Heat treatment of aluminum involves heating the metal to specific temperatures to alter its physical and mechanical properties, such as hardness, strength, and ductility. The process typically includes stages like solution heat treatment, quenching, and aging. The exact temperature depends on the type of aluminum alloy and the desired outcome. For most aluminum alloys, solution heat treatment is performed at temperatures ranging from 450°C to 540°C (842°F to 1004°F), followed by rapid cooling (quenching) to lock in the desired microstructure. Artificial aging, if required, is done at lower temperatures, usually between 120°C and 200°C (248°F to 392°F). Understanding these temperature ranges is critical for achieving the desired material properties in aluminum components.
Key Points Explained:
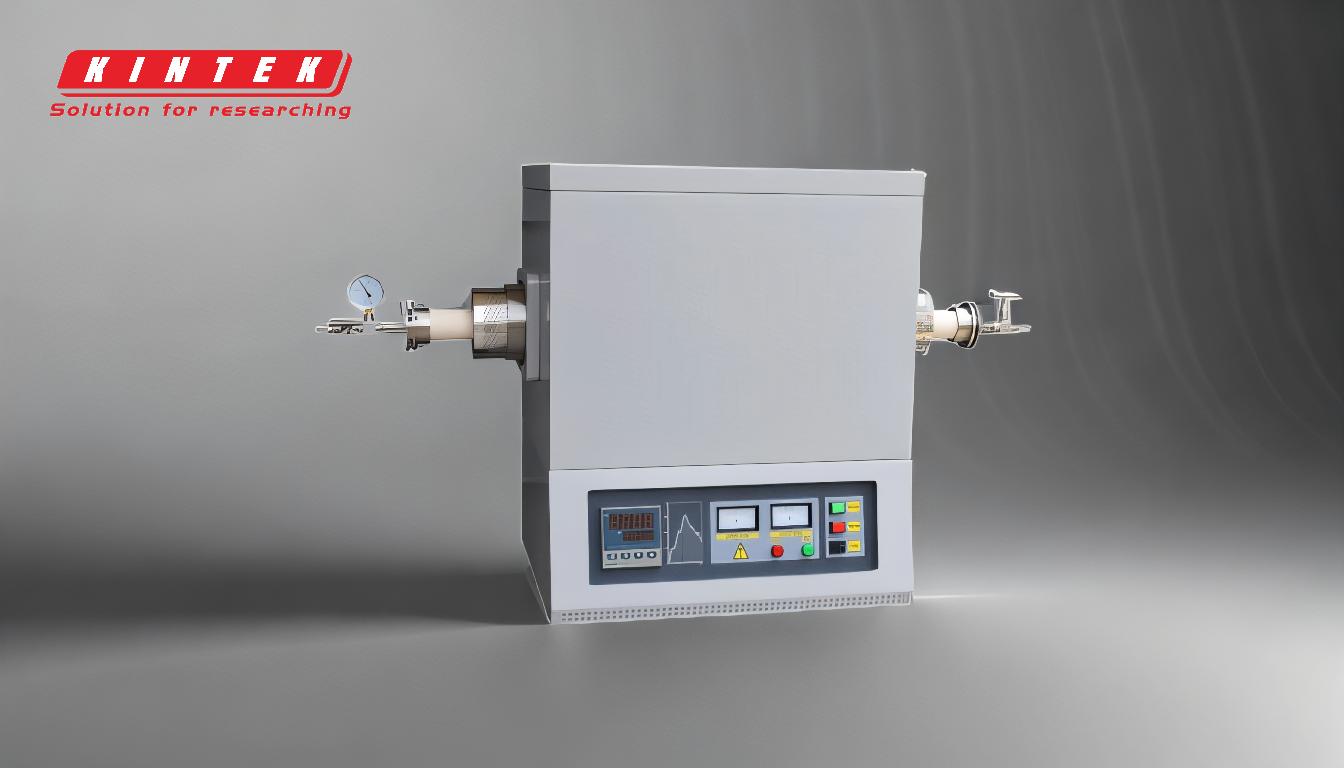
-
Purpose of Heat Treatment in Aluminum
Heat treatment is used to enhance the mechanical properties of aluminum alloys, such as strength, hardness, and resistance to wear. It is a critical process in industries like aerospace, automotive, and construction, where aluminum components must meet specific performance standards. -
Solution Heat Treatment Temperature
- Solution heat treatment involves heating the aluminum alloy to a temperature where the alloying elements dissolve into the base metal.
