Brazing is a joining process that uses a filler material to bond two or more metal components together. The filler material, which has a lower melting point than the base metals, is heated to its melting point and then flows into the joint by capillary action. The most commonly used filler materials for brazing include silver, copper, nickel, and gold-based alloys. Each of these materials has specific properties that make them suitable for different applications, particularly in terms of the types of metals being joined and the environmental conditions the joint will face. Proper cleaning of the materials before brazing is essential to ensure strong, high-quality joints.
Key Points Explained:
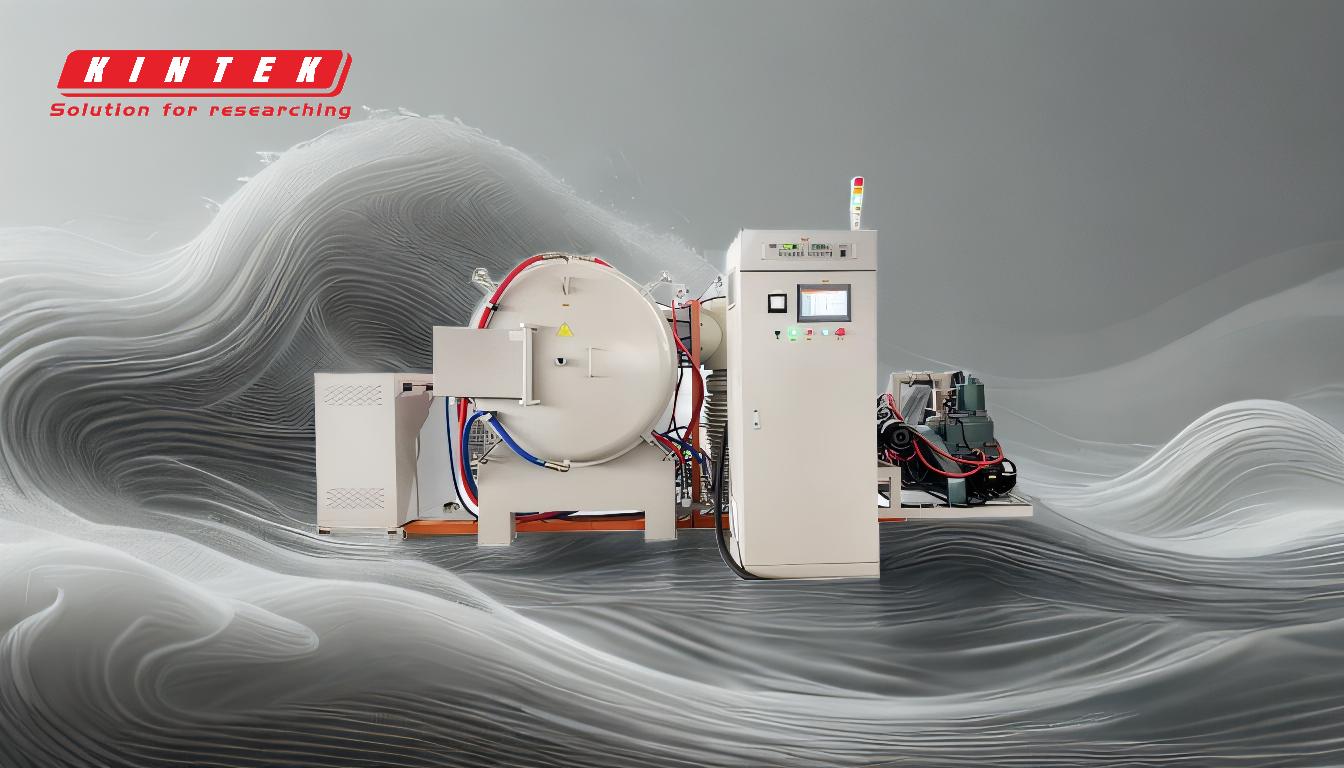
-
Common Filler Materials for Brazing:
- Silver-based fillers: These are widely used due to their excellent flow characteristics and ability to form strong joints with a variety of metals, including stainless steel, copper, and brass. Silver-based fillers are often alloyed with other metals like copper, zinc, or cadmium to improve their properties.
- Copper-based fillers: Copper is a popular choice for brazing due to its high thermal and electrical conductivity. It is often used in applications involving copper or copper alloys, such as in electrical components and heat exchangers.
- Nickel-based fillers: Nickel fillers are particularly suitable for joining stainless steels and heat-resistant alloys. They offer excellent strength and corrosion resistance, making them ideal for high-temperature and corrosive environments.
- Gold-based fillers: Gold fillers are used in specialized applications where high corrosion resistance and reliability are required, such as in aerospace and electronics industries. They are often used with stainless steels and other high-performance alloys.
-
Selection Criteria for Filler Materials:
- Compatibility with base metals: The filler material must be compatible with the base metals being joined to ensure a strong bond. This includes matching the thermal expansion coefficients and ensuring that the filler material wets the base metals properly.
- Operating environment: The filler material must be able to withstand the environmental conditions the joint will be exposed to, such as high temperatures, corrosive chemicals, or mechanical stress.
- Joint design and application requirements: The choice of filler material may also depend on the specific design of the joint and the functional requirements of the application, such as electrical conductivity or thermal performance.
-
Importance of Cleaning Before Brazing:
- Surface preparation: Before brazing, it is crucial to clean the surfaces of the base metals to remove any contaminants such as grease, oil, oxide layers, or scale. Contaminants can prevent the filler material from properly wetting the base metals, leading to weak joints.
- Cleaning methods: Common cleaning methods include mechanical cleaning (e.g., sandblasting or wire brushing), chemical cleaning (e.g., using solvents or acids), and thermal cleaning (e.g., heating to remove organic contaminants).
- Impact on joint quality: Proper cleaning ensures that the filler material can flow evenly into the joint, resulting in a strong, uniform bond. Poor cleaning can lead to defects such as voids, cracks, or incomplete bonding.
-
Applications of Different Filler Materials:
- Silver-based fillers: Commonly used in HVAC systems, electrical components, and plumbing applications.
- Copper-based fillers: Ideal for joining copper pipes, heat exchangers, and electrical conductors.
- Nickel-based fillers: Used in high-temperature applications such as gas turbines, chemical processing equipment, and power generation systems.
- Gold-based fillers: Applied in critical aerospace components, medical devices, and high-reliability electronic assemblies.
By understanding the properties and applications of different brazing filler materials, as well as the importance of proper surface preparation, you can select the most appropriate material for your specific brazing application and ensure the production of high-quality, durable joints.
Summary Table:
Filler Material | Key Properties | Common Applications |
---|---|---|
Silver-based | Excellent flow, strong joints | HVAC, electrical, plumbing |
Copper-based | High thermal/electrical conductivity | Heat exchangers, electrical conductors |
Nickel-based | High strength, corrosion resistance | Gas turbines, chemical processing |
Gold-based | High corrosion resistance, reliability | Aerospace, medical devices, electronics |
Need help selecting the right brazing material for your project? Contact our experts today for tailored solutions!