The sintering process involves the use of a wide range of materials, including metals, ceramics, and polymers, each selected for their specific properties and applications. Metals such as iron, carbon steels, stainless steel, aluminum, nickel, copper, titanium alloy, molybdenum, and tungsten are commonly used due to their high melting points and suitability for powder metallurgy. Ceramics are favored for high-temperature components, while polymers are utilized in rapid prototyping and filter manufacturing. These materials are processed through sintering to enhance their mechanical, thermal, and chemical properties, making them ideal for various industrial applications, including additive manufacturing and the production of small, precision components.
Key Points Explained:
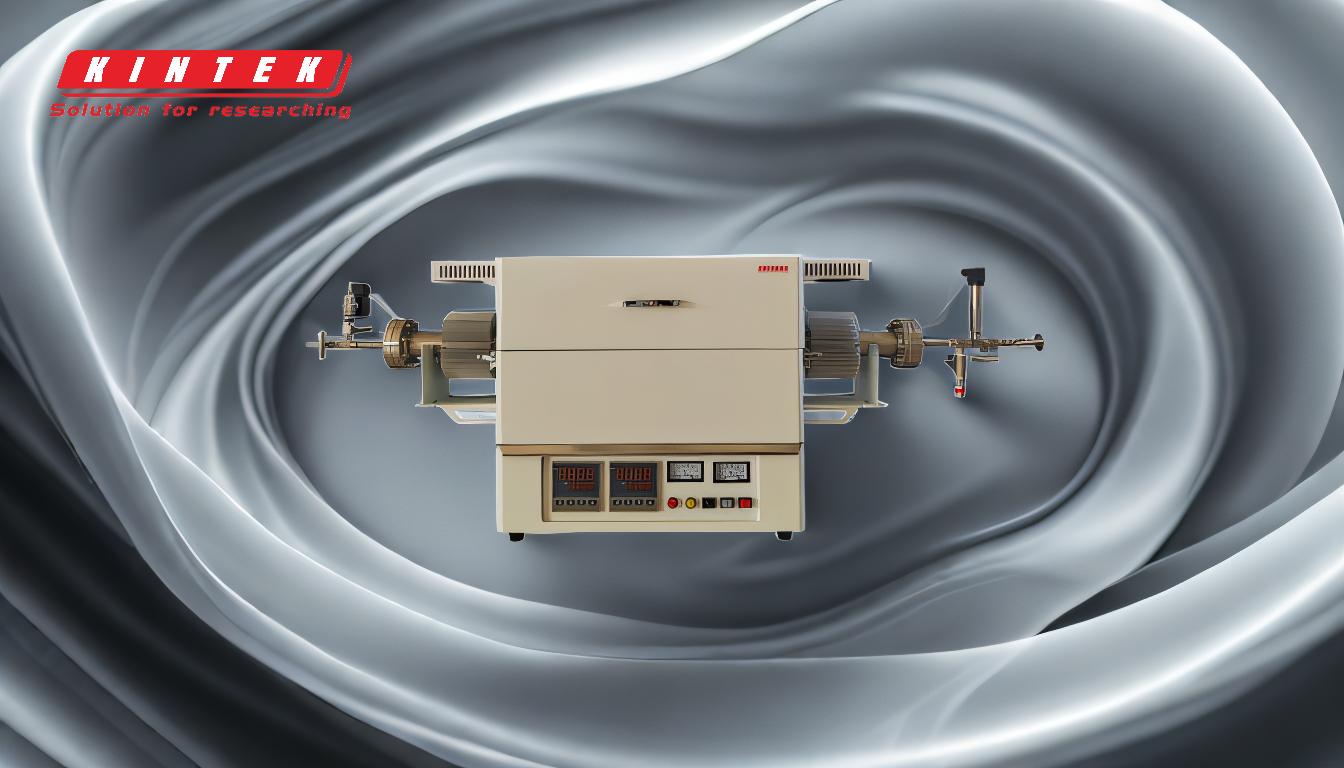
-
Metals Used in Sintering:
- Iron and Carbon Steels: These are foundational materials in sintering, often used for their strength and durability. They are processed to improve properties like hardness and wear resistance.
- Stainless Steel: Known for its corrosion resistance, stainless steel is widely used in sintering for components that require both strength and resistance to environmental factors.
- Aluminum: Lightweight and with good thermal conductivity, aluminum is used in sintering for applications requiring reduced weight and efficient heat dissipation.
- Nickel and Nickel Alloys: These materials are chosen for their high-temperature resistance and strength, making them suitable for aerospace and high-stress applications.
- Copper and Copper Alloys: With excellent electrical conductivity, copper is used in sintering for electrical components and connectors.
- Titanium Alloy: Known for its high strength-to-weight ratio and biocompatibility, titanium alloys are used in medical implants and aerospace components.
- Molybdenum and Tungsten: These refractory metals are used in sintering for their extremely high melting points, making them ideal for high-temperature applications.
-
Ceramics in Sintering:
- High-Temperature Components: Ceramics are sintered to produce components that can withstand extreme temperatures, such as gears and bearings used in high-heat environments.
- Electrical Insulators: Sintered ceramics are used in electrical applications where insulation is critical, such as in spark plugs and circuit breakers.
-
Polymers in Sintering:
- Rapid Prototyping: Polymers are used in sintering for rapid prototyping, allowing for the quick production of models and prototypes.
- Filter Manufacturing: Sintered polymers are used to create filters with precise pore sizes, essential for applications in filtration and separation processes.
-
Processing and Enhancement:
- Powder Metallurgy: Metal powders are sintered under controlled conditions, often with protective gases, to enhance properties like density, strength, and wear resistance.
- Additive Manufacturing: Advances in sintering technology have made it suitable for additive manufacturing, where complex geometries can be created layer by layer.
-
Applications:
- Industrial Components: Sintered materials are used to produce small, precision components like gears, pulleys, and bearings.
- Aerospace and Automotive: High-strength, lightweight sintered materials are used in the aerospace and automotive industries for components that require high performance.
- Medical Devices: Biocompatible materials like titanium alloys are sintered for use in medical implants and devices.
By understanding the materials used in sintering and their specific applications, purchasers can make informed decisions about the best materials for their needs, ensuring optimal performance and cost-effectiveness in their projects.
Summary Table:
Material Type | Examples | Key Properties | Applications |
---|---|---|---|
Metals | Iron, Carbon Steels, Stainless Steel, Aluminum, Nickel, Copper, Titanium Alloy, Molybdenum, Tungsten | High melting points, strength, corrosion resistance, lightweight, electrical conductivity | Aerospace, automotive, medical implants, electrical components |
Ceramics | High-temperature components, electrical insulators | Extreme temperature resistance, electrical insulation | High-heat environments, spark plugs, circuit breakers |
Polymers | Rapid prototyping, filter manufacturing | Lightweight, precise pore sizes | Rapid prototyping, filtration systems |
Processing | Powder metallurgy, additive manufacturing | Enhanced density, strength, wear resistance, complex geometries | Industrial components, additive manufacturing |
Need help selecting the right sintering materials for your project? Contact our experts today for tailored solutions!