The temperature at which steel should be annealed depends on the type of steel and the desired outcome of the annealing process. Generally, annealing involves heating the steel to a temperature above its critical point (typically between 700°C and 900°C for most carbon steels), holding it at that temperature to allow the microstructure to transform, and then cooling it slowly to achieve a soft, ductile state. The exact temperature and cooling rate vary based on the steel's composition, such as carbon content, and the specific application requirements. Proper annealing reduces internal stresses, improves machinability, and enhances the material's workability.
Key Points Explained:
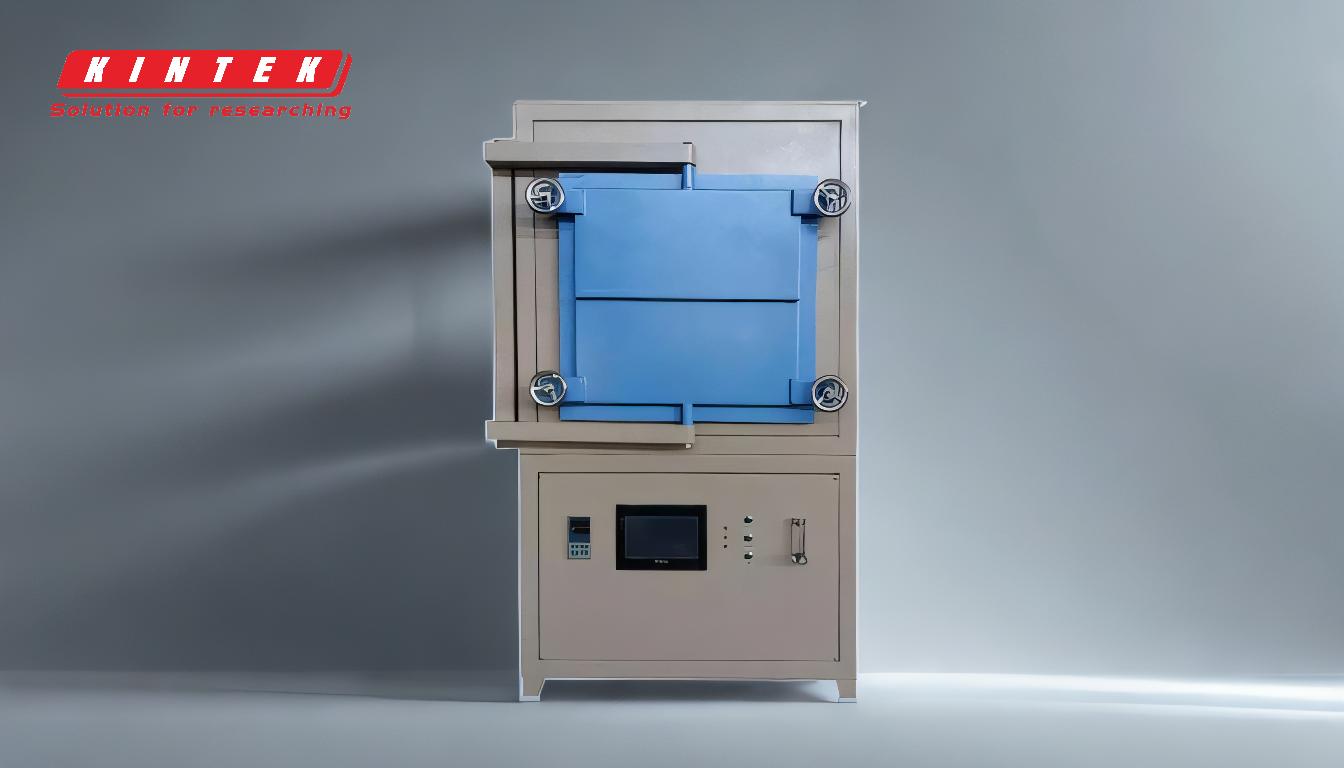
-
Purpose of Annealing:
- Annealing is a heat treatment process used to soften steel, improve its ductility, and reduce internal stresses. This makes the material easier to machine, form, or work with in subsequent processes.
-
Critical Temperature Range:
- The annealing temperature for steel typically ranges between 700°C and 900°C, depending on the type of steel. This range is above the steel's critical temperature, where the microstructure transforms from ferrite and pearlite to austenite.
-
Types of Steel and Their Annealing Temperatures:
- Low-Carbon Steels: Annealed at around 700°C to 800°C. These steels have less than 0.25% carbon content and are relatively easy to anneal.
- Medium-Carbon Steels: Annealed at 750°C to 850°C. These steels contain 0.25% to 0.60% carbon and require slightly higher temperatures for effective annealing.
- High-Carbon Steels: Annealed at 800°C to 900°C. These steels have a carbon content above 0.60% and need higher temperatures to achieve the desired softness and ductility.
- Alloy Steels: The annealing temperature varies based on the alloying elements (e.g., chromium, nickel, or manganese). Some alloy steels may require temperatures up to 950°C.
-
Holding Time:
- After reaching the target temperature, the steel must be held at that temperature for a sufficient duration to ensure uniform heating and complete transformation of the microstructure. The holding time depends on the thickness and size of the steel component but typically ranges from 1 to 4 hours.
-
Cooling Rate:
- Slow cooling is essential for effective annealing. The steel is usually cooled in the furnace at a controlled rate of 10°C to 30°C per hour until it reaches room temperature. This slow cooling prevents the formation of hard, brittle structures like martensite.
-
Importance of Temperature Control:
- Precise temperature control is critical during annealing. Overheating can lead to grain growth, which weakens the steel, while insufficient heating may not fully transform the microstructure, leaving the material too hard.
-
Applications of Annealed Steel:
- Annealed steel is used in applications requiring high ductility and machinability, such as:
- Manufacturing of automotive components.
- Production of tools and dies.
- Fabrication of structural parts in construction.
- Annealed steel is used in applications requiring high ductility and machinability, such as:
-
Equipment for Annealing:
- Annealing is typically performed in a muffle furnace or other controlled-atmosphere furnaces to ensure uniform heating and prevent oxidation or decarburization of the steel surface.
-
Post-Annealing Processes:
- After annealing, the steel may undergo additional processes such as tempering or stress relieving, depending on the final application requirements.
-
Safety Considerations:
- Proper safety measures must be taken during annealing, including the use of protective gear, adequate ventilation, and adherence to furnace operating guidelines to prevent accidents or material damage.
By understanding these key points, you can determine the appropriate annealing temperature and process for specific types of steel, ensuring optimal material properties for your application.
Summary Table:
Steel Type | Annealing Temperature | Key Characteristics |
---|---|---|
Low-Carbon Steel | 700°C to 800°C | <0.25% carbon, easy to anneal |
Medium-Carbon Steel | 750°C to 850°C | 0.25% to 0.60% carbon, requires higher heat |
High-Carbon Steel | 800°C to 900°C | >0.60% carbon, needs high heat for softness |
Alloy Steel | Up to 950°C | Varies based on alloying elements |
Need help determining the right annealing temperature for your steel? Contact our experts today for personalized guidance!