Electron beam (e-beam) evaporation is a versatile thin-film deposition technique used to coat substrates with a wide variety of materials. It is particularly effective for depositing high-temperature and refractory materials that are challenging to process using other methods like resistive thermal evaporation. The materials used in e-beam evaporation can be broadly categorized into metals (precious, regular, and refractory), dielectric materials, and ceramics. These materials are chosen based on their properties, such as high melting points, conductivity, or optical characteristics, making them suitable for applications in solar cells, OLED displays, optical coatings, and thin-film transistors.
Key Points Explained:
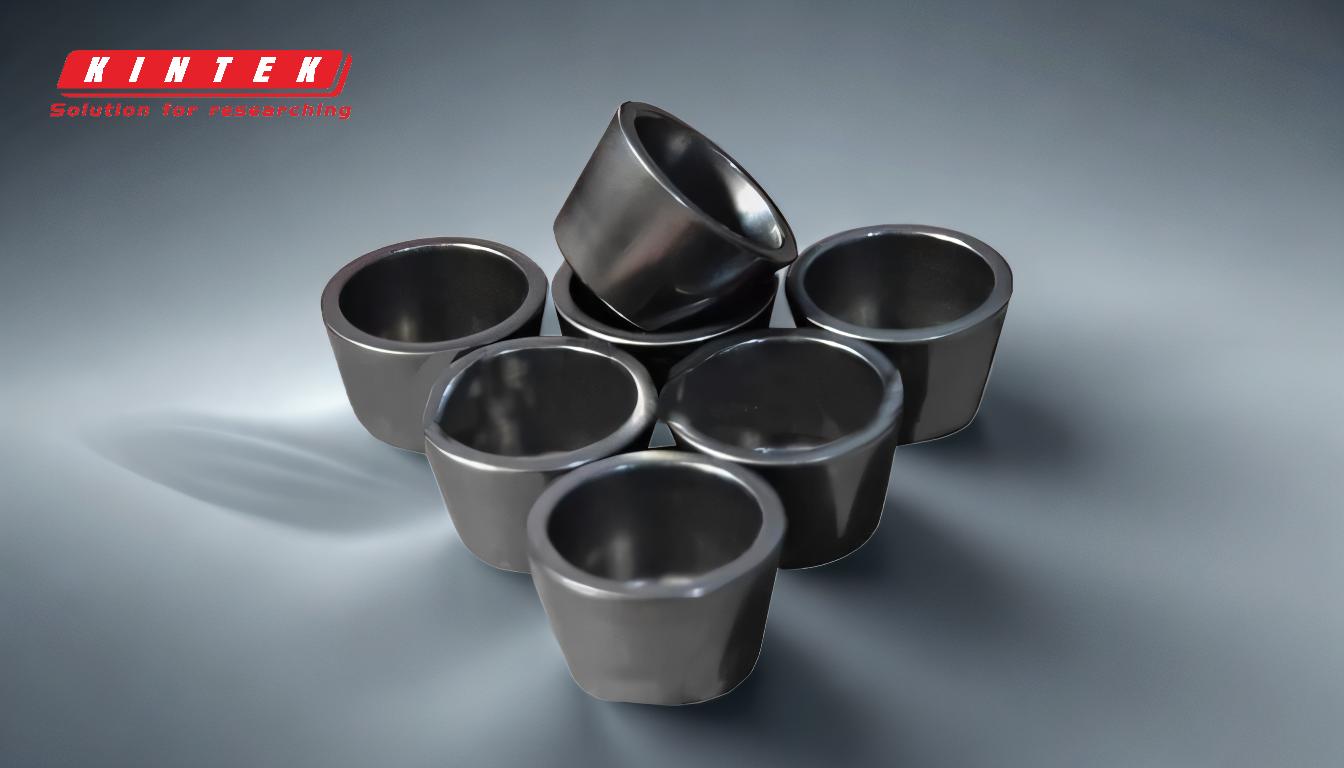
-
Types of Materials Used in E-Beam Evaporation:
- Precious Metals: Gold, silver, and platinum are commonly used due to their excellent conductivity and reflectivity. These materials are ideal for applications in electronics and optics.
- Regular Metals: Aluminum, copper, nickel, titanium, tin, and chromium are frequently deposited using e-beam evaporation. These metals are widely used in solar cells, OLED displays, and thin-film transistors.
- Refractory Metals: Tungsten, tantalum, and graphite are examples of refractory metals that can withstand extremely high temperatures. These materials are used in specialized applications requiring durability and high thermal resistance.
- Dielectric Materials: Indium tin oxide (ITO) and silicon dioxide (SiO2) are dielectric materials often used for optical coatings and transparent conductive layers in displays and solar cells.
- Ceramics: Materials like hafnium dioxide (HfO2) and aluminum oxide (Al2O3) are used for UV coatings and other high-temperature applications.
-
Advantages of E-Beam Evaporation for High-Temperature Materials:
- E-beam evaporation is particularly suitable for materials with high melting points, such as tungsten and tantalum, which are difficult to process using standard thermal evaporation.
- The technique allows for precise control over the deposition process, ensuring high-quality, uniform coatings even for complex materials.
-
Applications of E-Beam Evaporation Materials:
- Solar Cells: Gold and other conductive metals are used to create efficient electrical contacts.
- Optical Coatings: Dielectric materials like SiO2 and HfO2 are used to create anti-reflective and protective layers.
- OLED Displays: Metals such as aluminum and ITO are used for conductive layers and electrodes.
- Thin-Film Transistors: Materials like nickel and chromium are deposited to create thin, conductive layers.
-
Reactive Deposition with E-Beam Evaporation:
- E-beam evaporation can also deposit non-metallic films by introducing reactive gases like oxygen or nitrogen during the process. This allows for the creation of oxide and nitride films, expanding the range of materials that can be deposited.
-
Comparison with Thermal Evaporation:
- While thermal evaporation can deposit many of the same materials, e-beam evaporation is better suited for high-temperature and refractory materials due to its higher energy input and precise control.
In summary, e-beam evaporation is a highly adaptable technique capable of depositing a wide range of materials, including precious metals, regular metals, refractory metals, dielectric materials, and ceramics. Its ability to handle high-temperature materials and provide precise, uniform coatings makes it indispensable in industries such as electronics, optics, and renewable energy.
Summary Table:
Category | Examples | Applications |
---|---|---|
Precious Metals | Gold, Silver, Platinum | Electronics, optics (conductivity, reflectivity) |
Regular Metals | Aluminum, Copper, Nickel, Titanium | Solar cells, OLED displays, thin-film transistors |
Refractory Metals | Tungsten, Tantalum, Graphite | High-temperature applications, durability |
Dielectric Materials | ITO, SiO2 | Optical coatings, transparent conductive layers |
Ceramics | HfO2, Al2O3 | UV coatings, high-temperature applications |
Learn how e-beam evaporation can enhance your thin-film applications—contact our experts today!