Brazing is a metal-joining process that involves melting a filler metal into the joint between two or more base metals. While brazing is a versatile process suitable for many metals, certain metals are challenging or impossible to braze due to their physical and chemical properties. For example, cast iron, chromium, and tungsten are difficult to braze because of their brittleness, high melting points, or poor wetting characteristics. Understanding which metals cannot be brazed is crucial for selecting appropriate joining methods in manufacturing and repair processes.
Key Points Explained:
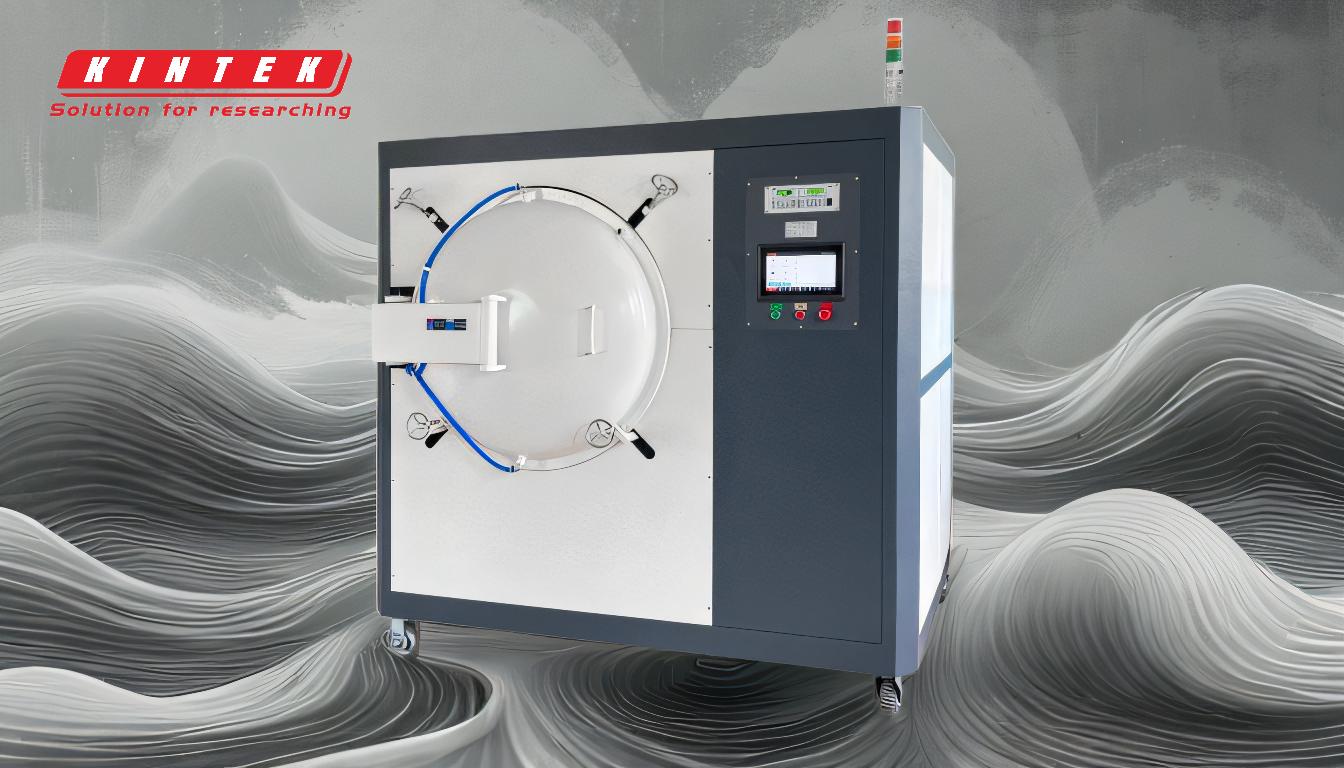
-
Cast Iron
- Why it cannot be brazed: Cast iron is brittle and has a high carbon content, which makes it prone to cracking under thermal stress during brazing. The heating and cooling cycles involved in brazing can cause thermal expansion and contraction, leading to fractures in the material.
- Alternative joining methods: Welding with specialized techniques or mechanical fastening is often used instead of brazing for cast iron.
-
Chromium
- Why it cannot be brazed: Chromium forms a stable oxide layer on its surface, which prevents the filler metal from wetting and bonding effectively. This oxide layer is difficult to remove, even with flux, making brazing impractical.
- Alternative joining methods: Chromium is often joined using welding or diffusion bonding, which can overcome the challenges posed by its oxide layer.
-
Tungsten
- Why it cannot be brazed: Tungsten has an extremely high melting point (3,422°C or 6,192°F), which makes it incompatible with most brazing filler metals. Additionally, tungsten is brittle and prone to cracking under thermal stress.
- Alternative joining methods: Tungsten is typically joined using specialized welding techniques or mechanical methods.
-
General Challenges in Brazing Certain Metals
- Metals with high melting points, brittleness, or poor wetting characteristics are generally unsuitable for brazing. These properties make it difficult to achieve a strong, reliable joint using traditional brazing methods.
- Understanding the limitations of brazing helps in selecting the right joining process for specific applications.
-
Importance of Material Selection in Joining Processes
- When brazing is not feasible, alternative methods such as welding, soldering, or mechanical fastening should be considered.
- Proper material selection and process planning are essential to ensure the durability and performance of the final product.
By recognizing the limitations of brazing for certain metals, manufacturers and engineers can make informed decisions about the most appropriate joining techniques for their specific needs.
Summary Table:
Metal | Why It Cannot Be Brazed | Alternative Joining Methods |
---|---|---|
Cast Iron | Brittle with high carbon content; prone to cracking under thermal stress. | Welding with specialized techniques or mechanical fastening. |
Chromium | Forms a stable oxide layer that prevents filler metal from bonding effectively. | Welding or diffusion bonding. |
Tungsten | Extremely high melting point; brittle and prone to cracking under thermal stress. | Specialized welding techniques or mechanical methods. |
Need help selecting the right joining method for your project? Contact our experts today for tailored solutions!