During the sintering of ceramic powders, several physical changes occur that transform the powder into a dense, solid material. These changes include the removal of water, organic matter, and adsorbed gases, as well as stress relief and the reduction of surface oxides. As the temperature increases, material migration, recrystallization, and grain growth take place, leading to a reduction in surface energy and the closing of pores. This results in a denser material with improved mechanical properties, such as increased strength and durability. The microstructure of the material, including grain size, pore size, and grain boundary distribution, is significantly influenced by the sintering process.
Key Points Explained:
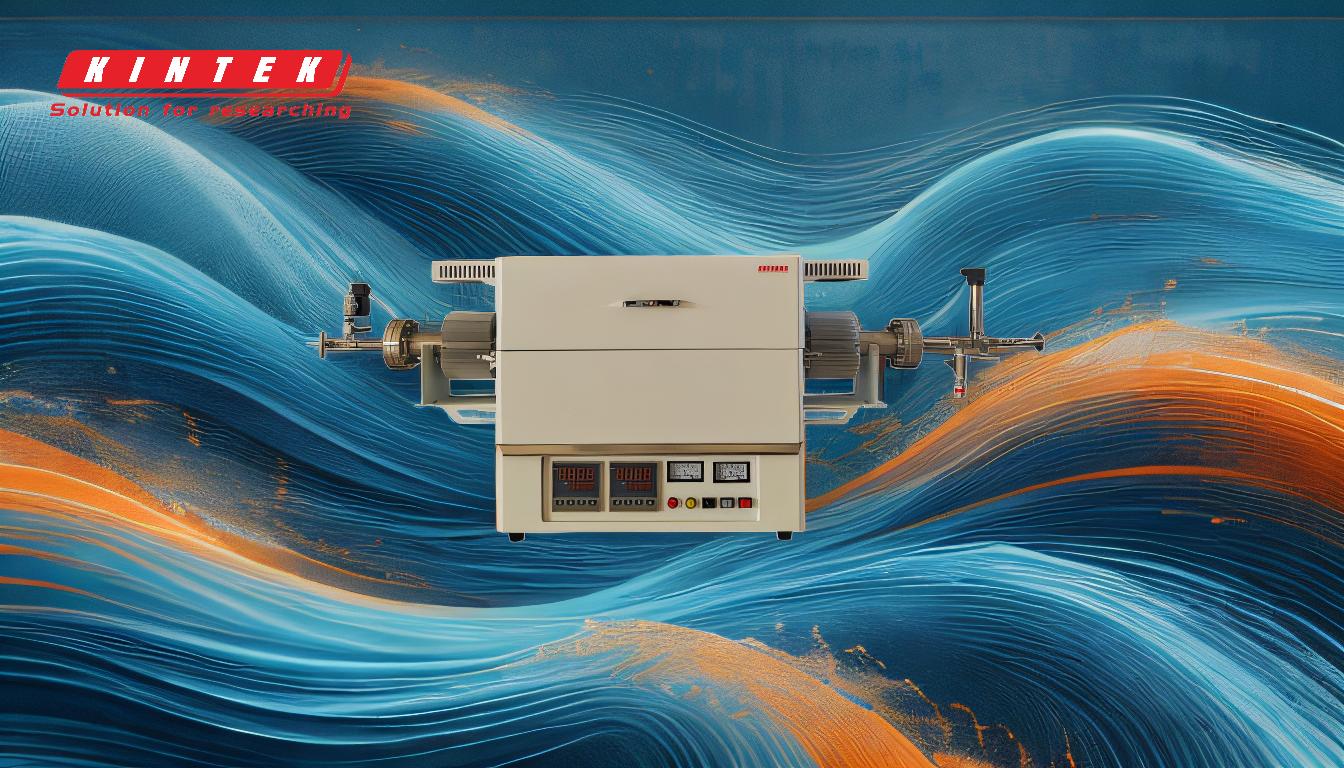
-
Removal of Water and Organic Matter:
- During the initial stages of sintering, any residual water or organic matter in the ceramic powder is evaporated or removed. This is crucial because the presence of these substances can lead to defects in the final product, such as cracks or voids. The removal process typically occurs at lower temperatures before the main sintering phase begins.
