PVD (Physical Vapor Deposition) coatings are applied to a wide range of metals, alloys, and substrates, depending on the desired properties and applications. Common metals that undergo PVD coating include stainless steel, titanium, zirconium, aluminum, and copper, as well as specialized alloys like tool steels and titanium alloys. These coatings are used to enhance properties such as hardness, wear resistance, chemical stability, and aesthetic appearance. PVD coatings are typically applied to materials that can withstand high temperatures (up to 800°F) and are compatible with vacuum deposition processes. The technique is versatile and can be used on metals, ceramics, and even some polymers, making it suitable for industries ranging from aerospace and automotive to medical and electronics.
Key Points Explained:
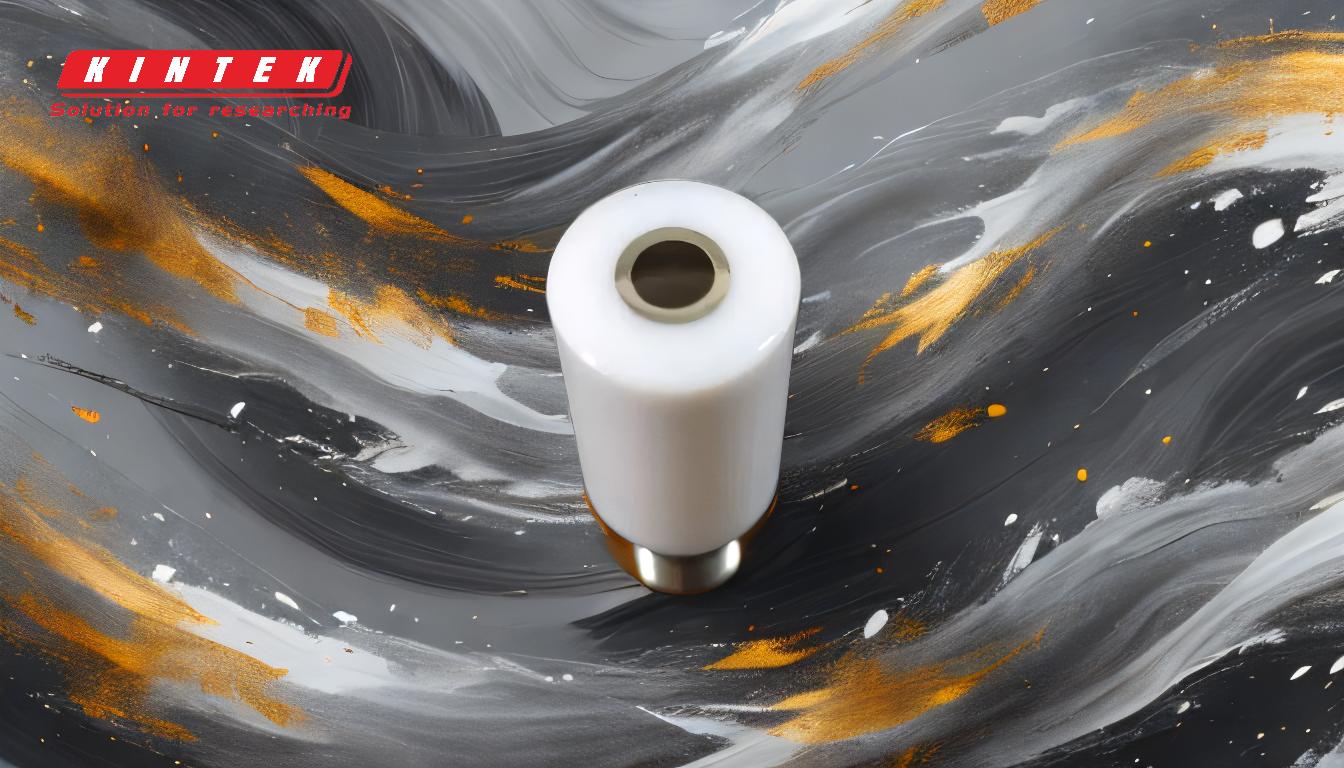
-
Common Metals for PVD Coating:
- Stainless Steel: Commonly used grades include 303, 440C, and 17-4 stainless steels. These are often chosen for their durability and corrosion resistance, making them ideal for medical and industrial applications.
- Titanium and Titanium Alloys: Titanium is lightweight, strong, and biocompatible, making it a popular choice for aerospace, medical implants, and high-performance applications.
- Aluminum: While less common due to its low melting point, aluminum can still be PVD coated for specific applications where weight reduction is critical.
- Copper: Used in electronics and aerospace for its excellent electrical conductivity and thermal properties.
- Zirconium: Often used in specialized coatings for its high corrosion resistance and biocompatibility.
-
Substrate Compatibility:
- PVD coatings can be applied to a variety of substrates, including metals, ceramics, and some polymers. The substrate must be able to withstand the high temperatures (typically up to 800°F) and vacuum conditions of the PVD process.
-
Specialized Coatings:
- Carbides, Nitrides, and Borides: These coatings are used for specific performance requirements, such as increased hardness, wear resistance, or thermal stability. Examples include titanium nitride (TiN) and zirconium nitride (ZrN), which are commonly used in cutting tools and automotive components.
- Gold and Other Precious Metals: Gold is frequently requested for aerospace electronics due to its excellent conductivity and resistance to corrosion.
-
Process Conditions:
- PVD coating is carried out in a vacuum chamber at temperatures between 50 and 600 degrees Celsius. The process involves vaporizing the coating material (target) and depositing it onto the substrate (workpiece) in a controlled environment. Reactive gases like nitrogen, acetylene, or oxygen may be introduced to create compound coatings with tailored properties.
-
Applications of PVD Coatings:
- Aerospace: Used for components requiring high strength, wear resistance, and thermal stability.
- Medical: Applied to implants and surgical instruments for biocompatibility and corrosion resistance.
- Automotive: Enhances the durability and performance of engine parts, cutting tools, and decorative elements.
- Electronics: Provides conductive and protective coatings for components like connectors and circuit boards.
-
Advantages of PVD Coatings:
- Thin and Durable: PVD coatings are extremely thin (0.5 – 5 μm) but offer significant improvements in surface hardness, wear resistance, and chemical stability.
- Aesthetic Versatility: The process allows for a wide range of colors and finishes, making it suitable for decorative applications.
- Strong Bonding: The coatings form a strong bond with the substrate, ensuring long-lasting performance.
By understanding the metals and substrates suitable for PVD coating, as well as the process conditions and applications, purchasers can make informed decisions when selecting materials and coatings for their specific needs.
Summary Table:
Category | Details |
---|---|
Common Metals | Stainless steel, titanium, zirconium, aluminum, copper, tool steels, titanium alloys |
Substrate Compatibility | Metals, ceramics, and some polymers that withstand high temperatures and vacuum conditions |
Specialized Coatings | Carbides, nitrides, borides, gold, and other precious metals |
Process Conditions | Vacuum chamber, 50–600°C, reactive gases (nitrogen, acetylene, oxygen) |
Applications | Aerospace, medical, automotive, electronics |
Advantages | Thin, durable, wear-resistant, chemically stable, aesthetic versatility |
Ready to enhance your materials with PVD coatings? Contact our experts today for tailored solutions!