Furnace heating materials are selected based on their ability to withstand high temperatures, resist wear, and provide efficient heat transfer. Common materials include iron-chrome aluminum alloys, nickel chrome alloys, refractory metals like silicon carbide (SiC), graphite, and molybdenum. These materials are chosen for their thermal stability, durability, and resistance to oxidation. The choice of material depends on the furnace's operating temperature, the specific application, and the desired longevity of the heating elements. Insulation materials like lightweight refractory bricks and fiber blocks are also used to enhance thermal efficiency and protect the furnace structure.
Key Points Explained:
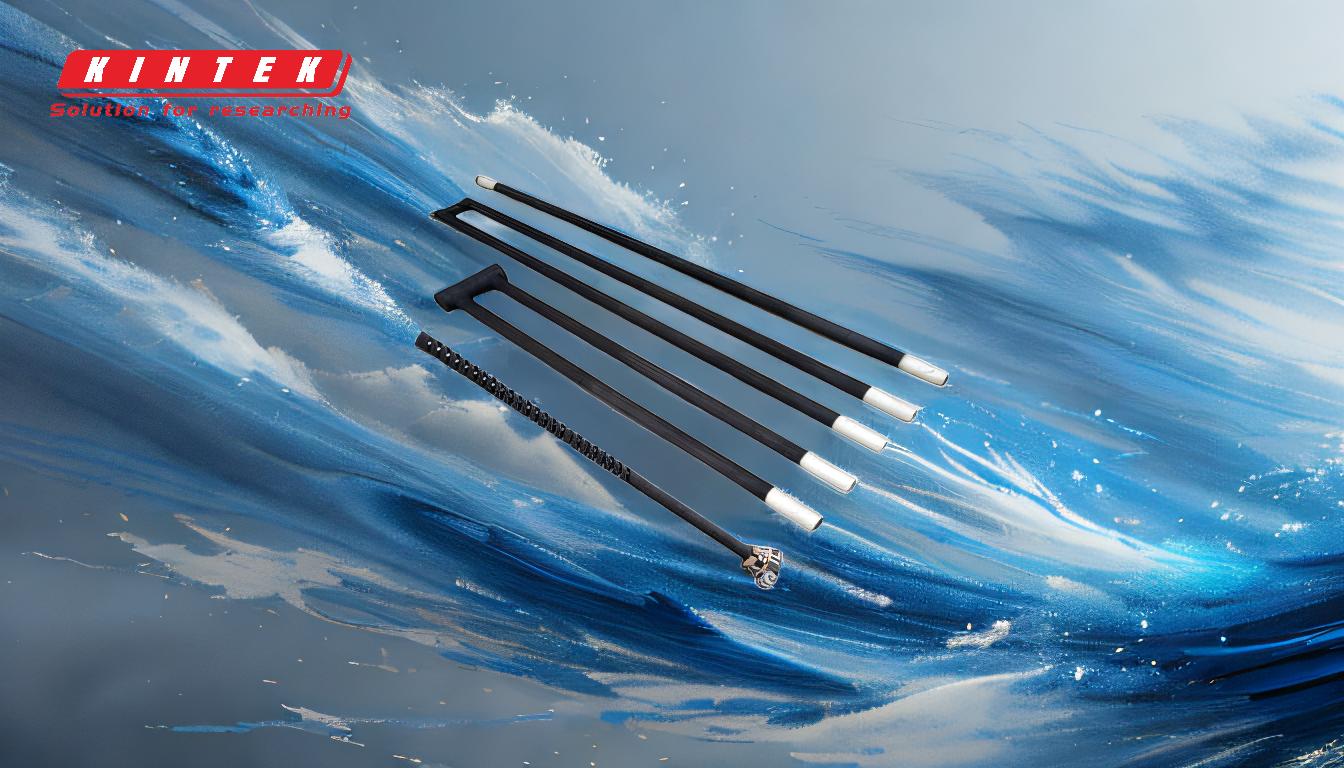
-
Iron-Chrome Aluminum Alloys:
- Properties: These alloys are known for their high resistance to oxidation and excellent thermal stability. They can withstand temperatures up to 1400°C.
