Injection molding machines vary significantly in size, typically ranging from about 1 ton to over 1000 tons in clamping force. The size of the machine required depends on factors such as the size and complexity of the part being produced, as well as the desired production volume. Larger machines are necessary for bigger, more complex parts, while smaller machines are suitable for simpler, smaller components. Understanding the specific requirements of your application is crucial in selecting the appropriate machine size.
Key Points Explained:
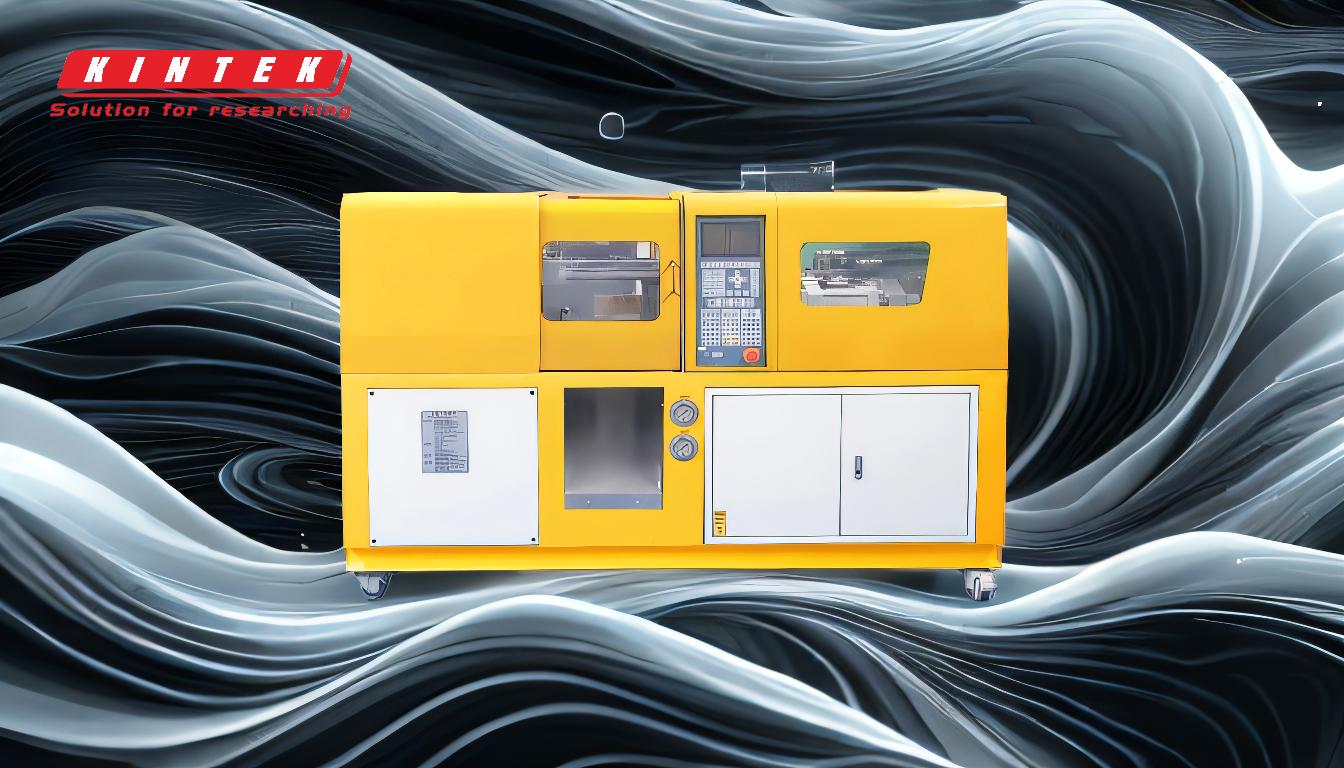
-
Range of Sizes:
- Injection molding machines can range from as small as 1 ton to as large as 1000 tons or more in clamping force.
- The size of the machine is typically measured by its clamping force, which is the force required to keep the press mold closed during the injection process.
-
Factors Influencing Machine Size:
- Part Size and Complexity: Larger and more complex parts require larger machines with higher clamping forces to ensure the mold remains securely closed during the injection process.
- Production Volume: Higher production volumes may necessitate larger or more robust machines to handle the increased workload and maintain consistent quality.
-
Example of Machine Size:
- A 165-ton injection molding machine is an example of a mid-range machine, suitable for producing medium-sized parts with moderate complexity.
-
Importance of Correct Sizing:
- Selecting the right size machine is crucial for achieving optimal production efficiency and part quality.
- An undersized machine may not provide sufficient clamping force, leading to defects in the final product.
- An oversized machine may result in unnecessary energy consumption and higher operational costs.
-
Considerations for Purchasers:
- Application Requirements: Evaluate the specific needs of your application, including the size and complexity of the parts you intend to produce.
- Future Scalability: Consider potential future needs and whether the machine can accommodate larger or more complex parts if your production requirements evolve.
- Energy Efficiency: Larger machines consume more energy, so it's important to balance the need for clamping force with energy efficiency considerations.
By carefully considering these factors, you can select the appropriate injection molding machine size that meets your production needs while optimizing efficiency and cost-effectiveness.
Summary Table:
Factor | Details |
---|---|
Clamping Force Range | 1 ton to 1000+ tons |
Part Size/Complexity | Larger, complex parts require higher clamping force |
Production Volume | Higher volumes may need larger machines for consistent quality |
Example Machine | 165-ton machine for medium-sized, moderately complex parts |
Importance of Sizing | Correct sizing ensures efficiency, quality, and cost-effectiveness |
Key Considerations | Application needs, future scalability, and energy efficiency |
Ready to find the perfect injection molding machine for your needs? Contact our experts today!