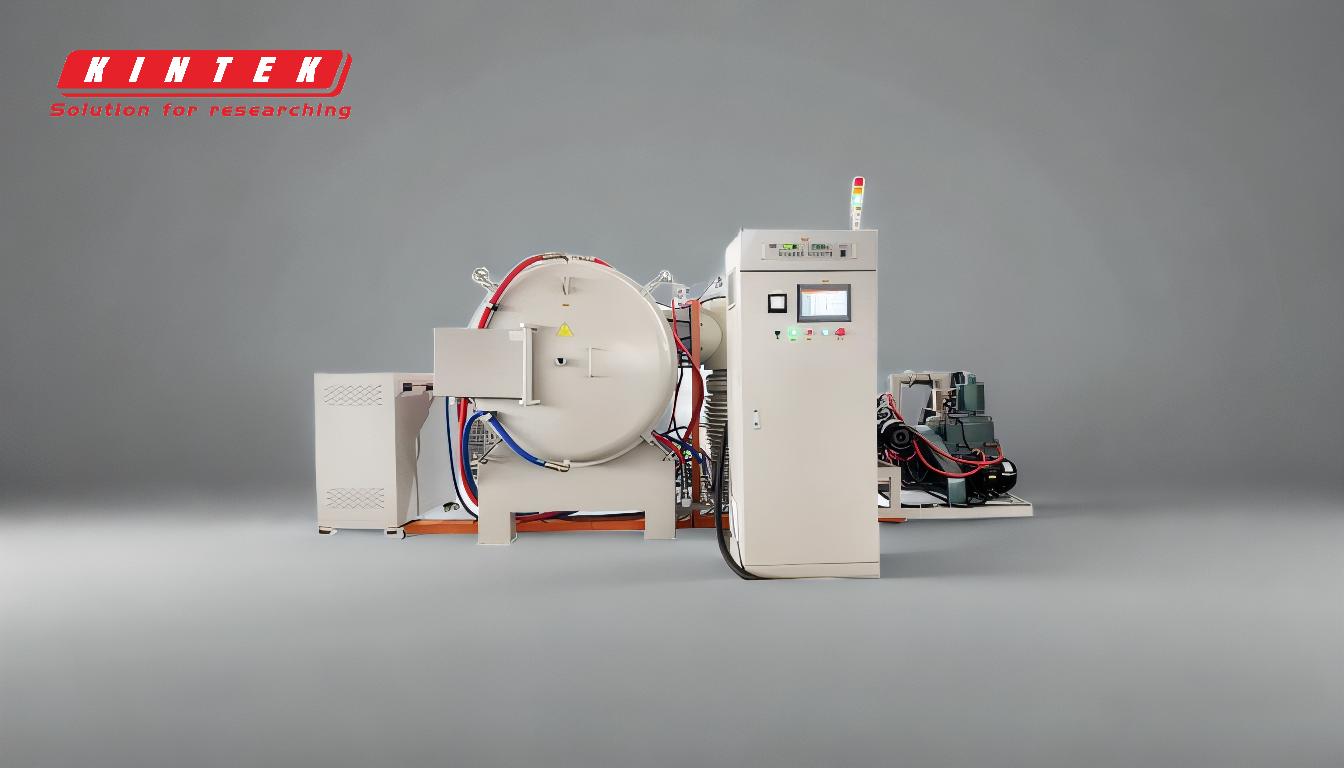
-
Silicone Mold Properties:
- Silicone molds used in vacuum casting are made from high-quality, flexible silicone rubber. This material is chosen for its durability, elasticity, and ability to withstand the vacuum environment.
- The flexibility of the silicone allows it to conform to the shape of the master model during mold creation and maintain its shape during the casting process.
- Silicone's inherent strength and resistance to tearing ensure that the mold remains intact even under the stress of repeated use.
-
Mold Design:
- The mold is designed with precision to match the geometry of the part being replicated. It typically consists of two or more halves that fit together seamlessly.
- Key features such as alignment pins, grooves, or interlocking edges are incorporated into the mold design to ensure that the halves stay together during the vacuum casting process.
- The mold may also include vents or channels to allow air to escape, which is crucial for achieving a bubble-free cast.
-
Vacuum Pressure:
- The vacuum environment plays a critical role in holding the mold together. When the mold is placed in the vacuum chamber, the external air pressure is reduced, creating a suction effect that compresses the mold tightly around the resin.
- This compression ensures that the mold halves remain in close contact, preventing any gaps or misalignments that could affect the final product.
-
Rigid Frame or Casing:
- To provide additional support, the silicone mold is often placed inside a rigid frame or casing. This frame holds the mold in place and prevents it from deforming under the vacuum pressure.
- The frame is typically made from materials like aluminum or plastic, which are strong enough to withstand the forces exerted during the casting process.
-
Clamping or Sealing Mechanisms:
- In some cases, mechanical clamps or seals are used to hold the mold halves together. These mechanisms ensure that the mold remains tightly closed during the vacuum casting process.
- Clamps or seals are particularly useful for larger or more complex molds, where additional force is required to keep the mold intact.
-
Resin Pouring and Curing:
- Once the mold is securely held together, liquid resin is poured into the mold cavity. The vacuum environment helps to draw the resin into all the intricate details of the mold, ensuring a high-quality finish.
- After pouring, the resin is allowed to cure, during which the mold continues to hold its shape due to the combined effects of the vacuum pressure, mold design, and rigid frame.
-
Reusability of the Mold:
- The combination of silicone's flexibility and the structural support provided by the vacuum and frame allows the mold to be reused multiple times without losing its shape or integrity.
- This reusability is a key advantage of vacuum casting, making it a cost-effective solution for small-batch production.
By leveraging the properties of silicone, the precision of mold design, and the forces exerted by vacuum pressure, vacuum casting ensures that the mold remains securely held together throughout the process, resulting in high-quality replicas of the original part.
Summary Table:
Key Factor | Role in Holding Mold Together |
---|---|
Silicone Mold Properties | Flexible yet durable, withstands vacuum pressure, resists tearing, and maintains shape. |
Mold Design | Precision design with alignment features, vents, and interlocking edges for seamless closure. |
Vacuum Pressure | Creates suction to compress mold halves, ensuring no gaps or misalignments. |
Rigid Frame/Casing | Provides structural support, prevents deformation under vacuum pressure. |
Clamping/Sealing | Mechanical clamps or seals ensure tight closure, especially for large or complex molds. |
Reusability | Silicone and structural support allow molds to be reused multiple times without losing integrity. |
Need high-quality replicas for your project? Contact us today to learn more about vacuum casting solutions!