Induction furnaces are widely used in metallurgical processes for melting and heating metals due to their efficiency, precise temperature control, and ability to produce high-quality metal with fewer impurities. The materials used in an induction furnace are carefully selected to ensure optimal performance and durability. Key components include the inductor, furnace body, power supply, capacitor, and control system. The furnace crucible, made of refractory materials, plays a critical role in containing the molten metal. Additionally, the choice of raw materials, such as selected scrap metal, ensures cleaner steel production compared to arc furnaces.
Key Points Explained:
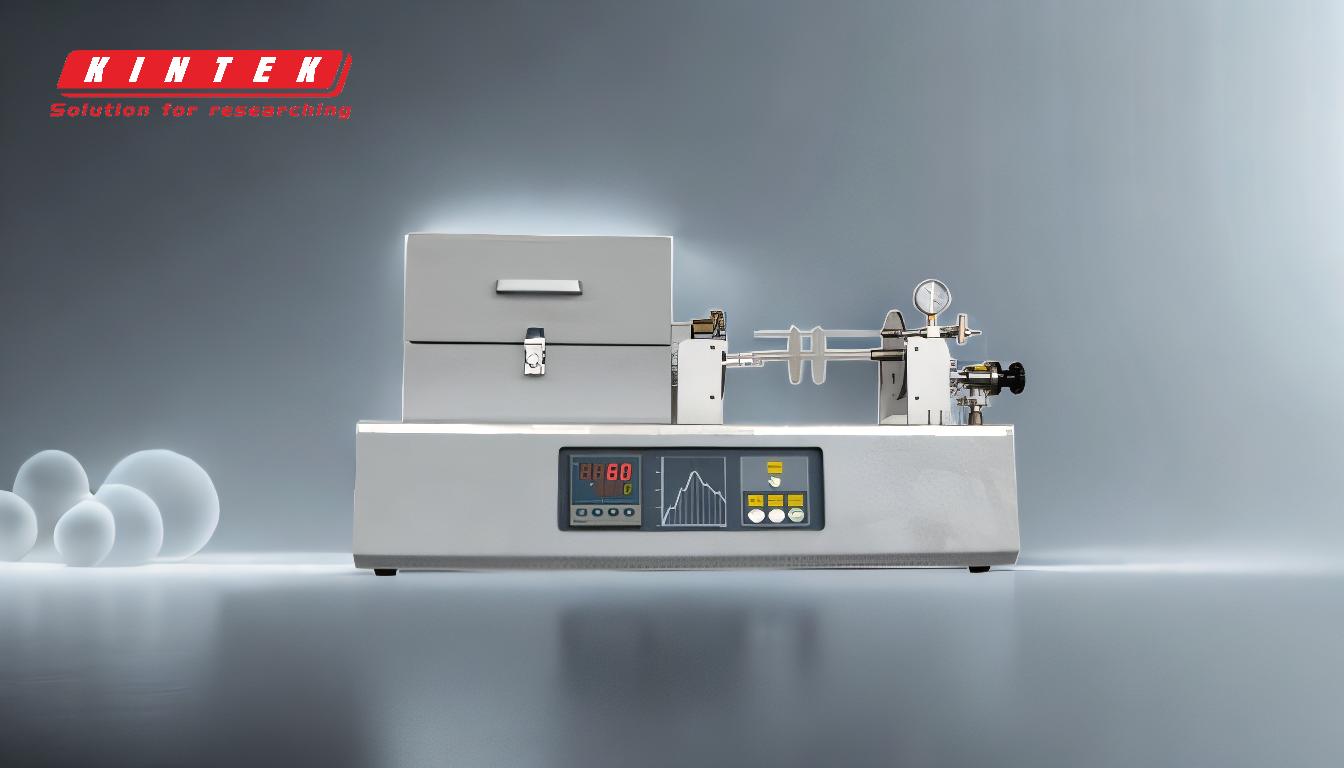
-
Core Components of an Induction Furnace
- Inductor (Induction Coil): The inductor generates a magnetic field that induces eddy currents in the metal, causing it to heat up. It is typically made of copper or aluminum due to their high electrical conductivity.
- Furnace Body: The furnace body houses the crucible and provides structural support. It is often constructed from durable materials like steel to withstand high temperatures and mechanical stress.
- Power Supply: The power supply, often an IGBT induction furnace, converts electrical energy into the high-frequency alternating current required for induction heating. IGBT (Insulated Gate Bipolar Transistor) technology is preferred for its efficiency and precise control.
- Capacitor: Capacitors are used in the resonant circuit to store and release energy, ensuring efficient operation of the induction furnace.
- Control System: Modern induction furnaces use advanced control systems to regulate temperature, power input, and other parameters, ensuring consistent and high-quality output.
-
Crucible Materials
- The crucible, which holds the molten metal, is made of refractory materials that can withstand extremely high temperatures and resist chemical reactions with the metal. Common materials include:
- Silica: Used for melting non-ferrous metals like aluminum and copper.
- Alumina: Suitable for high-temperature applications and resistant to corrosion.
- Graphite: Often used for melting precious metals due to its high thermal conductivity and resistance to thermal shock.
- Magnesia: Ideal for melting steel and other ferrous metals.
- The crucible, which holds the molten metal, is made of refractory materials that can withstand extremely high temperatures and resist chemical reactions with the metal. Common materials include:
-
Raw Materials for Melting
- Induction furnaces typically use selected scrap metal, which is free from impurities and oxides. This results in fewer inclusions and cleaner steel production.
- Unlike arc furnaces, which use oxygen blowing and materials like pig iron and sponge iron (DRI), induction furnaces avoid introducing additional impurities. This makes refining easier and enhances the quality of the final product.
-
Advantages of Induction Furnaces
- Uniform Heating: The induction electrothermal effect ensures uniform heating and melting, leading to consistent composition and temperature.
- Energy Efficiency: Induction furnaces are highly efficient, with minimal heat loss compared to traditional furnaces.
- Cleaner Steel Production: By using selected scrap and avoiding oxygen blowing, induction furnaces produce steel with fewer impurities, especially when combined with ladle refining and vacuum degassing.
-
Applications and Industry Use
- Induction furnaces are widely used in industries such as steelmaking, foundries, and metal casting. They are particularly valued for their ability to melt and refine metals with high precision and minimal contamination.
In summary, the materials used in an induction furnace, including the inductor, crucible, and raw metals, are carefully chosen to ensure efficient operation and high-quality output. The integration of advanced technologies like IGBT power supplies further enhances their performance, making induction furnaces a preferred choice in modern metallurgical processes.
Summary Table:
Component | Materials | Purpose |
---|---|---|
Inductor (Coil) | Copper, Aluminum | Generates magnetic field for heating |
Furnace Body | Steel | Provides structural support and withstands high temperatures |
Power Supply | IGBT-based systems | Converts electrical energy for efficient induction heating |
Capacitor | High-energy storage capacitors | Ensures efficient operation in the resonant circuit |
Control System | Advanced digital systems | Regulates temperature and power for consistent output |
Crucible | Silica, Alumina, Graphite, Magnesia | Contains molten metal and resists high temperatures and chemical reactions |
Raw Materials | Selected scrap metal | Ensures cleaner steel production with fewer impurities |
Ready to optimize your metallurgical processes? Contact us today to learn more about induction furnaces!