- For most aluminum alloys, this temperature ranges from 450°C to 540°C (842°F to 1004°F).
- The exact temperature depends on the alloy composition. For example, 6061 aluminum alloy is typically heated to around 530°C (986°F) during solution heat treatment.
-
Quenching Process
- After solution heat treatment, the aluminum is rapidly cooled (quenched) to room temperature.
- Quenching is usually done using water, air, or other cooling mediums to lock in the dissolved alloying elements and prevent precipitation.
- This step is crucial for achieving a supersaturated solid solution, which is necessary for subsequent aging.
-
Aging Treatment
- Aging is the final step in the heat treatment process and can be either natural or artificial.
- Natural aging occurs at room temperature over several days or weeks.
- Artificial aging involves heating the aluminum to lower temperatures, typically between 120°C and 200°C (248°F to 392°F), for a specific duration to achieve the desired hardness and strength.
- For example, 7075 aluminum alloy is often artificially aged at 120°C (248°F) for 24 hours.
-
Factors Influencing Heat Treatment Temperature
- Alloy Composition: Different aluminum alloys have varying heat treatment requirements. For instance, 2xxx series alloys (copper-based) require higher temperatures than 6xxx series (magnesium-silicon-based).
- Desired Properties: The temperature and duration of heat treatment are tailored to achieve specific mechanical properties, such as tensile strength or ductility.
- Component Size and Shape: Thicker or more complex parts may require adjusted temperatures to ensure uniform heating and cooling.
-
Common Aluminum Alloys and Their Heat Treatment Temperatures
- 6061 Aluminum Alloy: Solution heat treatment at 530°C (986°F), followed by artificial aging at 175°C (347°F) for 8 hours.
- 7075 Aluminum Alloy: Solution heat treatment at 480°C (896°F), followed by artificial aging at 120°C (248°F) for 24 hours.
- 2024 Aluminum Alloy: Solution heat treatment at 495°C (923°F), followed by natural aging at room temperature.
-
Importance of Temperature Control
- Precise temperature control is essential during heat treatment to avoid defects such as overheating, which can cause grain growth and reduce strength.
- Underheating may result in incomplete dissolution of alloying elements, leading to suboptimal mechanical properties.
-
Applications of Heat-Treated Aluminum
- Heat-treated aluminum is used in high-performance applications, including aircraft structures, automotive components, and marine equipment.
- The enhanced properties make it suitable for environments requiring high strength-to-weight ratios and corrosion resistance.
By understanding these key points, a purchaser can make informed decisions about the heat treatment processes required for specific aluminum alloys and applications. Proper heat treatment ensures that aluminum components meet the necessary performance standards and operational requirements.
Summary Table:
Process | Temperature Range | Key Details |
---|---|---|
Solution Heat Treatment | 450°C to 540°C (842°F to 1004°F) | Dissolves alloying elements; varies by alloy (e.g., 6061: ~530°C/986°F). |
Quenching | Rapid cooling to room temp | Uses water, air, or other mediums to lock in microstructure. |
Aging (Artificial) | 120°C to 200°C (248°F to 392°F) | Enhances hardness and strength; duration varies (e.g., 7075: 120°C for 24h). |
Natural Aging | Room temperature | Occurs over days/weeks; no additional heating required. |
Need precise heat treatment solutions for your aluminum components? Contact our experts today!