-
Removal of Adsorbed Gases:
- Adsorbed gases on the surface of the powder particles are also driven off during sintering. These gases can interfere with the bonding between particles, so their removal is essential for achieving a dense and uniform microstructure.
-
Stress Relief:
- Sintering helps to relieve internal stresses that may have been introduced during the powder compaction process. This stress relief is important for preventing warping or cracking of the material during or after sintering.
-
Reduction of Surface Oxides:
- Surface oxides on the powder particles are reduced during sintering. This reduction is necessary because oxides can act as barriers to diffusion, which is a key mechanism in the sintering process. The reduction of oxides facilitates better bonding between particles.
-
Material Migration:
- At high temperatures, material migration occurs through various mechanisms such as diffusion, viscous flow, and grain boundary sliding. This migration leads to the filling of voids and the reduction of porosity, resulting in a denser material.
-
Recrystallization:
- Recrystallization involves the formation of new, strain-free grains from the existing powder particles. This process helps to eliminate defects and improve the overall microstructure of the material.
-
Grain Growth:
- Grain growth is the increase in size of the individual grains within the material. This occurs as smaller grains merge to form larger ones, driven by the reduction in surface energy. Grain growth can affect the mechanical properties of the material, such as its strength and toughness.
-
Reduction of Surface Energy:
- The sintering process reduces the surface energy of the powder particles by decreasing the vapor-solid interface. This reduction in surface energy is a driving force for the densification of the material.
-
Pore Closure:
- As sintering progresses, existing pores within the material diminish or fully close up. This pore closure is essential for achieving a high-density material with improved mechanical properties.
-
Microstructural Changes:
- The sintering process directly affects the grain size, pore size, and grain boundary shape and distribution in the microstructure of the material. These changes in turn influence the properties of the material, such as its strength, durability, and thermal conductivity.
-
Temperature and Time:
- Sintering typically occurs at high temperatures, usually below the melting point of the material. The process often requires extensive diffusion and relatively high temperatures (>~0.6Tm, where Tm is the melting point). The duration of sintering also plays a critical role in determining the final properties of the material.
-
Mechanical Properties:
- The physical changes that occur during sintering, such as densification, grain growth, and pore closure, lead to improvements in the mechanical properties of the material. These properties include increased strength, hardness, and durability, making the sintered ceramic suitable for various industrial applications.
In summary, the sintering of ceramic powders involves a series of complex physical changes that transform the powder into a dense, solid material. These changes are driven by high temperatures and result in a material with improved mechanical properties and a refined microstructure. Understanding these processes is crucial for optimizing the sintering conditions to achieve the desired material properties.
Summary Table:
Stage | Description |
---|---|
Removal of Water/Organic Matter | Evaporation of residues at lower temperatures to prevent defects like cracks or voids. |
Removal of Adsorbed Gases | Gases on particle surfaces are driven off to ensure uniform bonding and microstructure. |
Stress Relief | Internal stresses from compaction are relieved to prevent warping or cracking. |
Reduction of Surface Oxides | Oxides are reduced to enhance diffusion and bonding between particles. |
Material Migration | High-temperature migration fills voids, reducing porosity and increasing density. |
Recrystallization | Formation of new, defect-free grains improves microstructure. |
Grain Growth | Smaller grains merge into larger ones, affecting strength and toughness. |
Reduction of Surface Energy | Surface energy decreases, driving densification and pore closure. |
Pore Closure | Pores diminish or close, enhancing material density and mechanical properties. |
Microstructural Changes | Grain size, pore size, and grain boundaries are refined, improving strength and durability. |
Temperature & Time | High temperatures (>0.6Tm) and duration are critical for achieving desired properties. |
Mechanical Properties | Improved strength, hardness, and durability make sintered ceramics ideal for industrial use. |
Optimize your ceramic sintering process for superior results—contact our experts today!