Copper brazing typically requires a temperature range that ensures the filler metal melts and flows properly while avoiding damage to the base material. The optimal temperature range for brazing copper in a hydrogen atmosphere is usually between 1,100 and 1,500°F. It is essential to select the lowest possible temperature within this range, typically at least 25°C (50°F) above the liquidus temperature of the braze alloy, to ensure a strong joint without overheating the copper. This approach balances the need for effective brazing with the preservation of the base material's integrity.
Key Points Explained:
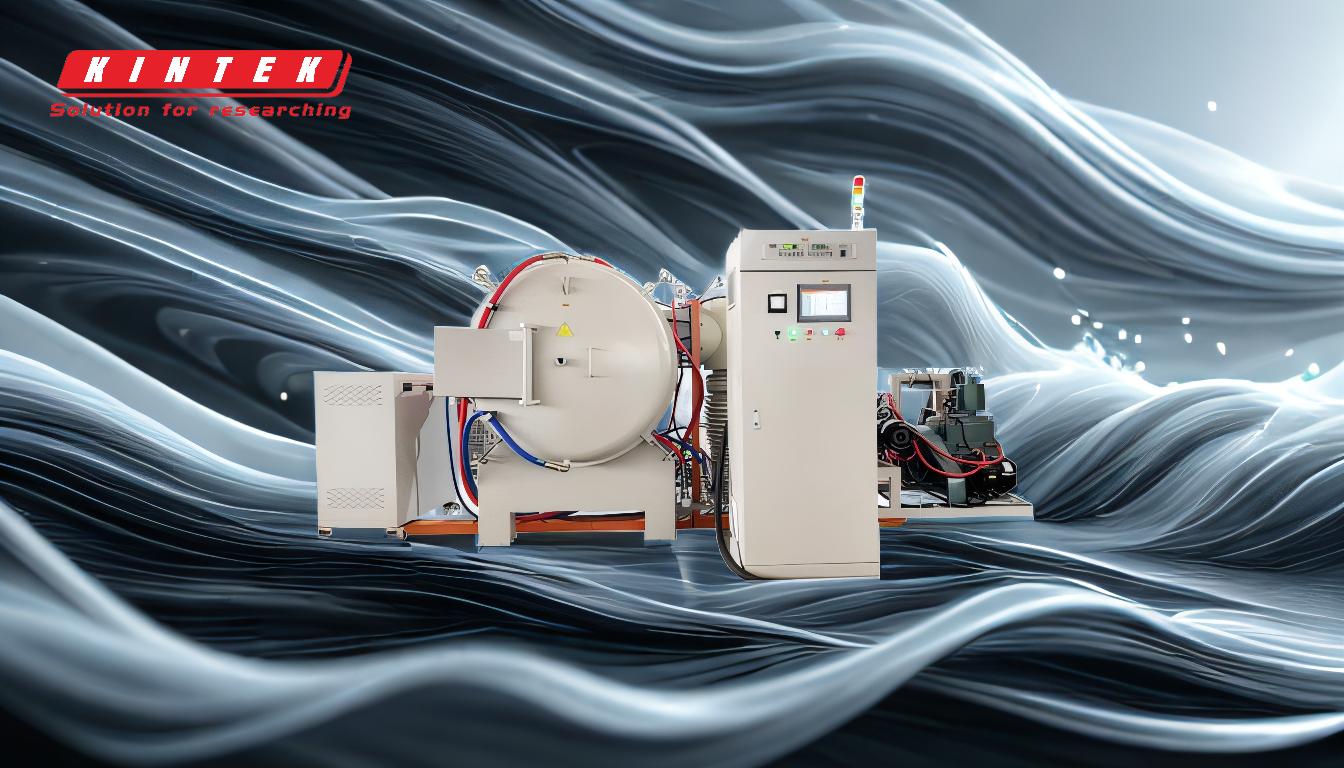
-
Optimal Temperature Range for Copper Brazing:
- The recommended temperature range for brazing copper is 1,100 to 1,500°F. This range ensures that the filler metal melts and flows properly, creating a strong bond between the copper pieces.
- Brazing in a hydrogen atmosphere is often preferred because it reduces oxidation and improves the quality of the joint.
-
Importance of Selecting the Lowest Possible Temperature:
- It is crucial to choose the lowest possible temperature within the recommended range to avoid overheating the copper base material. Overheating can weaken the copper or cause it to warp.
- The temperature should be at least 25°C (50°F) above the liquidus temperature of the braze alloy. The liquidus temperature is the point at which the alloy becomes completely liquid, ensuring proper flow and bonding.
-
Role of the Liquidus Temperature:
- The liquidus temperature of the braze alloy is a critical factor in determining the brazing temperature. Staying slightly above this temperature ensures that the filler metal flows smoothly and fills the joint completely.
- Exceeding the liquidus temperature by a small margin (25°C or 50°F) is sufficient to achieve a strong bond without risking damage to the copper.
-
Benefits of Brazing in a Hydrogen Atmosphere:
- Brazing in a hydrogen atmosphere helps to reduce oxidation on the copper surfaces, which can interfere with the bonding process.
- This environment also improves the wettability of the filler metal, ensuring better adhesion and a more reliable joint.
-
Practical Considerations for Copper Brazing:
- Always use a thermocouple or temperature sensor to monitor the brazing temperature accurately.
- Ensure that the copper surfaces are clean and free of contaminants before brazing, as any impurities can weaken the joint.
- Choose a braze alloy that is compatible with copper and has a suitable liquidus temperature for the intended application.
By following these guidelines, you can achieve a strong, durable brazed joint in copper while minimizing the risk of damaging the base material.
Summary Table:
Key Factor | Details |
---|---|
Optimal Temperature Range | 1,100–1,500°F |
Hydrogen Atmosphere | Reduces oxidation, improves joint quality |
Liquidus Temperature | Stay 25°C (50°F) above for proper flow and bonding |
Temperature Monitoring | Use a thermocouple or sensor for accuracy |
Surface Preparation | Clean and contaminant-free surfaces for stronger joints |
Need expert advice on copper brazing? Contact us today to achieve flawless results!