- Applications: Commonly used in industrial furnaces for applications requiring consistent and high-temperature heating.
- Advantages: Cost-effective, durable, and suitable for a wide range of industrial processes.
-
Nickel Chrome Alloys:
- Properties: Nickel chrome alloys offer high electrical resistance and good oxidation resistance, making them ideal for heating elements.
- Applications: Used in both industrial and domestic heating applications, especially where precise temperature control is needed.
- Advantages: Long lifespan, excellent thermal conductivity, and resistance to corrosion.
-
Refractory Metals (e.g., Silicon Carbide - SiC):
- Properties: Refractory metals are dense, hard, and highly resistant to heat and wear. SiC, in particular, can withstand extremely high temperatures and has excellent thermal shock resistance.
- Applications: Used in high-temperature furnaces, such as those in the ceramics and metallurgy industries.
- Advantages: Exceptional durability, high thermal efficiency, and resistance to chemical attack.
-
Graphite:
- Properties: Graphite is lightweight, has high thermal conductivity, and can withstand very high temperatures without degrading.
- Applications: Used in vacuum furnaces and other high-temperature environments where oxidation is a concern.
- Advantages: Excellent thermal shock resistance, low thermal expansion, and good electrical conductivity.
-
Molybdenum:
- Properties: Molybdenum has a high melting point (2623°C) and excellent strength at elevated temperatures. It is available in pure form or lanthanated for enhanced performance.
- Applications: Used in high-temperature furnaces, especially in the aerospace and semiconductor industries.
- Advantages: High thermal stability, resistance to corrosion, and excellent mechanical properties at high temperatures.
-
Insulation Materials:
- Properties: Lightweight refractory bricks and insulation fiber blocks are used to reduce heat loss and improve the thermal efficiency of the furnace.
- Applications: Essential in all types of furnaces to maintain high internal temperatures while protecting the external structure.
- Advantages: Enhances energy efficiency, reduces operating costs, and extends the lifespan of the furnace.
-
Silicon Steel:
- Properties: Silicon steel is used in the construction of reactors within furnaces due to its magnetic properties and high electrical resistance.
- Applications: Primarily used in the core of reactors to ensure efficient energy transfer and minimize losses.
- Advantages: High efficiency, reduced energy consumption, and long operational life when using new, high-quality products.
In summary, the choice of furnace heating material is critical to the performance, efficiency, and longevity of the furnace. Each material has specific properties that make it suitable for particular applications, and the selection should be based on the operating conditions and requirements of the furnace.
Summary Table:
Material | Key Properties | Applications | Advantages |
---|---|---|---|
Iron-Chrome Aluminum | High oxidation resistance, thermal stability (up to 1400°C) | Industrial furnaces, high-temperature heating | Cost-effective, durable, versatile |
Nickel Chrome Alloys | High electrical resistance, good oxidation resistance | Industrial and domestic heating, precise temperature control | Long lifespan, excellent thermal conductivity, corrosion-resistant |
Silicon Carbide (SiC) | Dense, hard, high heat and wear resistance, thermal shock resistance | High-temperature furnaces (ceramics, metallurgy) | Exceptional durability, high thermal efficiency, chemical resistance |
Graphite | Lightweight, high thermal conductivity, withstands high temperatures | Vacuum furnaces, high-temperature environments | Thermal shock resistance, low expansion, good electrical conductivity |
Molybdenum | High melting point (2623°C), strength at elevated temperatures | Aerospace, semiconductor industries | Thermal stability, corrosion resistance, mechanical strength |
Insulation Materials | Lightweight refractory bricks, fiber blocks, reduce heat loss | All furnace types, thermal efficiency enhancement | Energy efficiency, cost reduction, furnace protection |
Silicon Steel | Magnetic properties, high electrical resistance | Reactor cores in furnaces | High efficiency, reduced energy consumption, long operational life |
Need help selecting the right furnace heating material? Contact our experts today for tailored solutions!